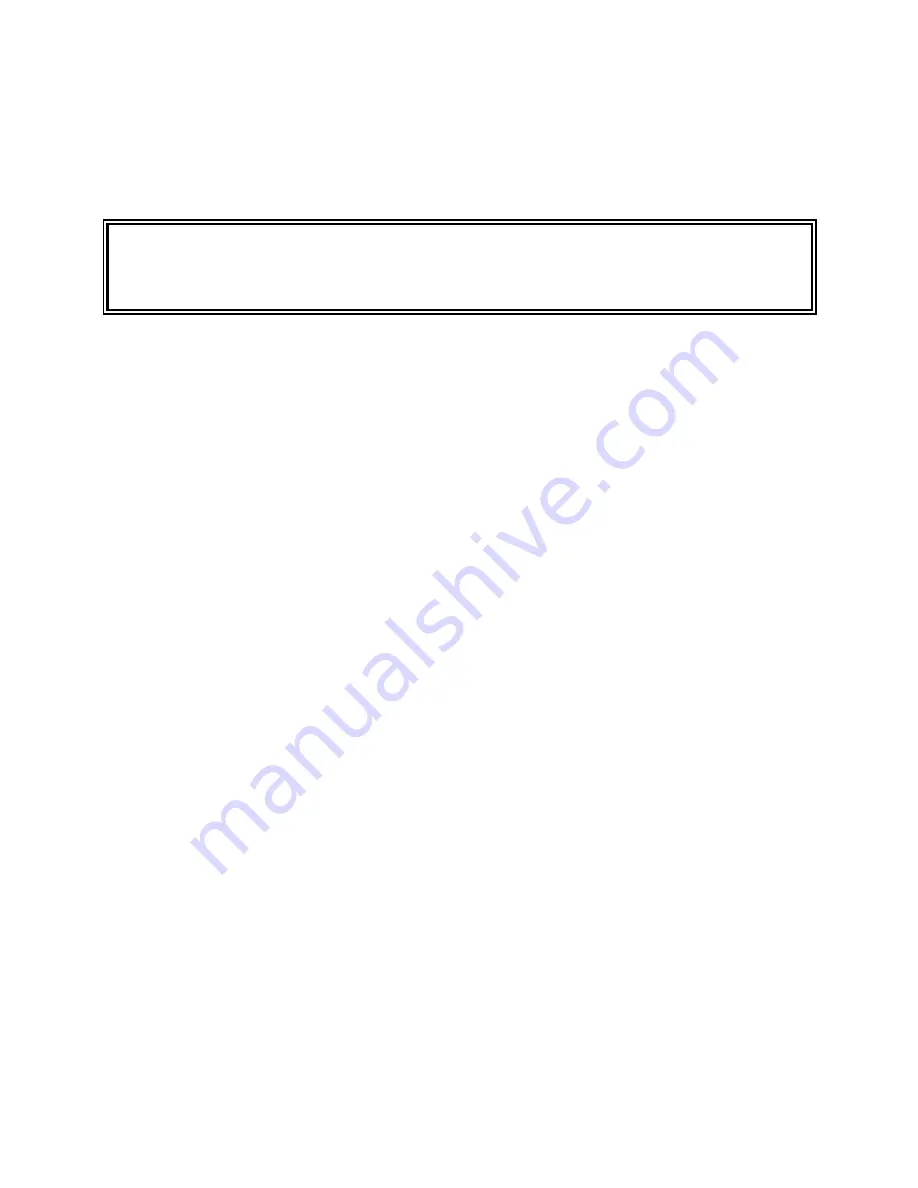
THERMOSALD
UPSCR10030-M-V3
UPSCR10045-M-V3
UPSCR10060-M-V3
UPSCR10090-M-V3
(08/2000)
TEMPERATURE CONTROLLER
for
IMPULSE HEAT-SEALING
(automatic calibrating system)
MAINTENANCE & OPERATIONS MANUAL
HARDWARE MOD. M
SOFTWARE V. 3
3E S.r.l.
-
Via del Maccabreccia 37/a - 40012 LIPPO DI CALDERARA ( BOLOGNA )
Tel. ++39 051 6466225 Fax ++39 051 6426252
e-Mail : mail@3e3e Website : http://www.3e3e3e.com