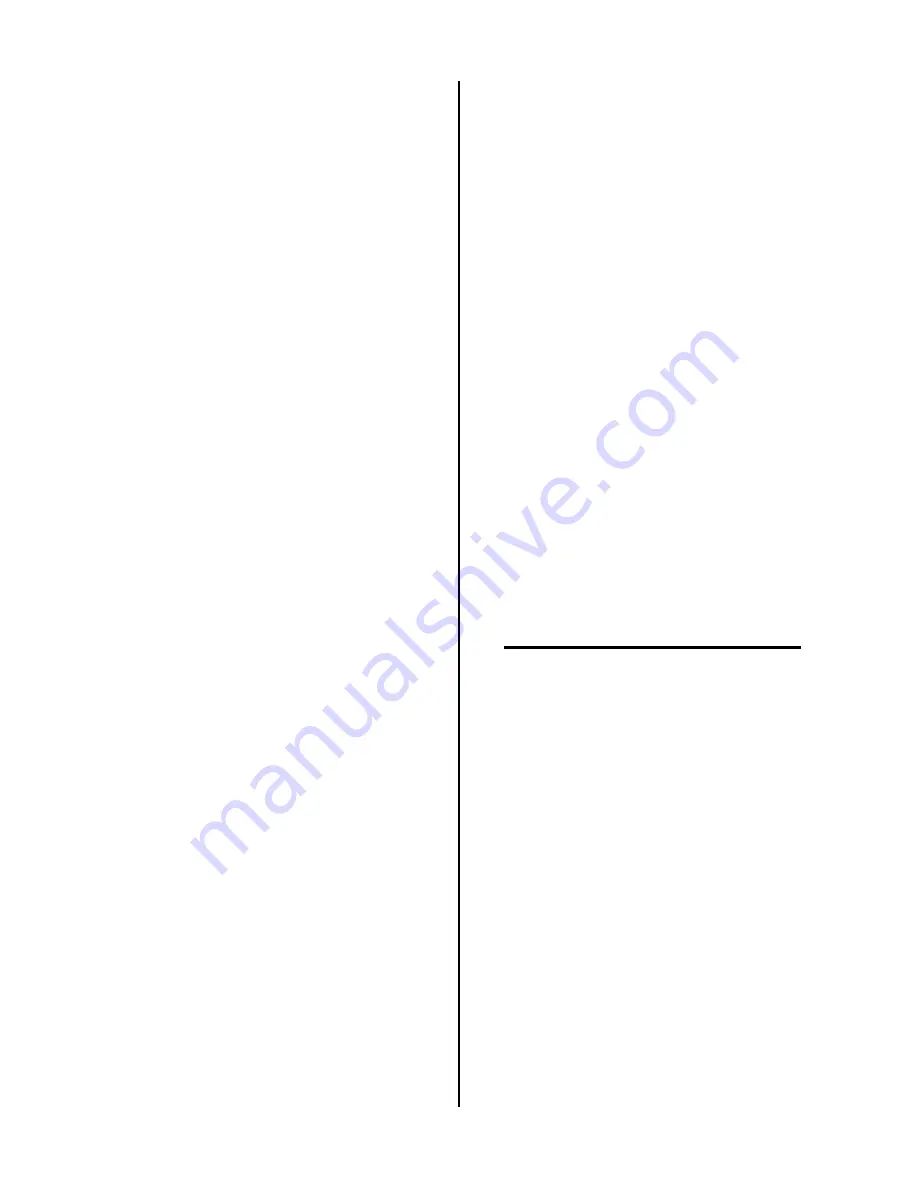
Manual 0-2569
23
SERVICE TROUBLESHOOTING
O. No Pilot Arc; Pilot indicator ON; PCR Energized
1. Faulty Arc Start Box or Shorted torch
a. Refer to Section 4.05-O, Pilot Circuit Check
P. Weak or Sputtering Pilot
1. Worn out or wrong torch consumable parts
a. Check for worn out torch consumables
b. Verify correct torch consumables are being used
for the application
2. Plasma gas pressure too high
a. Refer to Torch Manual Cuting Speed Charts for
proper pressure settings
3. Incorrect pilot resistor setting
a. Must be adjusted according to the input line
voltage, Refer to Section 4.05-S, Pilot Resistor
Adjustment. If adjusting pilot resistors does not
result in good pilot, then check Open Circuit
Votage (OCV) per step #4.
4. Low Open Circuit Voltage (OCV)
a. Improper connection of transformer voltage
select buss bars, check for correct configuration
b. Faulty Voltage Selection PCB
The Merlin has three input voltage ranges; 200-
230, 380-460, 500-575. If the incoming voltage
is in the lower half of any range an LED, D18,
on the Voltage Selection PCB should be OFF, if
it’s ON, refer to 4.05-A, Voltage Selection PCB
Check.
c. Faulty Driver PCB
Pilot and cutting arc has a hum or raspy sound,
pilot may sputter or cutting speeds may be less
than expected.
Q. No pilot; PILOT indicator on; Strong spark
visible at spark gap points inside the Arc Starter
Box
1. Electrode shorted against tip
a. Thread electrode securely into torch head or
replace tip and electrode
2. Shorted torch head
a. Refer to Section 4.05-O, Pilot Circuit Check, and
replace if necessary
3. Broken conductor in torch lead
a. Check and replace if necessary
4. Shorted torch lead
a. Check and replace if necessary
5. Dirty or wet torch lead
a. Clean and dry torch lead
R. Pilot arc on; No main arc transfer (torch brought
within range of work)
1. Work cable not connected
a. Connect work cable securely
2. Defective current control pot (on front panel or remote)
a. If Remote Control is used, disconnect J15 and
set current at power supply front panel. If trans-
fer is correct or Remote Control is not used, re-
fer to Section 4.05-P, Current Control, Display,
and CSD Checks.
S. Main arc starts but goes out immediately; Main
contactor (W1 or W2) goes off
1. Fault condition causes output greater than 175 amps
a. Current Control signal (DEMAND) greater than
10 vdc.
Measure for 10 vdc on the Switching Control
PC Board from TP1 (ground) to Front Panel
CURRENT Control, J10-15, or to the Remote
Current Control, J7-18 (see NOTE).
NOTE
Measure the voltage while attempting to cut as the
voltage may be correct prior to cutting.
If voltage exceeds 10 vdc, may be momentarily,
perform checks at Section 4.05-P, Steps 2 and
3.
b. Shorted Q1 or faulty Switching Control PC
Board. Refer to Section 4.05-M, Switching Con-
trol Check (Q1).
T. Main arc transfers but does not pierce through the
plate or pierce is too slow
1. Incorrect size or worn torch tip
a. Use correct size tip or replace worn tip
2. Restricted Plasma Gas flow
a. Check for wrong gas distributor, correct condi-
tion
b. Check Gas Solenoid Circuits per Section 4.05-H
3. Corner Slowdown (CSD) on remote
a. Most cutting machines activate CSD during
piercing, if so, CSD must be set at or near maxi-
mum to have enough current to pierce.
Summary of Contents for MERLIN 6000
Page 6: ...TABLE OF CONTENTS continued...
Page 16: ...INTRODUCTION 10 Manual 0 2569...
Page 66: ...REPLACEMENT PROCEDURES 60 Manual 0 2569...
Page 82: ...PARTS LISTS 76 Manual 0 2569...
Page 96: ...APPENDIX 90 Manual 0 2569 APPENDIX XIII CORNER SLOWDOWN CSD CIRCUIT DIAGRAM A 01140...
Page 103: ...Manual 0 2569 97 APPENDIX APPENDIX XX ARC STARTER BOX OPTION SYSTEM SCHEMATIC A 01575...
Page 106: ...APPENDIX 100 Manual 0 2569 APPENDIX XXII GAS CONTROL GC3000 WIRING DIAGRAM A 01129...
Page 107: ...Manual 0 2569 101 APPENDIX...
Page 108: ...APPENDIX 102 Manual 0 2569 APPENDIX XXIII SYSTEM SCHEMATIC Rev B or Earlier A 01573...
Page 110: ...APPENDIX 104 Manual 0 2569 APPENDIX XXIV SYSTEM SCHEMATIC Rev C or Later A 01947...
Page 112: ...APPENDIX 106 Manual 0 2569...