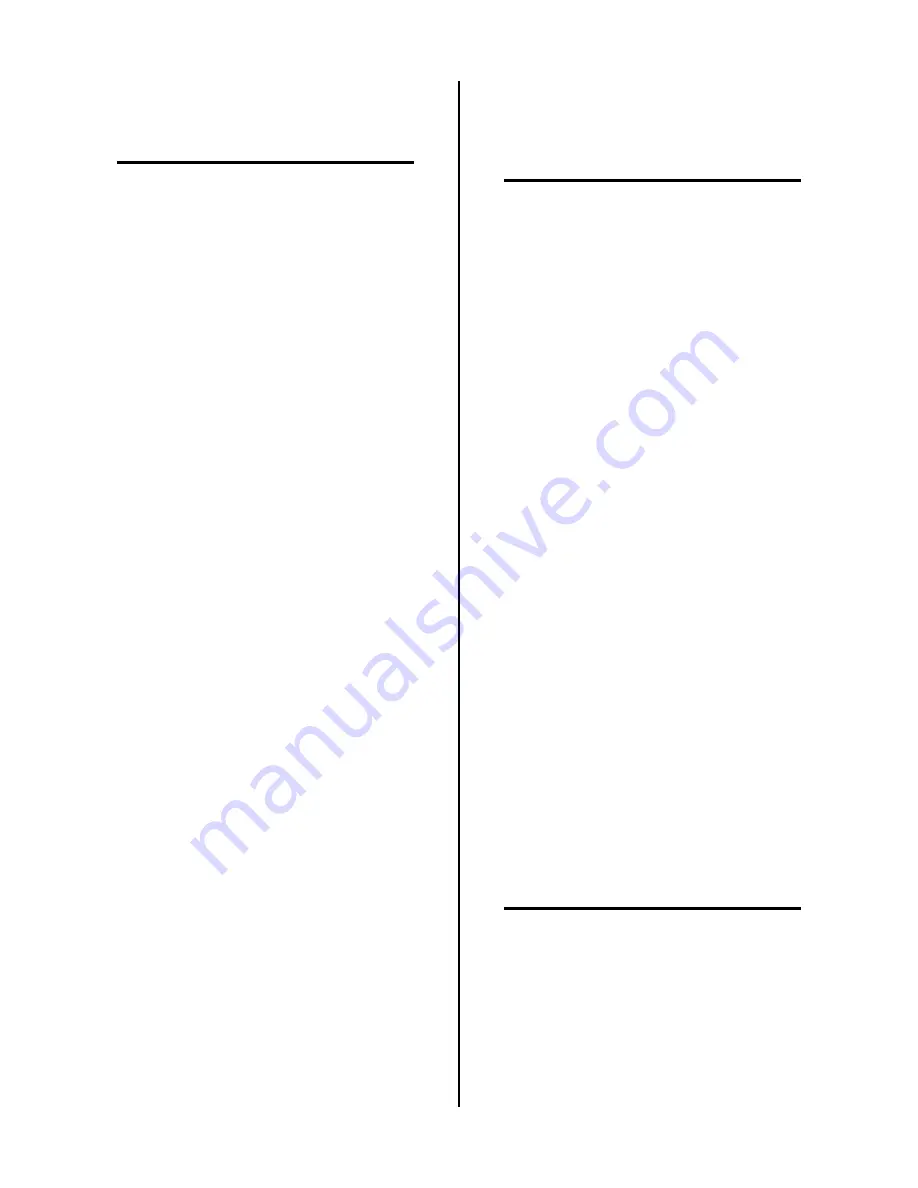
Manual 0-2569
39
SERVICE TROUBLESHOOTING
tor, turns ON the three decimals in the VOLTS dis-
play and prevents the Standoff Control (SC10) from
changing torch height.
NOTE
Refer to Appendix XIII for Corner Slowdown
(CSD) Circuit Diagram.
At the same time, the CSD relay in the Remote Con-
trol (RC6010) closes switching current control from
the OUTPUT AMPS control to the CSD control and
turning on the three decimals in the AMPS display.
Turning ON switch SW1-1, a dip switch on the Re-
mote Control PC Board inside the Remote Control
(RC6010), will reverse the logic so a closure is required
at the CSD input for normal operation and an open
for CSD.
For the Standoff Control (SC11) used without the Re-
mote Control (RC6010), the CNC input for CSD is
through J40-10 and J40-11 or J11-1 and J11-2 of the
Standoff Control (SC11). For the Power Supply, cor-
ner current reduction is only available when using the
Remote Control (RC6010). The CSD relay output at
J42 is not used with the Power Supply.
If the problem is the CSD on all the time or none of
the time disconnect the CSD input from the cutting
machine, set Remote Control (RC6010) internal switch
SW1-1 OFF and jumper the CSD input pins at either
J6 or J29 (J42 or J11 for Standoff Control (SC11). If
CSD is on (display indicates three decimals) when the
jumper is connected and off when the jumper is not
connected, the problem is with the cutting machine
or the CNC cable. If jumping the CSD does not work,
the Remote Control (RC6010) or Standoff Control
(SC11) is faulty. If while using the Remote Control
(RC6010) and Standoff Control (SC10) together, CSD
works in the Remote Control (RC6010) but not the
Standoff Control (SC10) check for a low, less than 3
vdc., on the ribbon cable at J5-21. If not low, with
CSD on, the Remote Control (RC6010) is faulty. If J5-
21 is low, either the Standoff Control (SC10) is faulty
or the ribbon cable is open.
Q. 48 Volt Bias Test
1. Remove the remote cable from the Remote Control
(RC6010), or the Standoff Control (SC11) depending
on remote used. Temporally jumper TB2-1 to TB2-2
for enable.
For the Remote Control (RC 6010), measure for +48
+/-5 vdc from J37-16, 35 and 37 (+) to J37-15,34 and
36 (-). If correct, Remote Control RC6010 (see NOTE)
is faulty.
NOTE
If Standoff Control (SC10) is also used with the
Remote Control (RC6010) all signals and power
come from the Remote Control.
For the Standoff Control (SC11), measure J41-3 and 4
(+) to J41-1 and 2 (-). If correct, Standoff Control (SC11)
is faulty.
2. If the 48 vdc is not correct, go the Power Supply and
measure for +48 +/- 5 vdc at J32-1 to 2 of the Bias PC
Board. If correct, check for open in the Power Supply
harness to J15 or the remote cable.
If 48 vdc is not correct, remove J32 from the Bias PC
Board as and measure again (on the Bias PC Board).
If correct, check for a short in the wiring harness of
remote cable.
3. If 48 vdc is still incorrect check for 115 VAC at J30-1 to
J30-3 at the Bias PC Board. If correct, replace Bias PC
Board. Also, check Fuse (F1), 3A 250v, on the Bias PC
Board.
R. OK-To-Move Tests
1. The Shunt Amp sends a voltage level to the Switching
Control PC Board that corresponds to the work lead
or cutting current. When that current is greater than
14 amps, a circuit on the Switching Control PC Board
sends an active low signal called CSR to the Logic PC
Board, J3-11, that turns on K1, the OK-To-Move relay.
SW5 on the Logic PC Board selects whether the OK-
To-Move output at J2-14 and 16 is a contact closure
(SW5 up) or 24 vac (SW5 down). OK-To-Move from
J2-14 and 16 connects to TB2-9 and 10 then on to J15-
10 and 11.
To troubleshoot, while cutting, measure at TB2-9 to
TB2-10 for 0 volts both AC and DC indicating contact
closure or if Logic PC Board switch SW5 is set for AC
volts measure for 24 VAC.
NOTE
Refer to Appendix XIV for OK-To-Move Circuit
Diagram.
If correct go to step 2. If not correct, repeat the mea-
surement at J2-14 to J2-16. If still incorrect measure
Logic PC Board J3-11 to TP1. If less than 5 vdc re-
place the Logic PC Board, otherwise the Switching
Control PC Board is faulty (or the ribbon cable open).
Summary of Contents for MERLIN 6000
Page 6: ...TABLE OF CONTENTS continued...
Page 16: ...INTRODUCTION 10 Manual 0 2569...
Page 66: ...REPLACEMENT PROCEDURES 60 Manual 0 2569...
Page 82: ...PARTS LISTS 76 Manual 0 2569...
Page 96: ...APPENDIX 90 Manual 0 2569 APPENDIX XIII CORNER SLOWDOWN CSD CIRCUIT DIAGRAM A 01140...
Page 103: ...Manual 0 2569 97 APPENDIX APPENDIX XX ARC STARTER BOX OPTION SYSTEM SCHEMATIC A 01575...
Page 106: ...APPENDIX 100 Manual 0 2569 APPENDIX XXII GAS CONTROL GC3000 WIRING DIAGRAM A 01129...
Page 107: ...Manual 0 2569 101 APPENDIX...
Page 108: ...APPENDIX 102 Manual 0 2569 APPENDIX XXIII SYSTEM SCHEMATIC Rev B or Earlier A 01573...
Page 110: ...APPENDIX 104 Manual 0 2569 APPENDIX XXIV SYSTEM SCHEMATIC Rev C or Later A 01947...
Page 112: ...APPENDIX 106 Manual 0 2569...