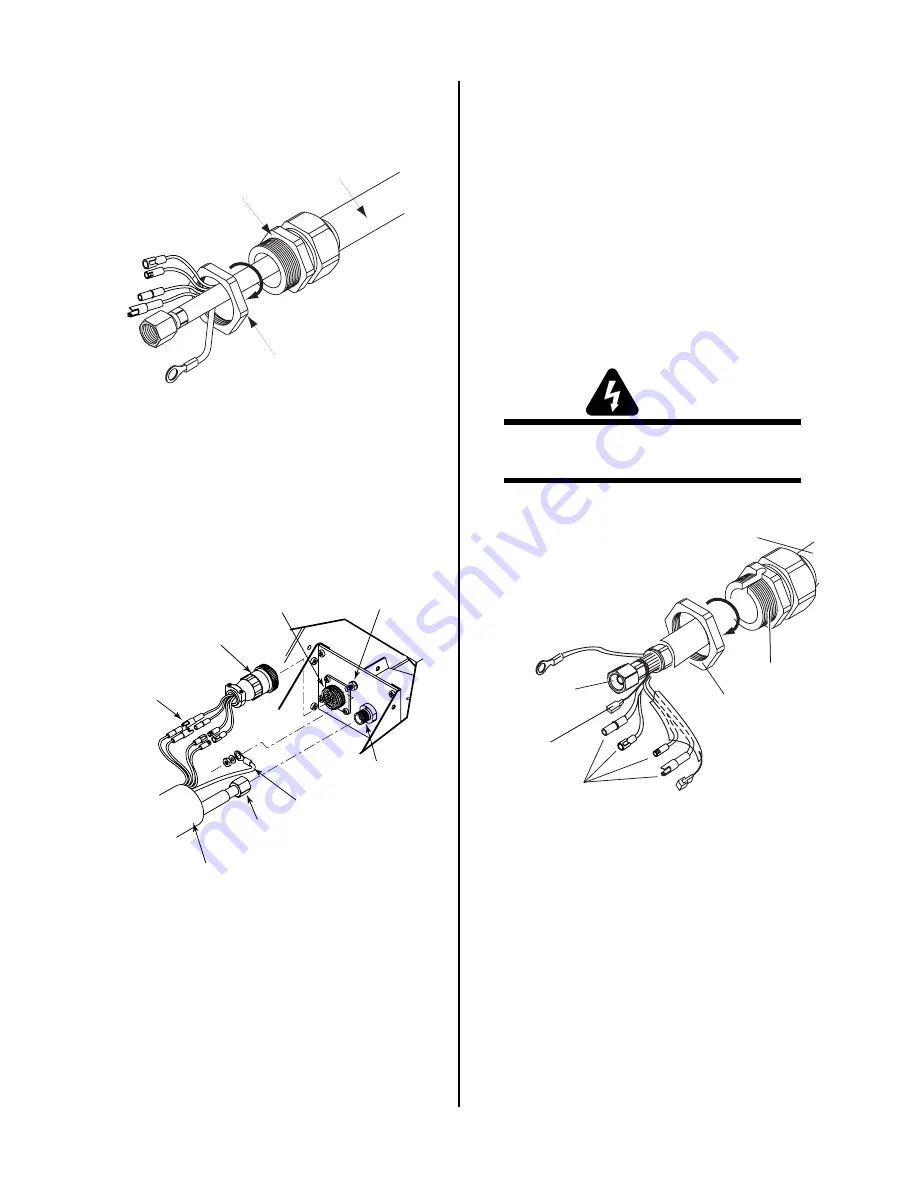
Manual 0-2811
3-7
INSTALLATION
A. PCM-102 Torch Installation
1. Remove the retaining nut from the Strain Relief.
Strain Relief
Nut
Strain Relief
Torch Leads
Assembly
A-02760
Figure 3-10 Torch Strain Relief Nut
2. Feed the end of the torch lead and the Strain Re-
lief into the hole in the unit.
3. Tighten the Strain Relief Nut to secure the Strain
Relief to the Power Supply.
Adapter
(Supplied With
Power Supply)
Pilot Lead
Torch Lead
Assembly
Gas/Power
Lead
Adapter
Connector
Pilot Lead Stud
Gas/Power Lead
Connection
A-02747
PIP Circuit &
Shield Connectors
Figure 3-11 Torch Leads Connections
4. Connect the torch Negative/Plasma Lead to the
bulkhead connection inside the Power Supply.
5. Connect the PIP and Shield Cables to the mating
connectors on the Adapter supplied on the Power
Supply.
6. Remove the top nut and washer from the Pilot
Stud.
7. Place the lug on the Pilot Control Wire onto the
stud and secure with the nut and washer removed
in the above Step.
8. Tighten the Strain Relief onto the Torch Leads.
9. Check the torch for proper parts assembly.
10. Close the access panel and turn the latching screw.
B. SL100 Torch Installation
Torches with shielded leads and ATC connectors connect
to a shielded ATC Adapter which connects to the power
supply bulkhead. Torches with shielded leads and O2B
fittings connect directly to the power supply bulkhead.
Bulkhead connections are the same in both applications.
WARNING
Disconnect primary power at the source before dis-
assembling the torch or torch leads.
Strain Relief
Nut
Strain Relief
Shielded ATC Adapter
Pilot Lead
Negative/Plasma
Lead
Torch Control
Connectors
Shield
Connector
Shield
Connector
A-03677
Strain Relief Nut Removal
1. Remove the Strain Relief Nut from the Strain Re-
lief. Inside the Power Supply Bulkhead area, route
the connectors on the free end of the Adapter or
Torch Leads through the Strain Relief Nut.
2. Fit the ATC Adapter or Torch Leads end and the
Strain Relief into the hole in the unit.
3. Secure the Strain Relief with the retaining nut re-
moved earlier.
Summary of Contents for CE Pak Master 100XL Plus
Page 2: ......
Page 6: ......
Page 18: ...INTRODUCTION 2 4 Manual 0 2811...
Page 36: ...OPERATION 4 6 Manual 0 2811...
Page 49: ...Manual 0 2811 A 5 APPENDIX This page left blank...
Page 50: ...APPENDIX A 6 Manual 0 2811 APPENDIX V SYSTEM SCHEMATIC A 02765...
Page 51: ...Manual 0 2811 A 7 APPENDIX A 02765...
Page 52: ......