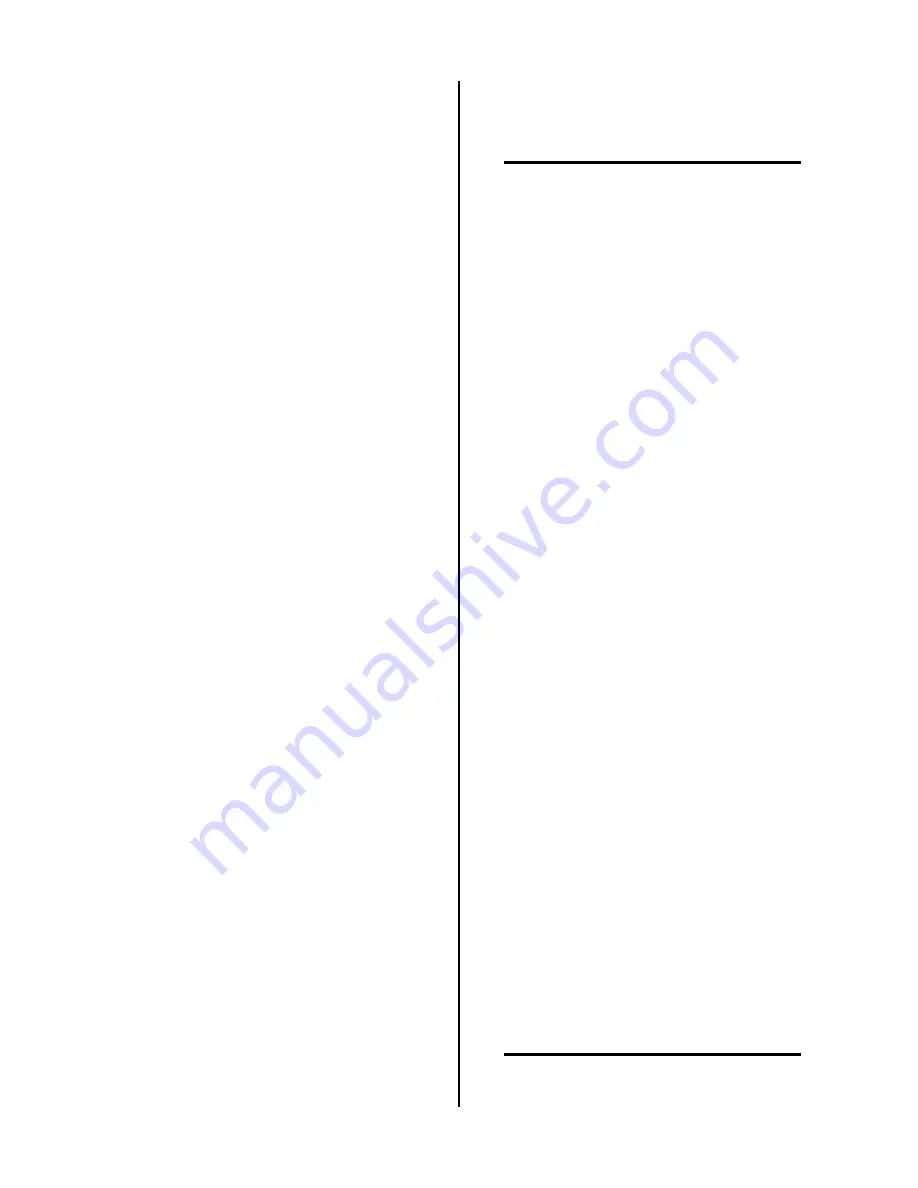
Manual 0-2569
17
SERVICE TROUBLESHOOTING
Board (PCB) configures the power supply for Merlin 6000
operation (refer to Switching Control PCB description for
details).
B. Input Voltage Selection
The main transformer (T1) has busbar connections to se-
lect one of three input voltage ranges. Each main trans-
former secondary has two taps. One secondary tap is
automatically selected by the Voltage Selection PC board
when primary power is applied. If input voltage is within
the lower half of the selected voltage range (for example,
380V or 415V in the 380/415/460V range), the higher
voltage taps are selected. If input voltage is within the
upper half of the selected voltage range (460V in the 380/
415/460V range), the lower voltage taps are selected. This
arrangement provides secondary voltages close to the
optimum levels. When the lower voltage taps are selected
a red indicator, D18, on the Voltage Selection PC Board
will be ON.
The auxiliary voltage taps, 115 VAC and 28 VAC circuits,
are selected directly by relays on the Voltage Selection
PC Board. The fan and pump motors are supplied by the
Motor Control Contactors (MC1 and MC2). MC1 is for
the high voltage tap and MC2 is for the low voltage tap.
Three-phase primary power is controlled by one of the
Main Contactors (W1 for the high voltage tap or W2 for
the low voltage tap).
C. Switch-Mode Power Supply Operation
Primary three-phase power from the Main Transformer
secondary is rectified by the three-phase bridge diodes
D1-D6. The resulting negative DC voltage (approximately
-320 vdc) is applied to the switching transistor (Q1). The
switching transistor controls the output current by pulse
width modulation (PWM). PWM varies the duty cycle
(or on-time versus off-time) of the switch. The greater
the on-time, the higher the output current will be. Com-
ponents D7-10, R2-3, C13-14, L1, and the Suppression PC
Board are snubbers to limit voltage and current surges
caused by switching Q1 on and off. D11-14 are free wheel-
ing diodes. When Q1 is on, current flows through Q1
into the output network. When Q1 is off, D11-14 provide
a path for current to continue flowing supported by en-
ergy that was stored in the output network during the
time Q1 was on. The switching transistor output is a se-
ries of pulses which are filtered back into pure DC volt-
age by the output network. The output network consists
primarily of the main inductor (L2A and L2B), resistor
R13, and capacitor C23.
D. Switching Control PC Board (PCB)
The Switching Control PC Board compares the shunt amp
output with the current control pot setting and generates
logic level PWM signals. The shunt and Shunt Amp PC
Board are located between the input bridge positive and
work lead to measure the output cutting current. The
PWM signals are sent to the Driver PC Board, where they
are converted into the current and voltage levels needed
to drive the switching transistor.
NOTE
The Switching Control PCB in the Merlin 6000
Master Power Supply may be used in the Merlin
6000 Slave Power Supply and the Merlin 6000GST
Master Power Supply.
In the Master Power Supply, the Switching Control PCB
does the following:
• Senses if the Remote Control (RC6010) is installed,
then routes the current control signal from the re-
mote instead of the Merlin Master Power Supply
front panel control.
• Sends the Current Control Signal to the Slave Power
Supply through the Isolation PCB and Parallel
Cable connection. All signals to and from the Slave
Power Supply pass through the Isolation PCB and
Parallel Cable.
• Combines the Output Signal from the Slave Power
Supply with the Shunt Amp signal. The result cre-
ates a Display Signal that is sent to the Remote
Control current display.
• Configures the Remote Control for 300A, instead
of 150A, when a Slave Power Supply is used.
• Sends a torch voltage signal to the Standoff Con-
trol, if used.
• Supplies POT HI and POT LOW signals for setting
MIN and MAX output to both the Remote Con-
trol and Master Power Supply front panel current
controls.
• Sends current sensing (CSR) signal, when output is
greater than 12A, to Logic PCB.
• Sends over current shutdown signal, when current
is greater than 175A, to Logic PCB.
• Turning OFF the ENABLE, from the Remote Con-
trol switch or a switch connected to TB2, will shut
off coolant flow and DC power to allow changing
torch parts. A relay on the Switching Control PCB
removes power from one side of the motor con-
tactor (MC) and main contactor (W) coils when
the ENABLE switch is OFF.
A DIP-switch (SW1) configures the Switching Control
PCB for no current ramping (Merlin 6000) or current
ramping (Merlin 6000GST).
NOTE
For a Merlin 6000 System, both Master and Slave
Power Supplies should have both sections of SW1
turned OFF.
Summary of Contents for MERLIN 6000
Page 6: ...TABLE OF CONTENTS continued...
Page 16: ...INTRODUCTION 10 Manual 0 2569...
Page 66: ...REPLACEMENT PROCEDURES 60 Manual 0 2569...
Page 82: ...PARTS LISTS 76 Manual 0 2569...
Page 96: ...APPENDIX 90 Manual 0 2569 APPENDIX XIII CORNER SLOWDOWN CSD CIRCUIT DIAGRAM A 01140...
Page 103: ...Manual 0 2569 97 APPENDIX APPENDIX XX ARC STARTER BOX OPTION SYSTEM SCHEMATIC A 01575...
Page 106: ...APPENDIX 100 Manual 0 2569 APPENDIX XXII GAS CONTROL GC3000 WIRING DIAGRAM A 01129...
Page 107: ...Manual 0 2569 101 APPENDIX...
Page 108: ...APPENDIX 102 Manual 0 2569 APPENDIX XXIII SYSTEM SCHEMATIC Rev B or Earlier A 01573...
Page 110: ...APPENDIX 104 Manual 0 2569 APPENDIX XXIV SYSTEM SCHEMATIC Rev C or Later A 01947...
Page 112: ...APPENDIX 106 Manual 0 2569...