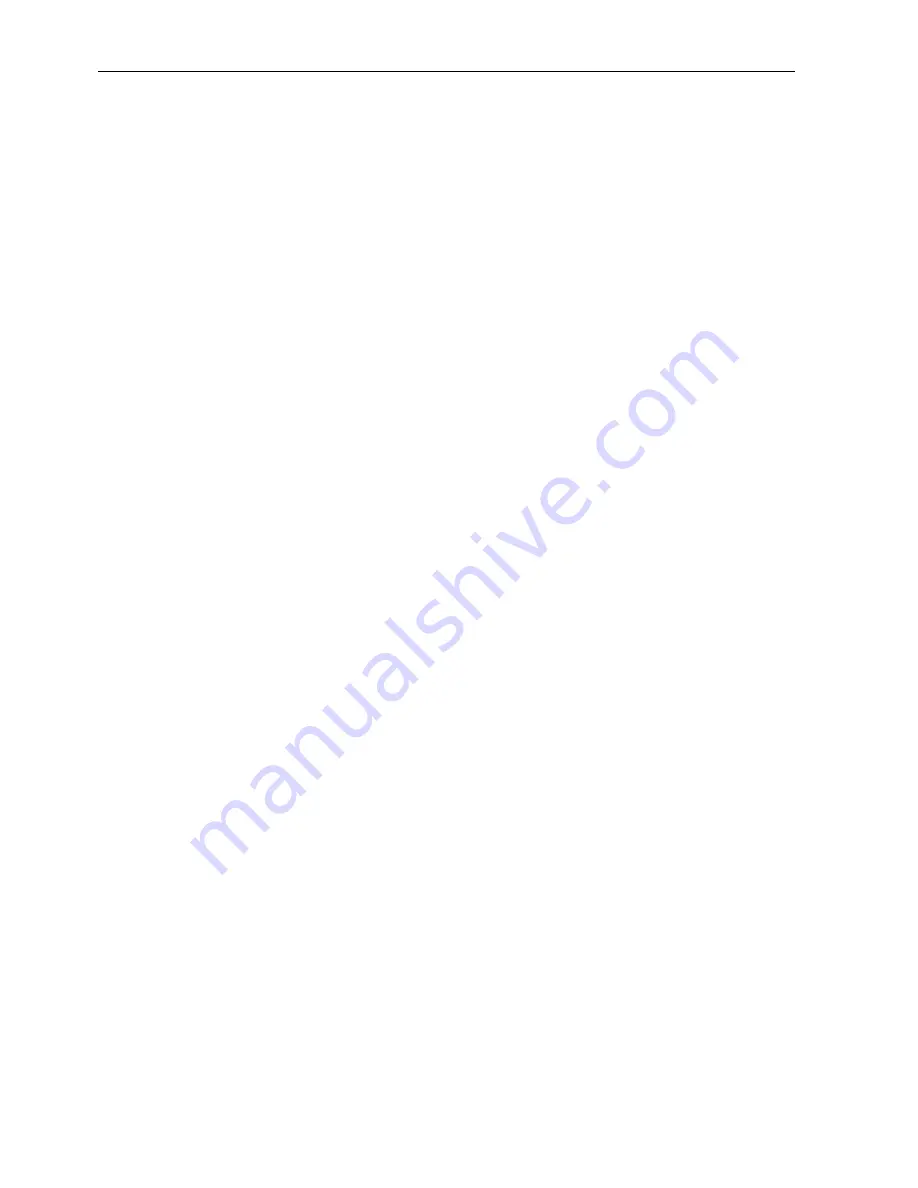
Engine Maintenance
54
5. Start the unit on low speed heat, let it run for
two minutes, and then shut it off.
6. Check the coolant level and add coolant if
necessary.
7. Repeat steps 5 and 6 until the coolant level
stabilizes.
Engine Thermostat
For the best engine operation, use a 180 F (82 C)
thermostat year-round.
Engine Fuel System
The TK 486 engine is a direct injection diesel that
uses an in-line injection pump.
The components of the fuel system are:
1. Fuel tank
2. Inlet strainer (prefilter)
3. Fuel filter/water separator
4. Priming pump
5. Fuel transfer pump
6. Injection pump
7. Injection nozzles
The priming pump is used to manually draw fuel
from the tank up to the fuel pump if the unit
should run out of fuel.
Operation
Fuel is drawn from the fuel tank and through the
prefilter by the fuel transfer pump. The fuel
transfer pump delivers fuel to the fuel filter/water
separator. Two orifices in the filter head control
the pressure in the fuel system by allowing a
certain amount of fuel to return to the tank. One
orifice is located in the center of the filter head. It
bleeds off water. The other orifice is located
off-center on the filter head. It bleeds off air.
Filtered fuel passes through a line from the outlet
fitting on the filter base to the injection pump.
The injection pump plungers are activated by a
gear driven injection pump camshaft. The
governor sleeve and weight assembly is mounted
on the end of the pump camshaft. The governor’s
speed requirements are relayed to the injection
pump through a linkage arrangement located in
the rear cover. The injection pump raises the
pressure of the fuel and meters the correct amount
of fuel to the nozzle at the correct time. The
increased fuel pressure will lift the spring loaded
nozzle to admit fuel into the combustion chamber.
Injection pump leakage, injection nozzle overflow
and excess fuel from the fuel filter orifice are then
all sent back to the fuel tank in the return line.
Maintenance
The injection pump and fuel transfer pump are
relatively trouble-free and if properly maintained
will usually not require major service repairs
between engine overhauls.
Contamination is the most common cause of fuel
system problems. Therefore, to ensure best
operating results, the fuel must be clean and fuel
tanks must be free of contaminants. Change the
fuel filter/water separator regularly and clean the
prefilter on the inlet side of the fuel transfer pump.
NOTE: The injection nozzles should be tested
(and repaired if necessary) at 10,000 hour
intervals when used in normal conditions.
Normal conditions are considered to be the use
of clean high quality fuel, no used oil blending,
and regular maintenance of the fuel system
according to the Maintenance Inspection
Schedule. Refer to the TK 482 and TK 486
Overhaul Manual TK 50136 for injection nozzle
testing and repair procedures.
Whenever the fuel system is opened, take the
following precautions to prevent dirt from
entering the system:
1. Cap all fuel lines.
2. Work in a relatively clean area whenever
possible.
3. Complete the work in the shortest possible
time.
Any major injection pump or nozzle repairs
should be done by a quality diesel injection
service shop. The necessary service equipment
and facilities are not found in most engine rebuild
shops because of the large investment required.
Summary of Contents for Spectrum DE 30-2
Page 4: ...4...
Page 12: ...Safety Precautions 12...
Page 16: ...Specifications 16...
Page 31: ...Unit Description 31 1 Access Panels 2 Defrost Dampers Figure 12 Back View of Unit 1 2 AGA215...
Page 42: ...Operating Instructions 42...
Page 48: ...Electrical Maintenance 48...
Page 106: ...Structural Maintenance 106...
Page 110: ...Mechanical Diagnosis 110...
Page 114: ...Remote Evaporator Specifications 114...
Page 116: ...Remote Evaporator Maintenance Inspection Schedule 116...
Page 122: ...Remote Evaporator Electrical Maintenance 122...
Page 126: ...Remote Evaporator Refrigeration Service Operations 126...
Page 128: ...Remote Evaporator Structural Maintenance 128...
Page 130: ...Remote Evaporator System Diagnosis 130...
Page 134: ...Wiring and Schematic Diagrams Index 134...
Page 135: ...135 Schematic Diagram Page 1 of 2...
Page 136: ...136 Schematic Diagram Page 2 of 2...
Page 137: ...137 Wiring Diagram Page 1 of 4...
Page 138: ...138 Wiring Diagram Page 2 of 4...
Page 139: ...139 Wiring Diagram Page 3 of 4...
Page 140: ...140 Wiring Diagram Page 4 of 4...