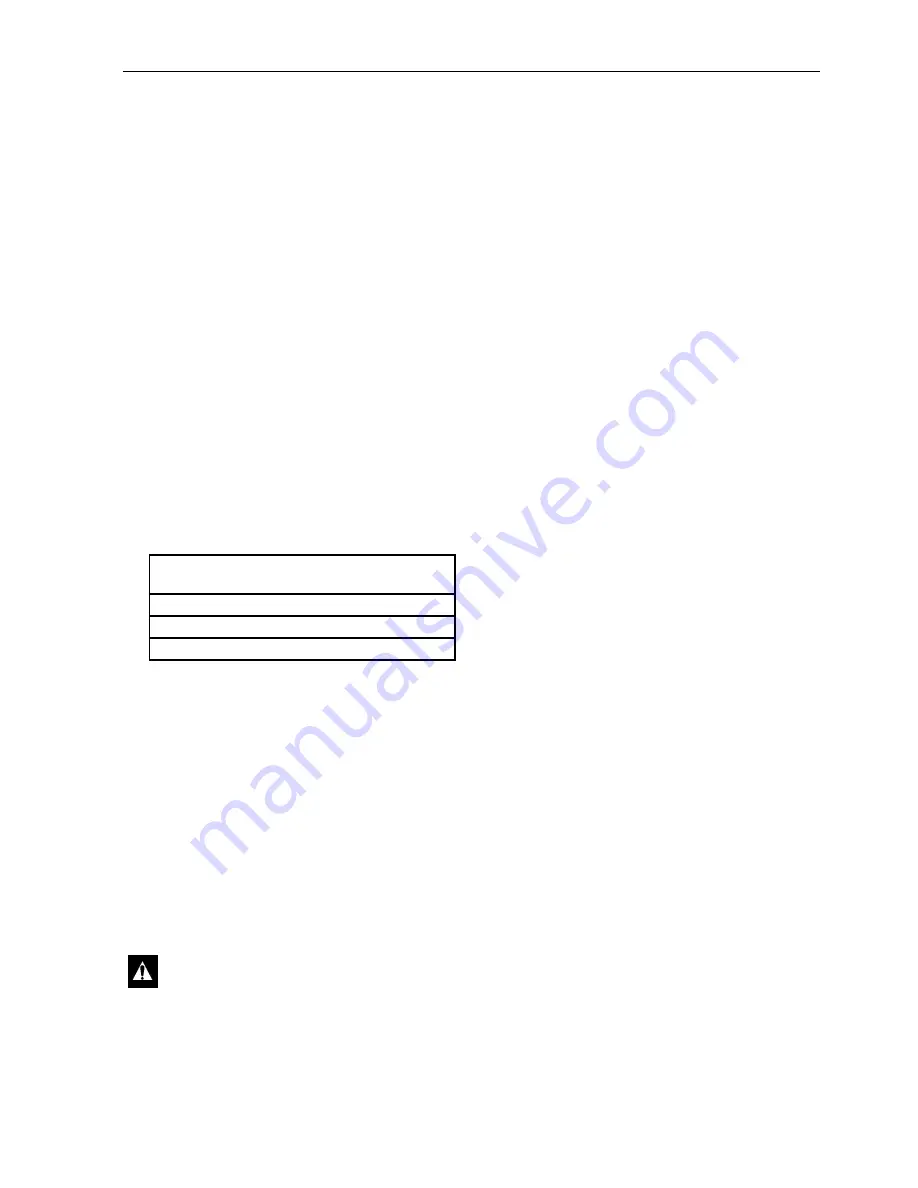
Structural Maintenance
109
Reassembly
1. Tap the new bearings on the shaft with a pipe.
2. Install new oil seals after replacing the bearing
races.
3. Replace the shaft in the housing. Install a new
seal in the retainer cap. Use the original shims
and replace the O-ring if needed.
4. Install the retainer cap assembly over the
shaft, then install the bolts.
5. Torque the bolts in a criss-cross pattern in
equal steps to 80 in-lb (9.04 N•m).
6. Lock the assembly in a vise and set up a dial
indicator to read end-play. To measure the
end-play, rotate the shaft while pushing in one
direction and set the dial indicator to ‘0’. Now
rotate the shaft and pull in the opposite
direction while reading the dial indicator.
End-play should be 0.001 to 0.005 in. (0.025
to 0.127 mm). If end-play is incorrect, use
different shims to obtain correct end-play.
7. After correct end-play is obtained, add oil for
the bearings.
8. Lock the assembly in a vise with the vent
facing up. Pour the oil (P/N 203-278) through
the top plug until it runs out of the side hole.
The assembly holds 2.5 oz (74 ml). Check the
condition of the O-ring used on the plugs and
replace if necessary. Install the top and side
plugs. Clean up any spillage.
9. Place the assembly on the workbench with the
vent up. Rotate the shaft by hand. The shaft
should be free enough to rotate without having
to hold the housing.
Idler Assembly
The unit is equipped with a one-piece idler
assembly that contains tapered roller bearings in a
sealed oil reservoir. This assembly does not
require any maintenance. There is a level plug and
a fill plug, but they are not normally used except
after removal and repair of the idler assembly. The
roadside end oil seal and the curbside end oil seal
should be checked during the pretrip inspection
for oil leakage. If there is any sign of leakage, the
idler assembly should be removed and repaired.
Idler Assembly Overhaul
Disassembly
1. Remove the idler assembly from the unit.
Remove both oil plugs and drain the oil from
the housing.
2. After draining the oil from the housing,
remove the four retaining bolts from the
curbside end of the assembly.
3. To remove the shaft from the assembly, tap the
opposite end of the shaft with a soft hammer.
After the shaft has been removed, clean all the
parts in clean solvent.
4. Using a punch, remove the oil seal from the
curbside end of the assembly. With the seal
removed, clean the housing in solvent.
5. Check the condition of the vent. If it is loose
or damaged, it must be repaired or replaced.
6. After all the parts are cleaned, inspect the
bearings and bearing races for wear or
damage.
7. To replace the bearings, first drive bearing off
shaft with a punch at notch in the base of the
shaft.
Reassembly
1. Install the new bearings on the shaft with a
pipe. Place the pipe over the shaft and drive
bearing down. Turn the shaft upside down,
and use the pipe to drive the other bearing
down.
2. Install a new oil seal on the curbside end of
the assembly after replacing the bearing race
and splash guard.
Shims available from the Service Parts
Department
0.020 in. (0.500 mm) Thermo King P/N 99-4231
0.007 in. (0.177 mm) Thermo King P/N 99-2902
0.005 in. (0.127 mm) Thermo King P/N 99-2901
CAUTION: When installing the fan shaft
assembly, make sure that the vent is
mounted facing up.
Summary of Contents for 002008
Page 4: ...4 ...
Page 30: ...Unit Description 30 Figure 9 Front View AJA920 ...
Page 31: ...Unit Description 31 1 Access Panels 2 Defrost Damper Figure 10 Back View 1 2 ARA104 ...
Page 114: ...Mechanical Diagnosis 114 ...
Page 116: ...Electric Standby Diagnosis 116 ...
Page 120: ...Remote Evaporator Specifications 120 ...
Page 122: ...Remote Evaporator Maintenance Inspection Schedule 122 ...
Page 128: ...Remote Evaporator Electrical Maintenance 128 ...
Page 132: ...Remote Evaporator Refrigeration Service Operations 132 ...
Page 134: ...Remote Evaporator Structural Maintenance 134 ...
Page 136: ...Remote Evaporator System Diagnosis 136 ...
Page 140: ...Index 140 ...
Page 142: ......
Page 143: ...143 Model 30 Schematic Diagram Page 1 of 2 ...
Page 144: ...144 Model 30 Schematic Diagram Page 2 of 2 ...
Page 145: ...145 Model 30 Wiring Diagram Page 1 of 4 ...
Page 146: ...146 Model 30 Wiring Diagram Page 2 of 4 ...
Page 147: ...147 Model 30 Wiring Diagram Page 3 of 4 ...
Page 148: ...148 Model 30 Wiring Diagram Page 4 of 4 ...
Page 149: ...149 Model 50 Schematic Diagram Page 1 of 2 ...
Page 150: ...150 Model 50 Schematic Diagram Page 2 of 2 ...
Page 151: ...151 Model 50 Wiring Diagram Page 1 of 5 ...
Page 152: ...152 Model 50 Wiring Diagram Page 2 of 5 ...
Page 153: ...153 Model 50 Wiring Diagram Page 3 of 5 ...