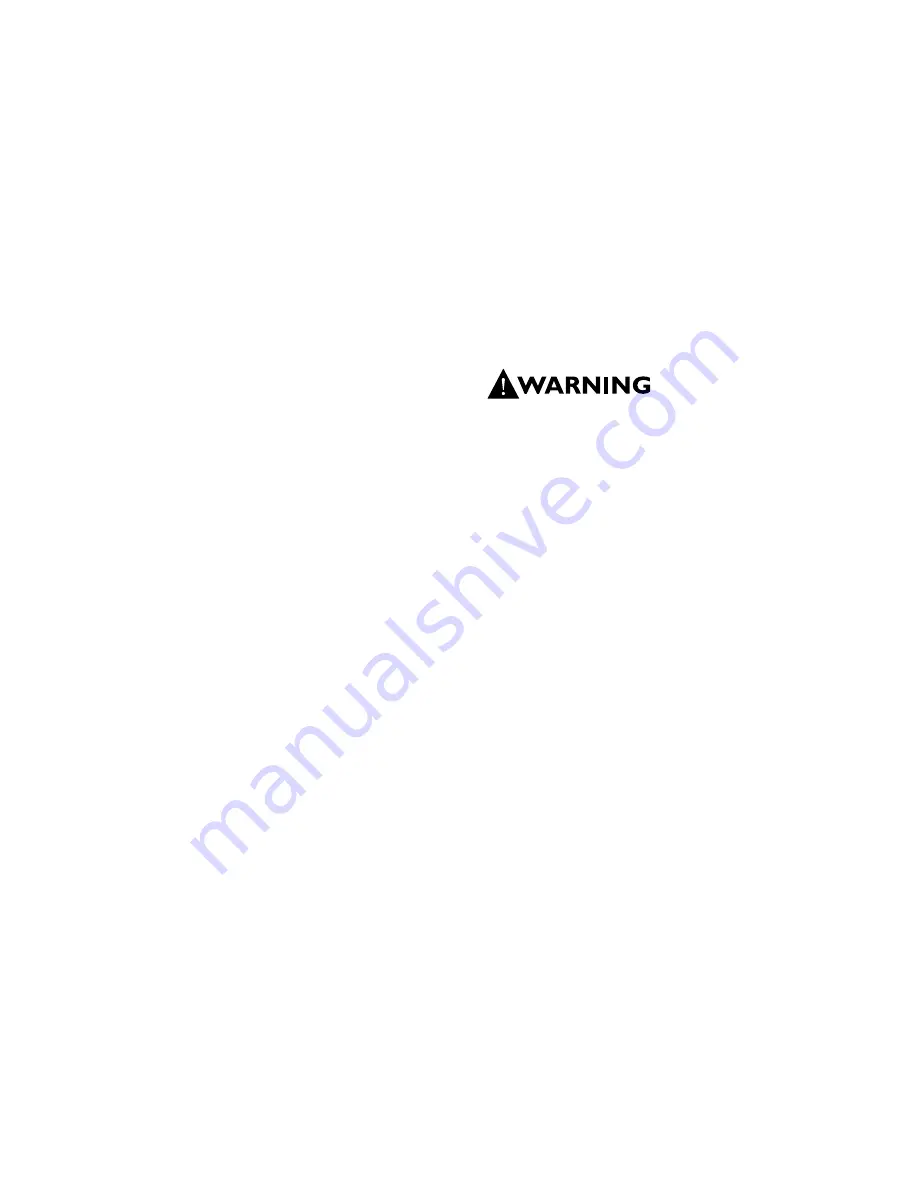
Blower does not run. Compressor runs briefly but cycles
on & off.
1. Loose connection in blower circuit (Fig. 4).
2. Obstruction prevents impeller rotation.
3. Defective blower (Sec. 5.5).
Unit removes some water but not as much as expected.
1. Air temperature and/or humidity have dropped.
2. Humidity meter and/or thermometer used are out of
calibration.
3. Unit has entered defrost cycle (Sec. 3.3 & 5.10).
4. Air filter dirty (Sec. 4.1).
5. Defrost timer incorrectly set for conditions
(Sec. 3.3 & 5.10).
6. Defective defrost thermostat (Sec. 5.10).
7. Low refrigerant charge (Sec. 5.4).
8. Air leak such as loose cover.
9. Defective compressor (Sec. 5.6).
10. Restrictive ducting (Sec. 2.4).
Pump does not pump water.
1. Hose kinked or plugged.
2. Pump check valve plugged (Sec. 5.11).
3. Bad connection in pump circuit (Fig. 4).
4. Hose disconnected internally.
Evaporator coil frosted continuously, low dehumidifying
capacity.
1. Defrost thermostat loose or defective
(Sec. 3.3 & 5.10).
2. Low refrigerant charge (Sec. 5.4).
3. Dirty air filters or airflow restricted. (Sec. 4.1).
4. Defrost timer set incorrectly (Sec. 3.3).
5.4 Refrigerant Charging
If the refrigerant charge is lost due to service or a leak,
a new charge must be accurately weighed in. If any of
the old charge is left in the system, it must be removed
before weighing in the new charge. Refer to the unit
nameplate for the correct charge weight and refrigerant
type. Add the refrigerant through the low side service
port (See Fig. 5).
5.5 Blower Replacement
The centrifugal blower has a PSC motor and internal
thermal overload protection. If defective, the complete
assembly must be replaced.
1. Unplug the power cord.
2. If an outlet duct is connected to the unit, remove it.
3. Remove the cabinet side.
4. Remove the 4 screws holding the electrical box
located next to the blower.
5. Disconnect the blower leads. Black from the blower
switch, and white the run capacitor.
6. Unbolt the blower capacitor from the blower motor
(required for removal clearance).
7. Remove the nuts & bolts holding the blower outlet
flange to the cabinet end and remove the blower.
8. Reassembling with the new blower is the above
procedure reversed.
5.6 Compressor/Capacitor Replacement
This compressor is equipped with a two terminal external
overload, run capacitor, but no start capacitor or relay
(see Fig. 4).
CAUTION-ELECTRICAL SHOCK HAZARD: Electrical power
must be present to perform some tests; these tests
should be performed by a qualified service person.
5.6A Checking Compressor Motor Circuits
Perform the following tests if the blower runs but the
compressor does not with the humidity control ON.
1. Turn the humidity control OFF and unplug the unit,
remove the cabinet front (6 screws).
2. Plug in the unit and turn the humidity control ON. Use
a voltmeter to check for 110 to 120 volts between
(a) the relay terminal that the black wire from the
compressor connects to and (b) the capacitor
terminal with the (2) white wires, (1) red wire & (1)
brown wire connected. If voltage is present, go to
step 3. If no voltage, the defrost thermostat, the
relay or the condensate pump safety switch are open
or there is a loose connection in the compressor
circuit. Test each component for continuity; see the
appropriate section if a defect is suspected.
3. Turn the humidity control OFF and unplug the unit,
then disconnect the red and yellow wires from
compressor terminals R & S. Using an ohmmeter
check continuity between the points listed below.
4. Compressor terminals C and S: No continuity
indicates an open start winding; the compressor
must be replaced.
5. Compressor terminals C and R: No continuity
indicates an open run winding; the compressor must
be replaced.
6. Compressor terminal C and overload terminal 1: No
continuity indicates a defective overload lead.
7. Overload terminals 1 and 3: If there is no continuity,
the overload may be tripped; wait 10 minutes and try
again. If there is still no continuity, it is defective and
must be replaced.
5
www.thermastor.com • [email protected]
Toll-Free 1-800-533-7533
www.sylvane.com 1-800-934-9194