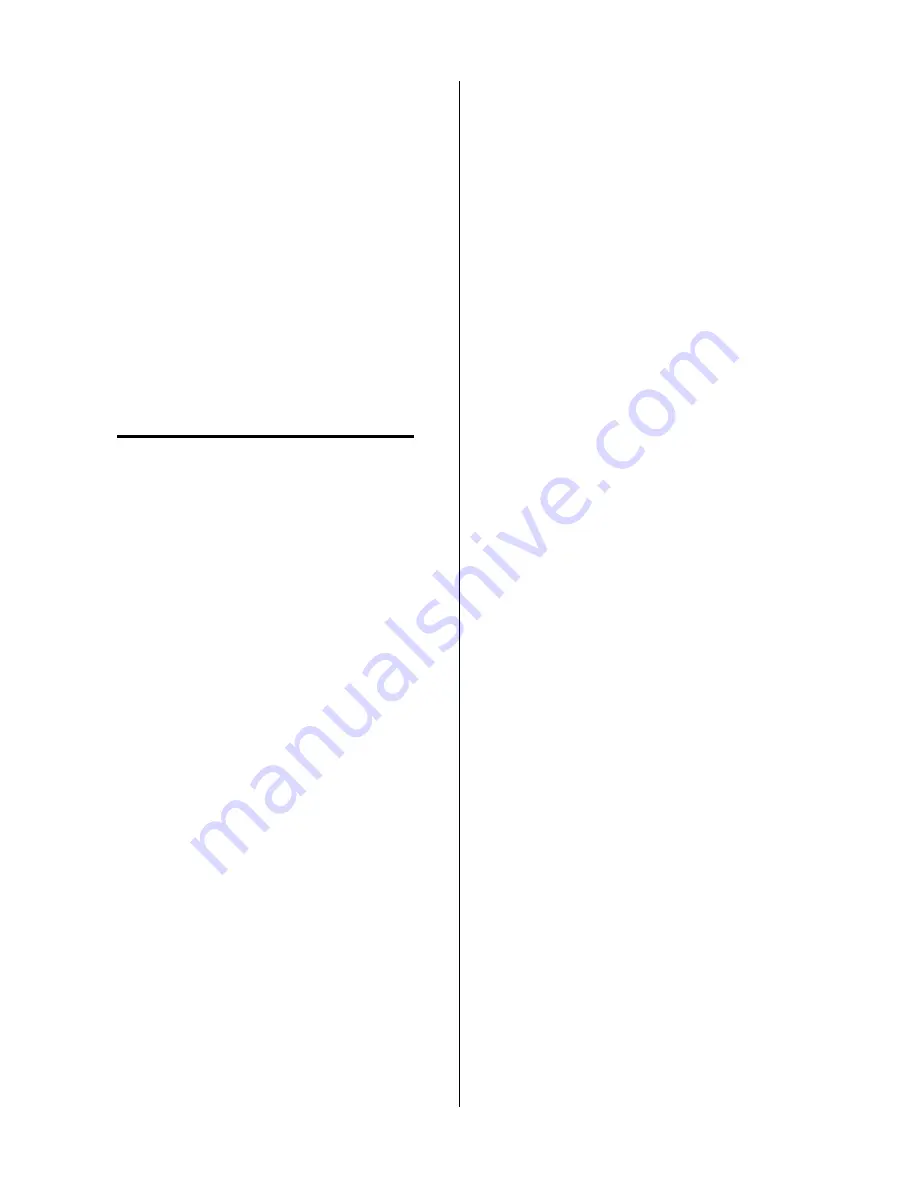
SERVICE TROUBLESHOOTING
22
Manual 0-2569
Turn ON the power supply, if gas flows, the torch
head or leads are clogged.
6. Defective gas solenoids or control circuits
a. Refer to Section 4.05-H, Gas solenoid circuits
J. COOLANT indicator off
1. Little or no pressure shown on gauge
a. Check coolant level
b. Check motor rotation and rpm.
c. Check and replace pump if necessary
2. Clogged internal or external coolant filters
a. Check internal and external coolant filters.
Clean or replace if necessary. Flush the old cool-
ant from the system (see note below).
NOTE
With a clogged internal coolant filter or Torch and
leads the Internal Coolant Pressure Gauge will be
normal, but the Pressure LED, indicates flow, will
be OFF.
3. Clogged torch or leads
a. Check torch and leads and replace if necessary.
Flush the old coolant from the system (see note
above).
4. Faulty flow switch (FS1)
a. Refer to Section 4.05-I, Coolant Flow Sensor
Circuit Check. Replace flow switch if neces-
sary
5. Faulty Logic PC Board
a. Refer to Section 4.05-I, Coolant Flow Sensor
Circuit Check. Replace Logic PC Board if nec-
essary.
6. Faulty LED/current control board
a. Refer to Section 4.05-I, Coolant Flow Sensor Cir-
cuit Check. Replace Logic PC Board if neces-
sary.
K. Coolant conductivity indicator off
1. Ionized or contaminated coolant
a. Check coolant conductivity and deionizer car-
tridge. Replace both if necessary
2. Faulty (or contaminated) conductivity probe
a. Clean conductivity probe and replace if neces-
sary
3. Faulty Logic PC Board
a. Refer to Section 4.05-J, Coolant Conductivity
Circuit. Replace Logic PC Board if necessary.
4. Faulty LED/Current Control PC Board
a. Refer to Section 4.05-J, Coolant Conductivity
Circuit. Replace LED/Current Control PC
Board if necessary
L. Press cutting machine START and nothing hap-
pens or standoff finds height then nothing
happens (no gas flow or pilot)
1. Start signal not getting to the Power Supply or Power
Supply is defective.
a. Determine if Remote Control or Power Supply
is at fault. Remove Remote Control or CNC
cable from J15 (or TB2). Jumper TB2-1 & 2 to
enable unit, then jumper TB2-3 & 4 for START.
If the pilot starts, after preflow, Remote Con-
trol or CNC is faulty. Refer to Section 4.05-L,
Remote Control Start Circuit. If no pilot, refer
to Section 4.05-K for Power Supply Start Cir-
cuit.
M. After Pre-Flow, DC indicator OFF; Main Contac-
tor does not come ON or only momentarily ON;
No Pilot Arc
1. Master Power Supply not receiving START signal
a. Refer to Section 4.05.N, Main Contactor (W)
Control Circuit and Section 4.05-K, Power Sup-
ply Start Circuits
2. Slave Power Supply not receiving START signal
a. Master Power Supply starts but Slave does not
Verify that the Slave Power Supply Logic PCB
READY and RUN LEDs are ON
• If the LEDs are ON, refer to section 4.05-T, Iso-
lation and Parallel Cable Interface
• If the LEDs are OFF, refer to Section 4.05.N, Main
Contactor (W) Control Circuit
3. Faulty Q1
a. Refer to Section 4.05-M, Switching Control
Check
N. No pilot arc; DC indicator on; Pilot indicator
OFF; PCR not energized
1. Faulty Logic PC Board, Switching Control PC Board,
or Shunt Amp PC Board.
a. Refer to Section 4.05-O, Pilot Circuit Check.
Summary of Contents for MERLIN 6000
Page 6: ...TABLE OF CONTENTS continued...
Page 16: ...INTRODUCTION 10 Manual 0 2569...
Page 66: ...REPLACEMENT PROCEDURES 60 Manual 0 2569...
Page 82: ...PARTS LISTS 76 Manual 0 2569...
Page 96: ...APPENDIX 90 Manual 0 2569 APPENDIX XIII CORNER SLOWDOWN CSD CIRCUIT DIAGRAM A 01140...
Page 103: ...Manual 0 2569 97 APPENDIX APPENDIX XX ARC STARTER BOX OPTION SYSTEM SCHEMATIC A 01575...
Page 106: ...APPENDIX 100 Manual 0 2569 APPENDIX XXII GAS CONTROL GC3000 WIRING DIAGRAM A 01129...
Page 107: ...Manual 0 2569 101 APPENDIX...
Page 108: ...APPENDIX 102 Manual 0 2569 APPENDIX XXIII SYSTEM SCHEMATIC Rev B or Earlier A 01573...
Page 110: ...APPENDIX 104 Manual 0 2569 APPENDIX XXIV SYSTEM SCHEMATIC Rev C or Later A 01947...
Page 112: ...APPENDIX 106 Manual 0 2569...