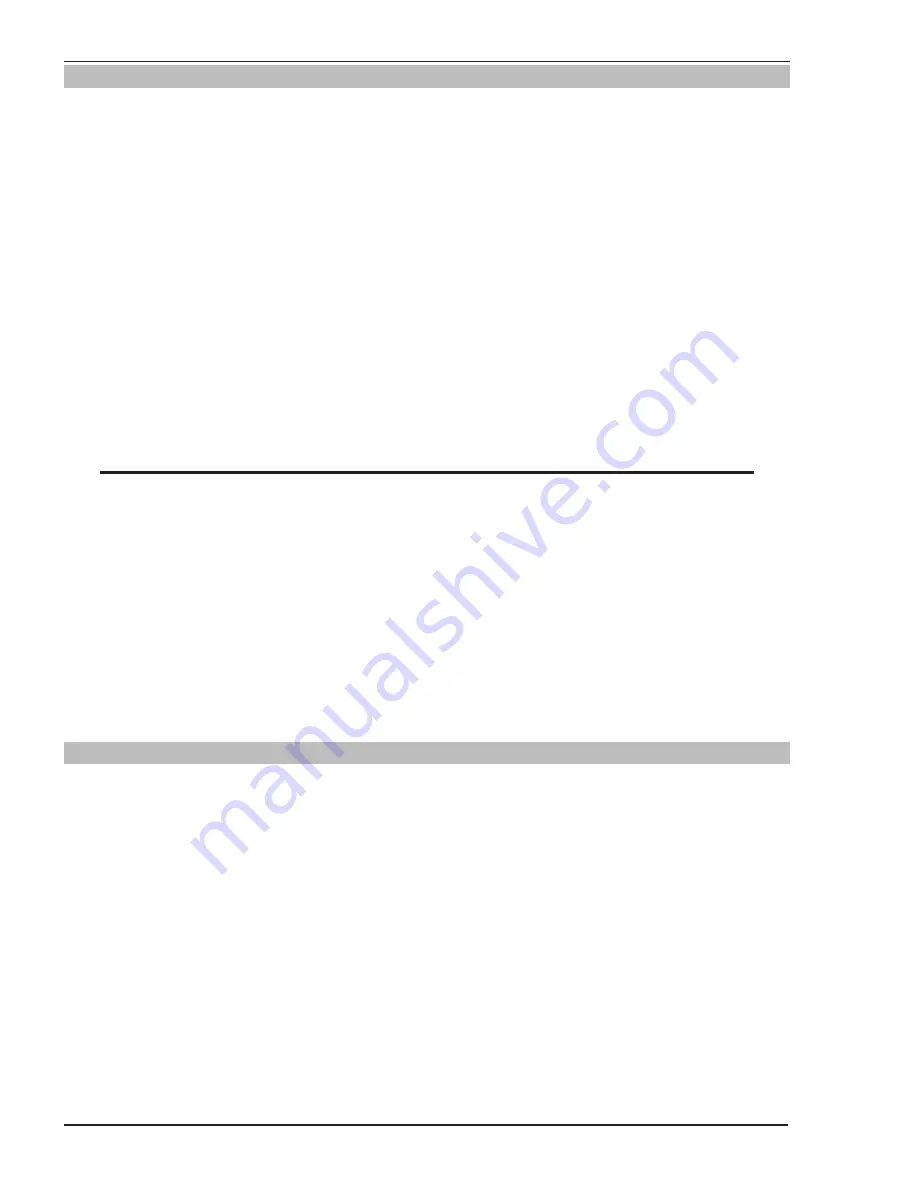
Fabricator 181i
INSTALLATION, OPERATION AND SETUP
3-20
Manual 0-5191
3.18 Gas Regulator Operation
With the regulator connected to cylinder or pipeline, and the adjustment screw/knob fully disengaged, pressurize
as follows:
1. Stand to one side of regulator and slowly open the cylinder valve. If opened quickly, a sudden pressure
surge may damage internal regulator parts.
2. With valves on downstream equipment closed, adjust regulator to approximate working pressure. It is
recommended that testing for leaks at the regulator connection points be carried out using a suitable leak
detection solution or soapy water.
3. Purge air or other unwanted welding grade shielding gas from equipment connected to the regulator by
individually opening then closing the equipment control valves. Complete purging may take up to ten
seconds or more, depending upon the length and size of the hose being purged.
Adjusting Flow Rate
With the regulator ready for operation, adjust working flow rate as follows:
1. Adjust the gas flow rate. The recommended rate for MIG welding is 28-46 CFH. The recommended rate
for LIFT TIG welding is 10-28 CFH.
NOTE
It may be necessary to re-check the shielding gas regulator flow rate following the first weld sequence
due to back pressure present within shielding gas hose assembly.
Shutdown
Close cylinder valve whenever the regulator is not in use. To shut down for extended periods (more than 30 minutes).
1. Close cylinder or upstream valve tightly.
2. Open downstream equipment valves to drain the lines. Bleed gas into a well ventilated area and away from
any ignition source.
3. After gas is drained completely, disengage adjusting screw and close downstream equipment valves.
4. Before transporting cylinders that are not secured on a cart designed for such purposes, remove regulators.
3.19 Setup for MIG (GMAW) Welding with Gas Shielded MIG Wire
A. Select MIG mode with the process selection control. (refer to Section 3.10 for further information)
B. Connect the MIG Gun Polarity Lead to the positive welding terminal (+). If in doubt, consult the electrode
wire manufacturer. Welding current flows from the Power Source via heavy duty bayonet type terminals. It is
essential, however, that the male plug is inserted and turned securely to achieve a sound electrical connection.
C. Fit the MIG Gun to the Power Source. (Refer to section 3.07 Attaching the Tweco WeldSkill 180 MIG Gun).
D. Connect the work lead to the negative welding terminal (-). If in doubt, consult the electrode wire manufacturer.
Welding current flows from the Power Source via heavy duty bayonet type terminals. It is essential, however,
that the male plug is inserted and turned securely to achieve a sound electrical connection.
E. Fit the gas regulator/flow gauge to the shielding gas cylinder (refer to Section 3.14) then connect the shielding
gas hose from the rear of the Power Source to the regulator/flow gauge outlet.
F. Refer to the Weld Guide located on the inside of the wirefeed compartment door for further information.
Summary of Contents for FABRICATOR 181i
Page 6: ......
Page 24: ......
Page 30: ......
Page 58: ...Fabricator 181i INSTALLATION OPERATION AND SETUP 3 28 Manual 0 5191 ...
Page 91: ...Fabricator 181i Manual 0 5191 5 7 Trouble Shooting and Service ...
Page 96: ...Fabricator 181i KEY SPARE PARTS 6 4 Manual 0 5191 This page is left blank intentionally ...