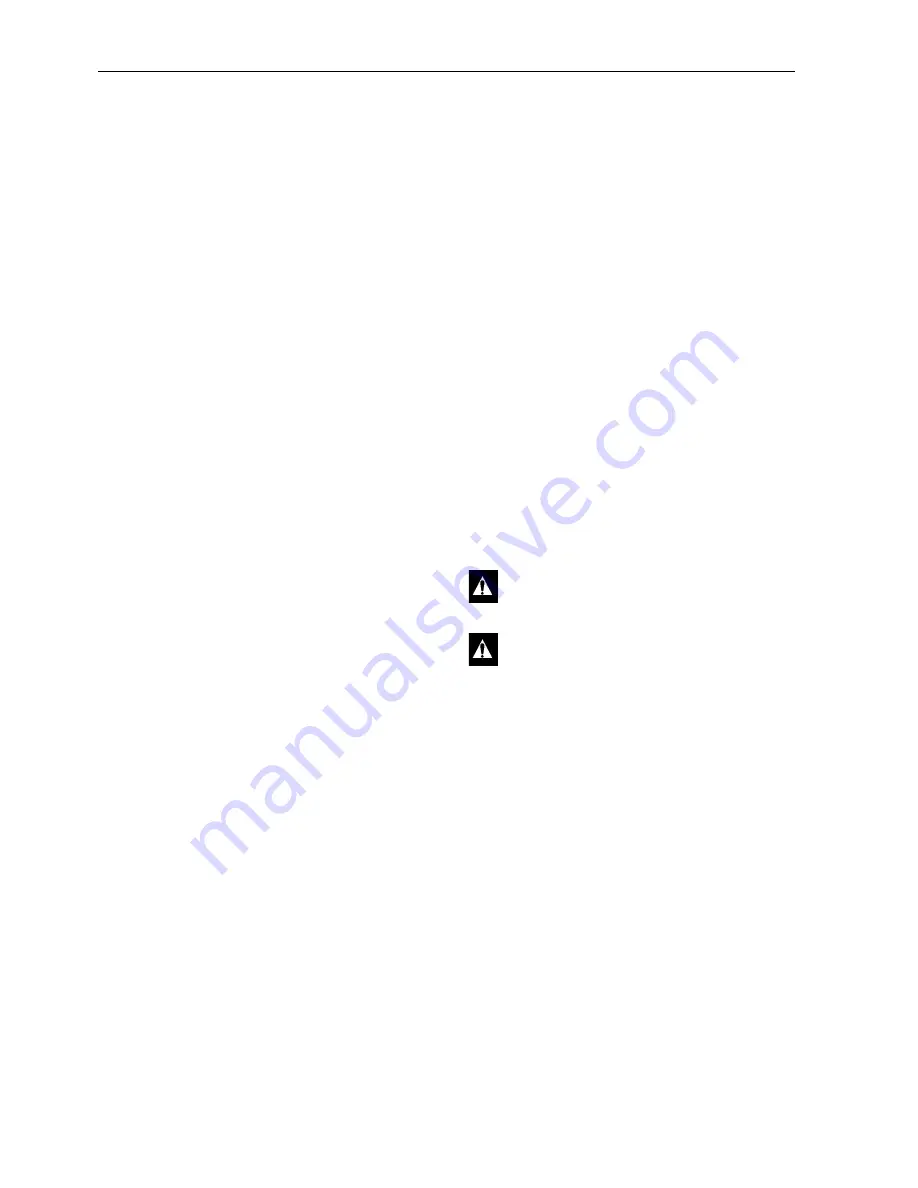
Operating Instructions
38
High Pressure Cutout:
The high pressure cutout is
a pressure sensitive switch that is located in the
compressor discharge manifold. If the discharge
pressure rises above 470 psi (3241 kPa), the
switch opens the 8D circuit to the fuel solenoid,
which stops the engine.
High Pressure Relief Valve:
The high pressure
relief valve is designed to relieve excess pressure
within the refrigeration system. The valve is a
spring-loaded piston that lifts off its seat when
refrigerant pressure exceeds 500 psi (3447 kPa).
The valve will reseat when the pressure drops to
400 psi (2758 kPa). The valve could possibly leak
refrigerant after it has relieved excess pressure.
Tapping the valve lightly may help the valve
reseat and seal properly. The valve is
non-repairable and requires no adjustment. If the
valve fails to reseat properly, remove the
refrigerant charge and unscrew and replace the
valve.
The high pressure relief valve is located on the
receiver tank. Its location is such that when the
pressure is expelled from the valve, it would be
directed away from anyone servicing the unit.
Low Oil Level Switch:
The low oil level switch
closes if the oil drops below a certain level and
stays closed for a specified time, the
microprocessor will shut the unit down and record
Alarm Code 66.
Preheat Buzzer:
The preheat buzzer sounds when
the CYCLE-SENTRY system energizes the glow
plugs. This should warn anyone near the unit that
the CYCLE-SENTRY system is about to start the
diesel engine.
Overload Relay—Manual Reset (Model 50):
An
overload relay protects the standby electric motor.
The overload relay opens the circuit to the electric
motor if the motor overloads for any reason (e.g.,
low line voltage or improper power supply) while
the unit is on electric standby operation.
Unit Operation
Manual Pretrip Inspection (Before
Starting Unit)
The following Manual Pretrip Inspection should
be completed before starting the unit and loading
the trailer. While the pretrip inspection is not a
substitute for regularly scheduled maintenance
inspections, it is an important part of the
preventive maintenance program designed to head
off operating problems and breakdowns before
they happen.
Fuel:
The diesel fuel supply must be adequate to
guarantee engine operation to the next check
point.
Engine Oil:
The engine oil level should be at the
FULL mark with the dipstick turned (threaded)
into oil pan. Never overfill.
Coolant:
The engine coolant must have antifreeze
protection to -30 F (-34 C). Alarm Code 37
indicates low coolant. Add coolant in the
expansion tank.
Battery:
The terminals must be clean and tight.
Belts:
The belts must be in good condition and
adjusted to the proper tensions.
Electrical:
The electrical connections should be
securely fastened. The wires and terminals should
be free of corrosion, cracks or moisture.
Structural:
Visually inspect the unit for leaks,
loose or broken parts and other damage. The
condenser and evaporator coils should be clean
and free of debris. Check the defrost drain hoses
and fittings to make sure they are open. Make sure
all the doors are latched securely.
CAUTION: Do not remove expansion
tank cap while coolant is hot.
CAUTION: Do not add “GREEN” or
“BLUE-GREEN” conventional coolant to
cooling systems using “RED” Extended
Life Coolant, except in an emergency. If
conventional coolant is added to Extended
Life Coolant, the coolant must be changed
after 2 years instead of 5 years.
Summary of Contents for 002008
Page 4: ...4 ...
Page 30: ...Unit Description 30 Figure 9 Front View AJA920 ...
Page 31: ...Unit Description 31 1 Access Panels 2 Defrost Damper Figure 10 Back View 1 2 ARA104 ...
Page 114: ...Mechanical Diagnosis 114 ...
Page 116: ...Electric Standby Diagnosis 116 ...
Page 120: ...Remote Evaporator Specifications 120 ...
Page 122: ...Remote Evaporator Maintenance Inspection Schedule 122 ...
Page 128: ...Remote Evaporator Electrical Maintenance 128 ...
Page 132: ...Remote Evaporator Refrigeration Service Operations 132 ...
Page 134: ...Remote Evaporator Structural Maintenance 134 ...
Page 136: ...Remote Evaporator System Diagnosis 136 ...
Page 140: ...Index 140 ...
Page 142: ......
Page 143: ...143 Model 30 Schematic Diagram Page 1 of 2 ...
Page 144: ...144 Model 30 Schematic Diagram Page 2 of 2 ...
Page 145: ...145 Model 30 Wiring Diagram Page 1 of 4 ...
Page 146: ...146 Model 30 Wiring Diagram Page 2 of 4 ...
Page 147: ...147 Model 30 Wiring Diagram Page 3 of 4 ...
Page 148: ...148 Model 30 Wiring Diagram Page 4 of 4 ...
Page 149: ...149 Model 50 Schematic Diagram Page 1 of 2 ...
Page 150: ...150 Model 50 Schematic Diagram Page 2 of 2 ...
Page 151: ...151 Model 50 Wiring Diagram Page 1 of 5 ...
Page 152: ...152 Model 50 Wiring Diagram Page 2 of 5 ...
Page 153: ...153 Model 50 Wiring Diagram Page 3 of 5 ...