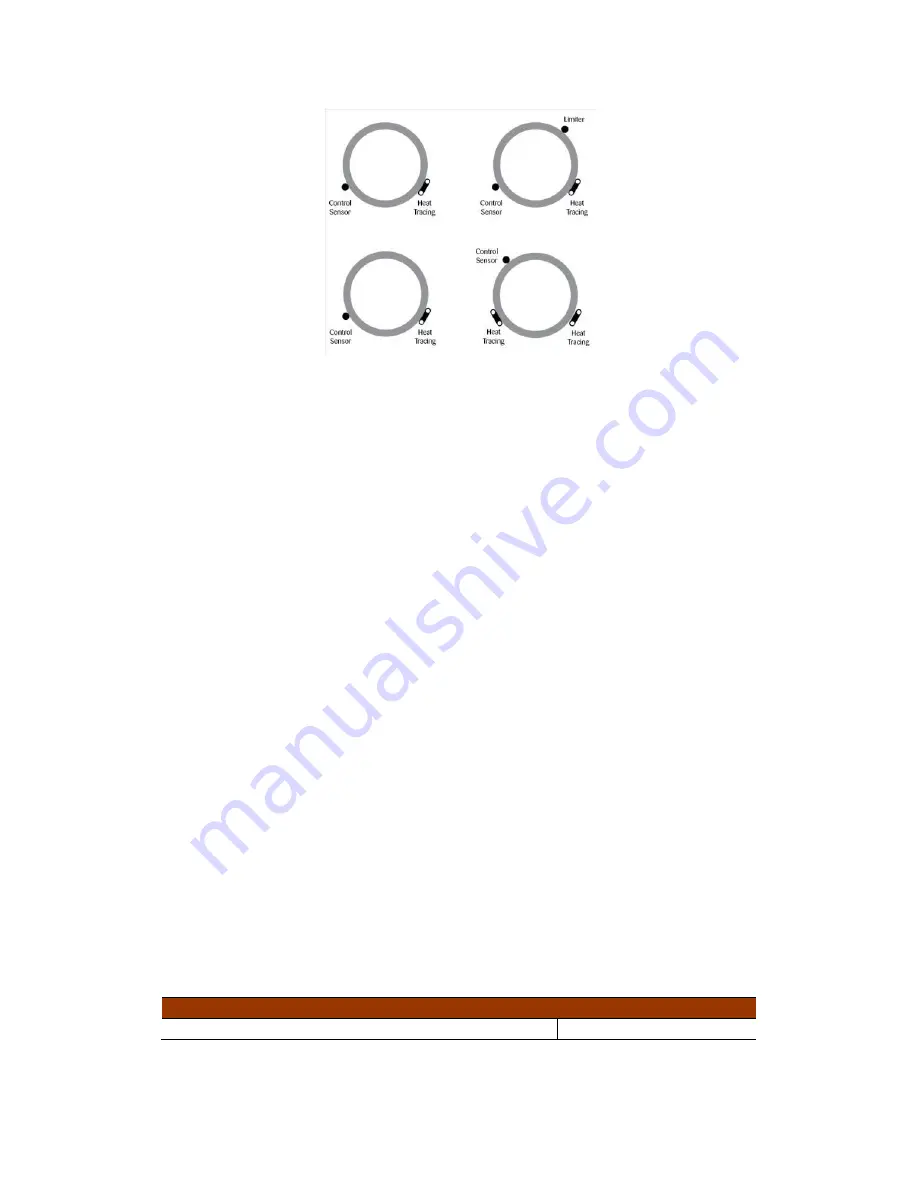
13
Figure 4.1:
RTD Sensor Location
Where RTD sensors are installed on the process piping, follow the guidelines
above. In special cases where the limiting temperature sensor is to be installed
on the heater itself, it is important to recognize that an offset should be
anticipated in the trip set-point to allow for sensor reading error and overshoot.
As a general rule, field RTD wiring and power wiring should not be routed in the
same conduit or proximity in a tray as the temperature signals can become
distorted and result in improper readings.
4.3 Power Distribution Wiring and Breakers
All field power wiring materials used shall be suitable for the intended service and
shall be rated for insulation service temperatures up to and exceeding 221°F
(105°C) unless higher values are otherwise noted in project specifications.
Power supply wiring from the power transformers to the power distribution panel
and distribution wiring to the heat trace circuits shall be rated for the heat trace
use voltage or higher and shall be of a sufficiently large wire size to minimize
voltage drop. Heat trace circuit breakers should be selected based on the type of
heat trace used, the service voltage, and the circuit current draw characteristics.
It is especially important when using self-regulating trace heaters to make sure
that the circuit breaker response curve type is coordinated with the startup
characteristic of the trace heater in a cold start condition. TCM2 controller circuit
breakers should have current ratings no higher than 15 A. In addition to the
controller circuit breaker, every heat trace circuit shall be provided with a circuit
breaker as a means for disconnection. All circuit breakers shall be easily
identifiable and accessible. All distribution wiring connections should be
tightened using a torque indicating screw driver to the levels indicated in
Table
4.1
.
Table 4.1:
Recommended Torque Values
Location of Terminals
Torque Values (Typical)*
Distribution Equipment
13.2 to 15.9 in. lbs. 1.49 to 1.80 N-m