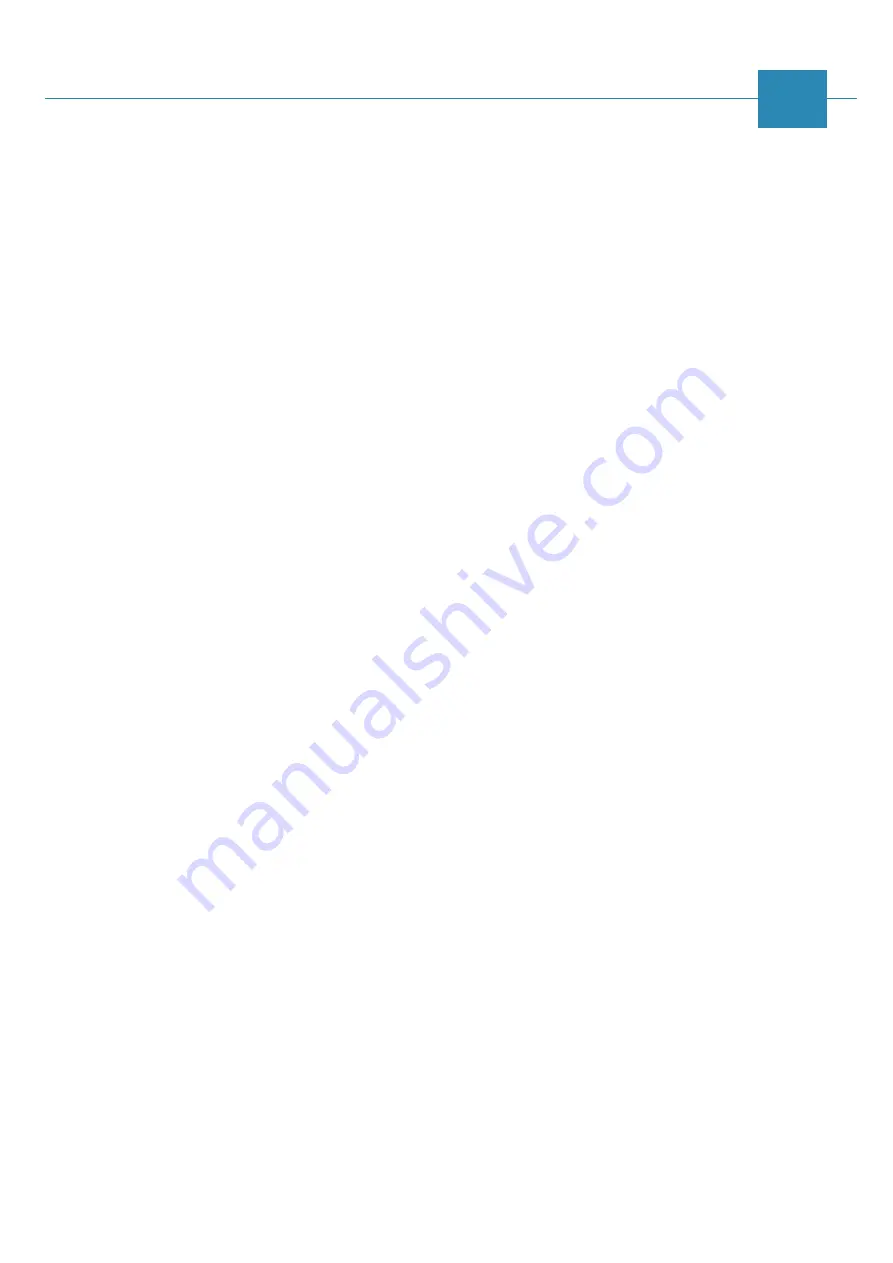
Thermo Electron LED GmbH
Heratherm 1-1
1
Safety Notes
Basic Operating Precautions
These operating instructions describe Heratherm ovens.
Heratherm ovens have been manufactured to the latest state of the art and been tested
thoroughly for flawless functioning prior to shipping. However, the oven may present
potential hazards, particularly if it is operated by inadequately trained personnel or if it is not
used in accordance with the intended purpose. Therefore, the following must be observed for
the sake of accident prevention:
• Heratherm ovens must be operated by adequately trained and authorized professional
personnel.
• Heratherm ovens must not be operated unless these operating instructions have been fully
read and understood.
• The present operating instructions, applicable safety data sheets, plant hygiene guidelines
and the corresponding technical rules issued by the operator shall be used to create written
procedures targeted at personnel working with the subject matter device, detailing:
• the safety precautions to be taken when processing specific agents,
• the measures to be taken in case of accidents.
• Repair work on the oven must be carried out only by trained and authorized expert
personnel.
• The contents of these operating instructions are subject to change at any time without
further notice.
• Concerning translations into foreign languages, the German version of these operating
instructions is binding.
• Keep these operating instructions close to the oven so that safety instructions and
important information are always accessible.
• Should you encounter problems that are not detailed adequately in these operating
instructions, please contact Thermo Electron LED GmbH immediately for your own
safety.
Summary of Contents for Heratherm OGS 100
Page 1: ......
Page 6: ...Contents 4 Heratherm Thermo Scientific ...
Page 8: ...List of Figures 2 Heratherm Thermo Scientific ...
Page 34: ...Product Description Work Space Components 4 10 Heratherm Thermo Scientific ...
Page 46: ...Start up Connecting the RS 232 Interface 5 12 Heratherm Thermo Electron LED GmbH ...
Page 62: ...Handling and Control Settings 7 14 Heratherm Thermo Scientific ...
Page 64: ...Shut down Shutting the Oven Down 8 2 Heratherm Thermo Scientific ...
Page 68: ...Cleaning and Disinfection Wipe Spray Disinfection 9 4 Heratherm Thermo Scientific ...
Page 84: ...Device Log 15 2 Heratherm Thermo Scientific ...