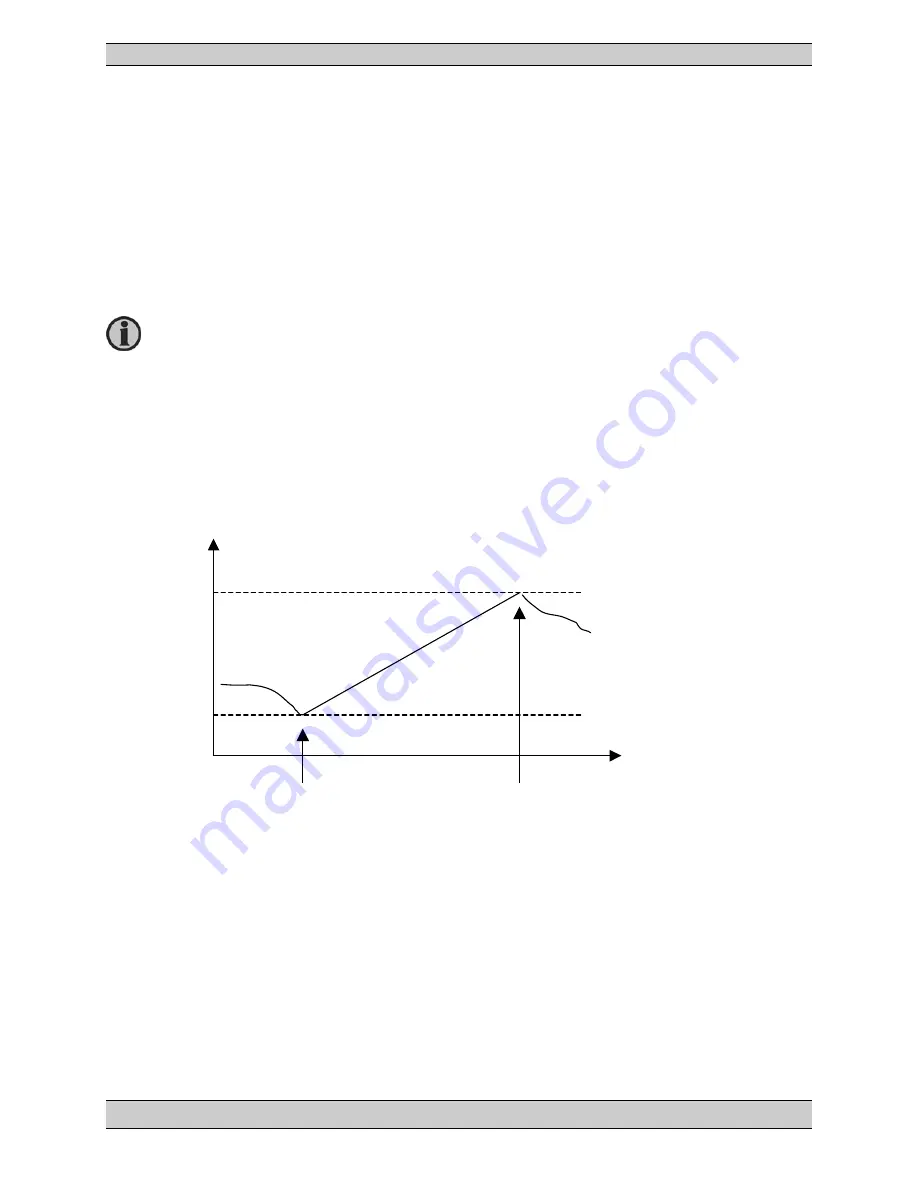
MEC 310 GENSET CONTROLLER
PM075 REV 2 09/08/20
Page 59
THOMSON TECHNOLOGY
Fuel pump logic
The fuel pump logic is used in order to start and stop the fuel supply pump to maintain the fuel level in
the service tank at predefined levels. The start and stop limits are detected from the VDO 1 input.
Start level, factory setting at 20% 6551
Stop level, factory setting at 80% 6552
•
Start level, relay 2 activates
•
Stop level, relay 2 deactivates
Fuel pump start level
Fuel level
80%
20%
Time
Fuel service tank level
Fuel pump stop level
The fuel pump relay is an NO relay and is configured to relay 2 by default. This
configuration cannot be changed. If other alarm functions have been configured
to relay 2, and the fuel logic is activated, then a
relay channel error
alarm will
occur. Please make sure that relay 2 is configured to Fuel Pump.