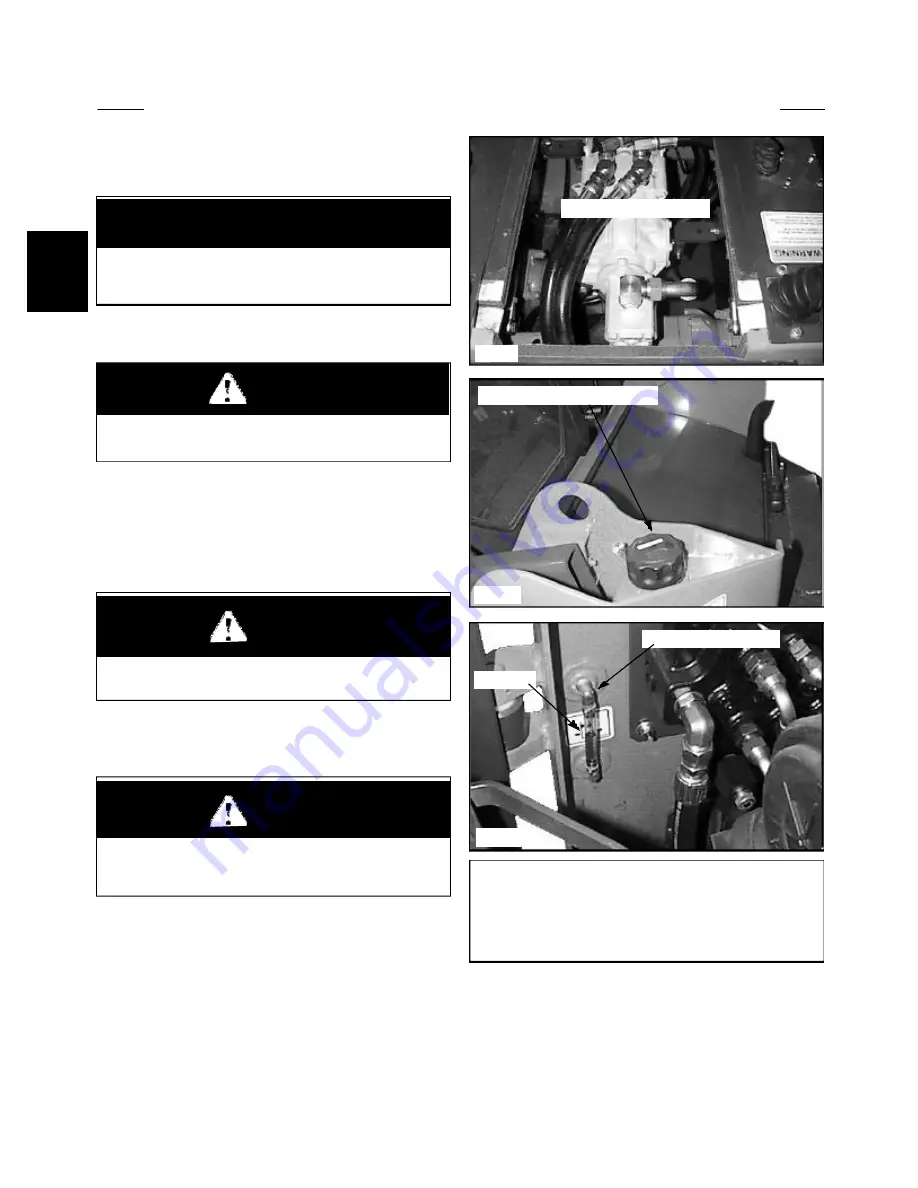
2-20
2
TANDEM PUMP REPLACEMENT 2.10
14 Reinstall the steering control linkages and locks as
outlined in Section 4. ( fig. C1857 )
15 Fill the hydraulic oil reservoir to the proper level.
16 Follow the start up procedure outlined in section 2.8
before attempting to start the loader.
17 The start up must be made with the loader raised
securely from the ground. Changing the pumps and the
steering control linkages has affected the neutral adjust-
ment. Failure to raise the loader clear of the ground may
result in the loader engaging in motion and possibly caus-
ing serious injury.
18 Start the loader and check for leaks. Make repairs as
necessary and replenish the hydraulic oil reservoir. Never
use your hands to check for hydraulic leaks.
19 Make adjustments to the steering controls, steering
locks, and restraint bar cables as required. Follow the pro-
cedures for control adjustments in Section 4
To prevent personal injury never make repairs to
the hydraulic system while the engine is operating.
This start-up procedure must be made with the
loader securely raised off the ground.
Use caution when dealing with hydraulic fluid under
pressure. Escaping fluid under pressure can pene-
trate the skin and cause serious injury.
IMPORTANT
Follow the start up procedure outlined in section 2.8
upon restarting after pump repairs or replacement.
C1857
C1879
C1878
Fill level
Reservoir sight gauge
Hydraulic reservoir filler cap
Replace control linkage
NOTE:
NOTE:
The 137/ 153 use a Sauer Danfoss M44 Tandem
Pump. The 1300 /135 use a M35 Tandem Pump.
WARNING
WARNING
WARNING