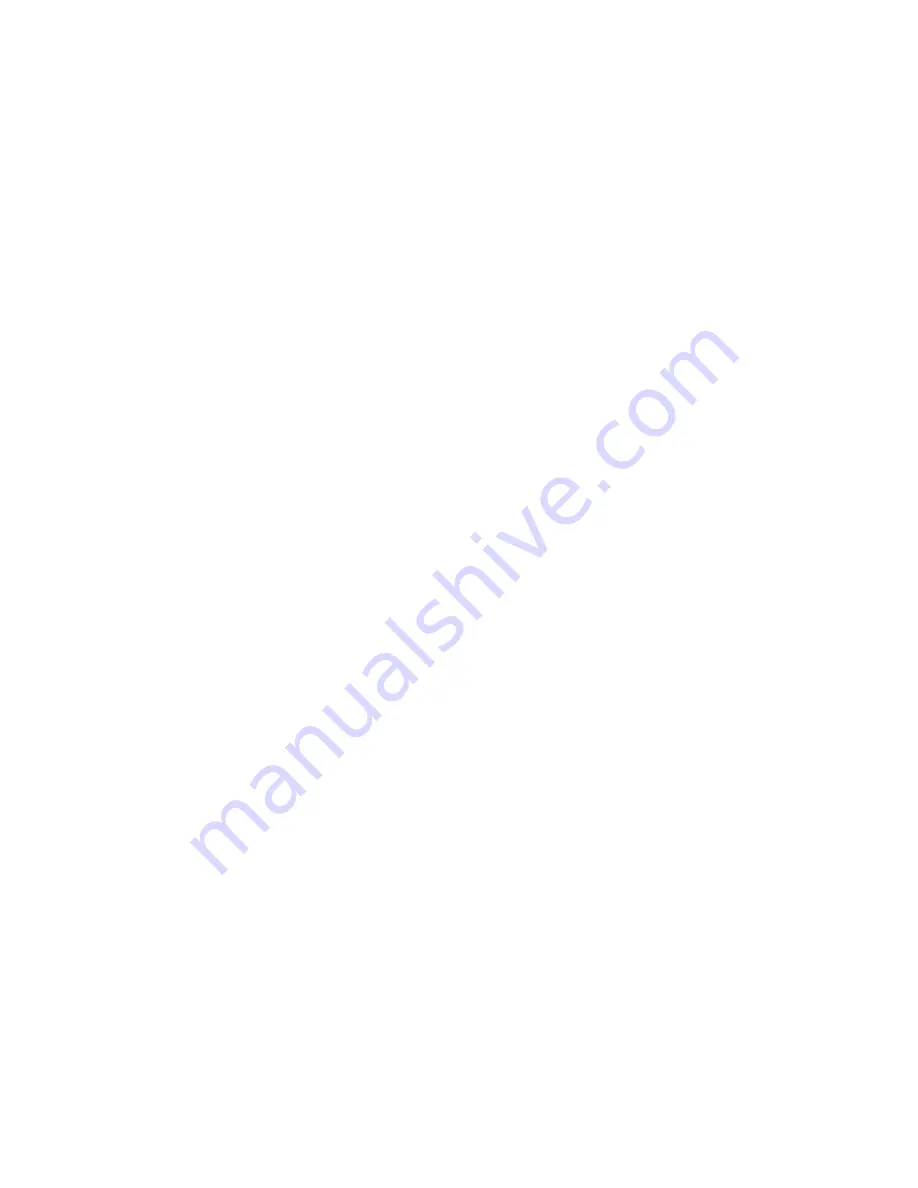
TABLE OF CONTENTS
SECTION 1:
GENERAL INFORMATION ........................................................................... 1-1
1.01
Notes, Cautions and Warnings ........................................................................ 1-1
1.02
Important Safety Precautions ......................................................................... 1-1
1.03 Publications .................................................................................................... 1-2
1.04
Note, Attention et Avertissement ..................................................................... 1-3
1.05
Précautions De Sécurité Importantes ............................................................. 1-3
1.06
Documents De Reference ............................................................................... 1-6
1.07
Statement of Warranty .................................................................................... 1-7
SECTION 2 SYSTEM:
INTRODUCTION ..................................................................................... 2-1
2.01
How To Use This Manual ................................................................................ 2-1
2.02
Equipment Identification ................................................................................. 2-1
2.03
Receipt Of Equipment ..................................................................................... 2-2
2.04
Power Supply Specifications .......................................................................... 2-2
2.05
Input Wiring Specifications ............................................................................. 2-4
2.06
Power Supply Features ................................................................................... 2-5
SECTION 2 TORCH:
INTRODUCTION .................................................................................... 2T-1
2T.01 Scope of Manual ............................................................................................2T-1
2T.02 General Description .......................................................................................2T-1
2T.03 Specifications
...............................................................................................2T-1
2T.04 Quick Connection Torch ................................................................................2T-2
2T.05 Options And Accessories ...............................................................................2T-2
2T.06 Introduction to Plasma ..................................................................................2T-2
SECTION 3 SYSTEM:
INSTALLATION ....................................................................................... 3-1
3.01 Unpacking ....................................................................................................... 3-1
3.02
Lifting Options ................................................................................................ 3-1
3.03
Opening the Main Switch Cover ...................................................................... 3-2
3.04
Primary Input Power Connections, SINGLE Phase ......................................... 3-2
3.05
Primary Input Power Connections, THREE Phase ........................................... 3-3
3.06
Gas Connections ............................................................................................. 3-4
3.07
Work Lead Connections .................................................................................. 3-7
SECTION 3 TORCH:
INSTALLATION ...................................................................................... 3T-1
3T.01 Torch Connections .........................................................................................3T-1
3T.02 Setting Up Mechanical Torch .........................................................................3T-1
SECTION 4 SYSTEM:
OPERATION .......................................................................................... 4-1
4.01
Front Panel Controls / Features ....................................................................... 4-1
4.02
Preparations for Operation .............................................................................. 4-4
Summary of Contents for CUTMASTER 60i
Page 6: ...This Page Intentionally Blank ...
Page 16: ...CUTMASTER 60i GENERAL INFORMATION Manual 0 5436 1 8 This Page Intentionally Blank ...
Page 22: ...CUTMASTER 60i INTRODUCTION Manual 0 5436 2 6 This Page Intentionally Blank ...
Page 26: ...CUTMASTER 60i INTRODUCTION Manual 0 5436 2T 4 This Page Intentionally Blank ...
Page 34: ...CUTMASTER 60i INSTALLATION Manual 0 5436 3 8 This Page Intentionally Blank ...
Page 36: ...CUTMASTER 60i INSTALLATION Manual 0 5436 3T 2 This Page Intentionally Blank ...
Page 44: ...CUTMASTER 60i OPERATION Manual 0 5436 4 8 This Page Intentionally Blank ...
Page 72: ...CUTMASTER 60i SERVICE Manual 0 5436 5 12 This Page Intentionally Blank ...
Page 89: ...This Page Intentionally Blank ...