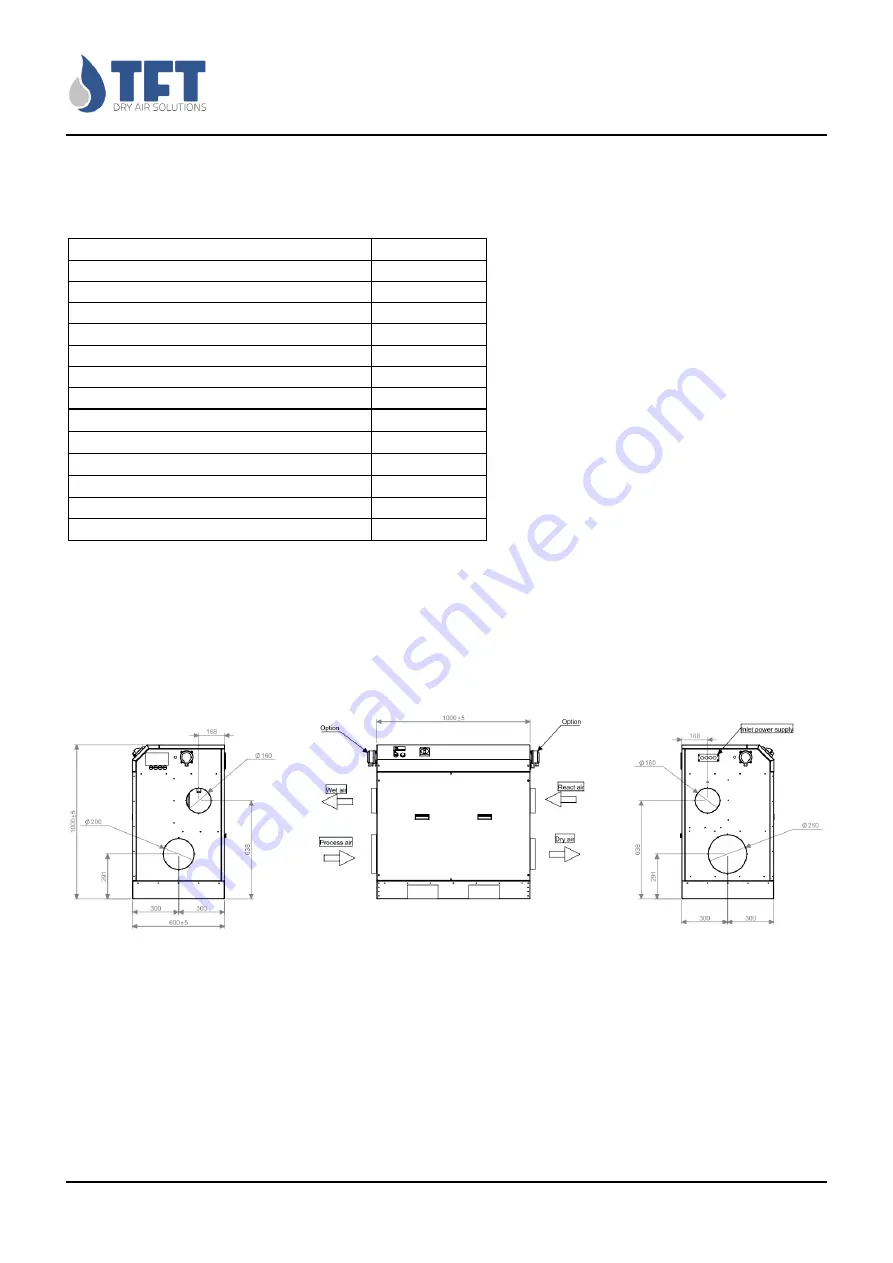
Pagina 20 di 35
AD1100TE-STD.EN-00 - Subject to change without notice
TFT DryAir
Technical data
Characteristics AD1100TE
Process air flow
1100 m
3
/h
Static pressure
300 Pascal
Reactivation air flow
250 m
3
/h
Static pressure
180 Pascal
Dehumidification capacity:
@ 20°C ÷ 60% RH
5,0 Kg/h
Maximum input power
7,1 kW
Power supply Volt/Ph/Hz
400/3/50
Auxiliary power
24 V
Connection Outlet Process Air
= 200 mm
Connection Inlet Process Air
= 250 mm
Connection Outlet Wet Air
= 160 mm
Connection Inlet Reactivation Air
= 160 mm
Weight
150 kg
Total sound pressure (*):
66 dB (A)
(*)
Sound pressure level calculated in free field, 10 meters from the unit, directional factor Q = 2 according to ISO 9614
Note:
For performance to different conditions - contact TFT srl for selection
Dimensions
PA = Inlet process air - DA = Outlet dry air - WA = Outlet wet air - RA = Inlet reactivation air