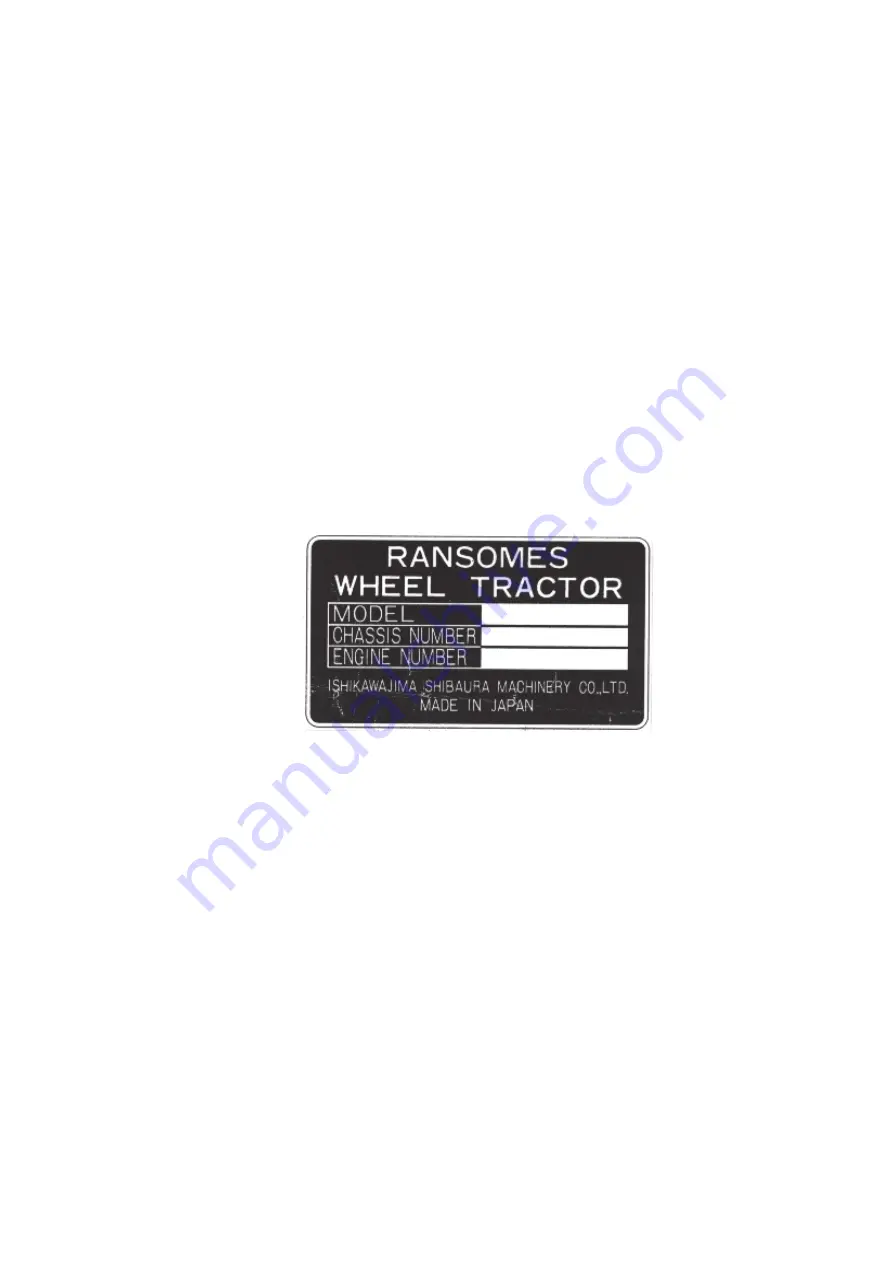
1
PLEASE READ CAREFULLY:
For a complete list of the pre-delivery service checks performed by your dealer, refer to PRE-DELIVERY SERVICE on the upper portion of page
61 and 63. The copy on page 61 is your record of the service performed, and the copy on page 63, which is to be removed from the manual, is
your dealer’s. MAKE SURE THAT YOU AND THE DEALER SIGN BOTH COPIES.
After you have operated your tractor for fifty hours, take this manual and your tractor to your dealer. He will then perform the factory recommended
50-HOUR SERVICE as listed on the lower portions of pages 61 and 63 - without charge - except for lubricant, oil, or filters replaced as part of
normal maintenance. MAKE SURE THAT YOU AND THE DEALER SIGN BOTH COPIES.
A PRODUCT IDENTIFICATION PLATE is located on the left-hand side of the transmission housing. The numbers on the plate are important
should your tractor require future service. For your convenience, have your dealer record the numbers in the appropriate spaces below.
RANSOMES policy is one of continuous improvement, and the right to change prices, specification or equipment at any time without notice is
reserved.
All data given in this book is subject to production variations. Dimensions and weights are approximate only and the illustrations do not necessarily
show tractors in standard condition. For exact information about any particular tractor please consult your RANSOMES Tractor Dealer.
Summary of Contents for Ransomes CT435
Page 2: ......
Page 31: ...29 OPERATION Figure 39 Rear Wheel Weights Figure 40 Front End Weights ...
Page 57: ...55 METRIC BOLT TORQUE SPECIFICATIONS LUBRICATION AND MAINTENANCE ...
Page 62: ...60 SPECIFICATIONS ...
Page 70: ...68 NOTES ...
Page 72: ...70 ...
Page 74: ......
Page 75: ......
Page 76: ...Ransomes Way Ipswich England IP3 9QG RANSOMES ...