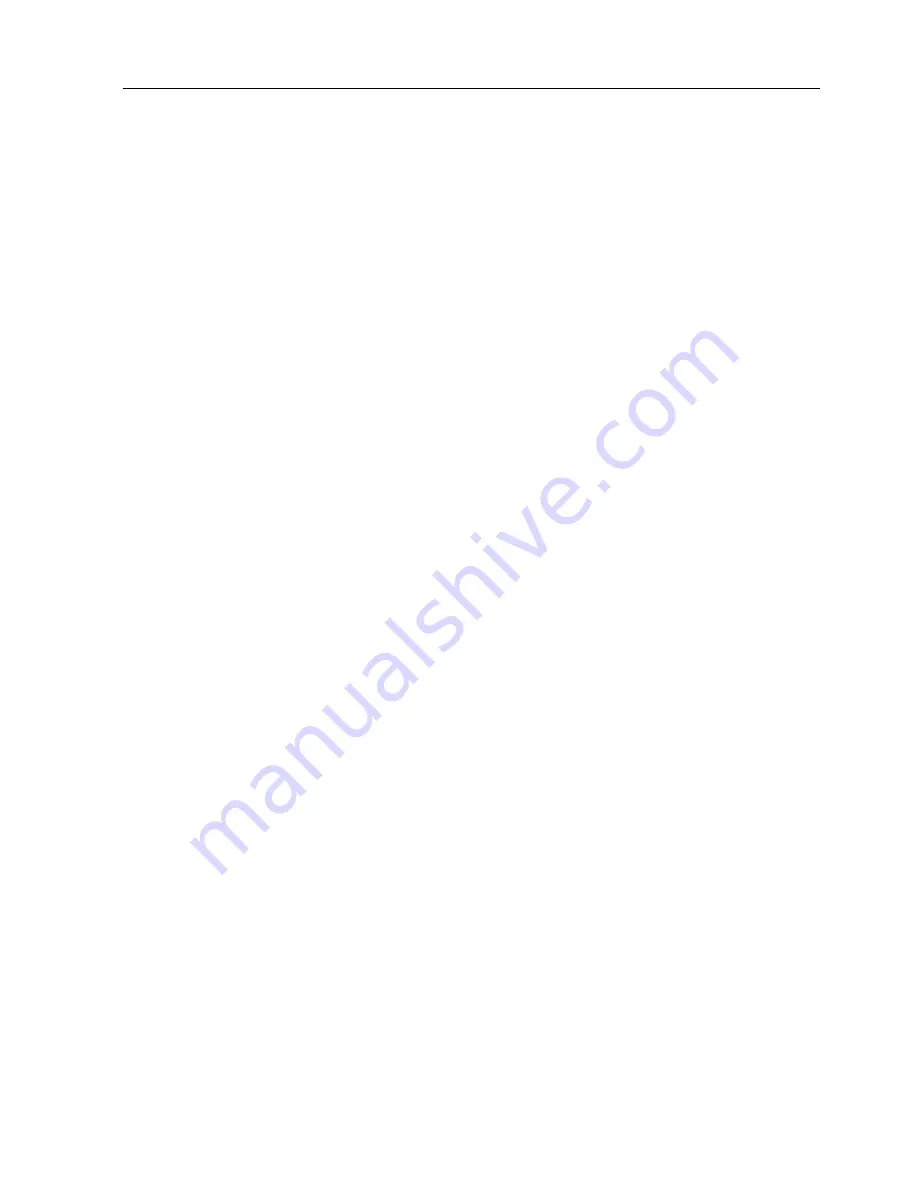
79
Refrigeration Maintenance
NOTE: The following procedures involve
servicing the refrigeration system. Some of these
service procedures are regulated by Federal, and
in some cases, by State and Local laws.
In the USA all regulated refrigeration service
procedures must be performed by an EPA
certified technician, using approved equipment
and complying with all Federal, State and Local
laws.
Refrigerant Charge
Testing the Refrigerant Charge with
an Empty Trailer
If the unit has an insufficient charge of refrigerant,
the evaporators will be “starved” and the box
temperatures will rise even though the unit is
operating. The suction pressure will drop as the
refrigerant charge decreases. If the unit has an
overcharge of refrigerant, the unit may not cool
properly and the suction and discharge pressure
may be high. The charge may be determined by
inspection of the refrigerant through the receiver
tank sight glass with the following conditions
established:
1. Place a test box over each evaporator.
2. Install a gauge manifold.
3. Run all the evaporators on cool until the return
air temperature in each box is at 0 F (-18 C).
By allowing a box to leak a small amount, you
will be able to maintain 0 F (-18 C).
4. The suction pressure should be 13 to 18 psig
(90 to 124 kPa).
5. The discharge pressure should be 325 to
400 psig (2241 to 2758 kPa). If the pressure is
below this, it can be raised by covering a
portion of the roadside condenser grille with a
piece of cardboard to block condenser airflow.
6. Under these conditions, the ball should be
floating in the receiver tank sight glass. If
refrigerant is not visible in the receiver tank
sight glass, the unit is low on refrigerant.
Testing the Refrigerant Charge with
a Loaded Trailer
NOTE: This test determines if there is enough
refrigerant for the current temperatures, not if
there is a full charge of refrigerant.
1. Install a gauge manifold.
2. Run all the evaporators on cool.
3. Build up and maintain 325 to 400 psig (2241
to 2758 kPa) of discharge pressure. If the
pressure is below this, it can be raised by
covering the roadside condenser grille with a
piece of cardboard to block condenser air
flow.
4. Cool the compartments to lowest temperatures
required.
5. Check suction pressure. It should be 13 to
22 psig (90 to 152 kPa).
6. Under these conditions, the ball should be
floating in the receiver tank sight glass. If
refrigerant is not visible in the sight glass, the
unit is low on refrigerant.
Testing for an Overcharge
Use the following procedure to identify a unit
with an excessive refrigerant charge:
1. Install a gauge manifold on the compressor.
2. Operate the host unit in high speed with all the
evaporators in cool to stabilize system
pressures and reduce the compartment
temperatures to approximately 60 F (16 C) or
colder.
3. Observe discharge pressure and cover the
condenser to increase the discharge pressure
approximately 50 psig (345 kPa) above the
observed pressure. Do not allow the discharge
pressure to go above 350 psig (2413 kPa).
NOTE: If the ball and liquid level in the
receiver sight glass drops during step 3, the
unit is not overcharged and it is not
necessary to complete the procedure.
4. Remove the condenser cover to rapidly reduce
discharge pressure.
Summary of Contents for 002008
Page 4: ...4 ...
Page 30: ...Unit Description 30 Figure 9 Front View AJA920 ...
Page 31: ...Unit Description 31 1 Access Panels 2 Defrost Damper Figure 10 Back View 1 2 ARA104 ...
Page 114: ...Mechanical Diagnosis 114 ...
Page 116: ...Electric Standby Diagnosis 116 ...
Page 120: ...Remote Evaporator Specifications 120 ...
Page 122: ...Remote Evaporator Maintenance Inspection Schedule 122 ...
Page 128: ...Remote Evaporator Electrical Maintenance 128 ...
Page 132: ...Remote Evaporator Refrigeration Service Operations 132 ...
Page 134: ...Remote Evaporator Structural Maintenance 134 ...
Page 136: ...Remote Evaporator System Diagnosis 136 ...
Page 140: ...Index 140 ...
Page 142: ......
Page 143: ...143 Model 30 Schematic Diagram Page 1 of 2 ...
Page 144: ...144 Model 30 Schematic Diagram Page 2 of 2 ...
Page 145: ...145 Model 30 Wiring Diagram Page 1 of 4 ...
Page 146: ...146 Model 30 Wiring Diagram Page 2 of 4 ...
Page 147: ...147 Model 30 Wiring Diagram Page 3 of 4 ...
Page 148: ...148 Model 30 Wiring Diagram Page 4 of 4 ...
Page 149: ...149 Model 50 Schematic Diagram Page 1 of 2 ...
Page 150: ...150 Model 50 Schematic Diagram Page 2 of 2 ...
Page 151: ...151 Model 50 Wiring Diagram Page 1 of 5 ...
Page 152: ...152 Model 50 Wiring Diagram Page 2 of 5 ...
Page 153: ...153 Model 50 Wiring Diagram Page 3 of 5 ...