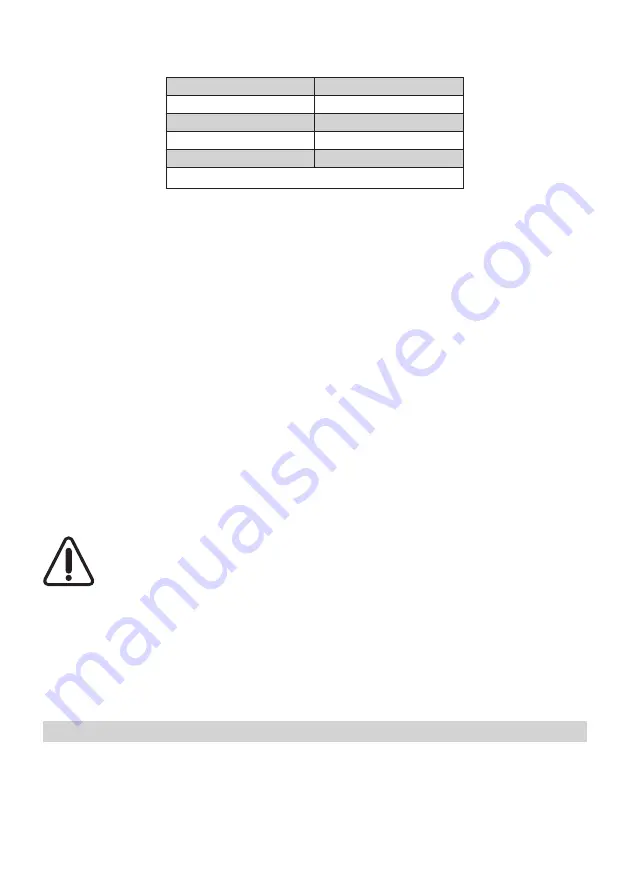
32
The example boiler settings:
Temperature
60 °C
Feeding time
20 s
The time of breake
40 s
Fun power
Power on 5
Interval overburning
15 - 20 min.
Sample sets refers to coal
After getting steady glow switch over the controller to automatic functioning, at this point the fan and fuel proportioner
are in operation. Set the required temperature.
According to the controller manual, set the required parameters
on the controller.
It
is advisable
that the feeding and scavenge time lasts up to 60 s. In the case of extending the feeding time the
scavenge time should be lessened by the same amount of time (and vice versa).The above settings are the example
settings. The producer does not guarantee that the example setting ensures proper functioning of the boiler in any
circumstances. The settings of the boiler functioning have to be adjusted to the user’s own needs. During automatic
operation of the boiler the fuel will burn completely when it reaches the edge of the burner’s cupola and ash as well as
slag fall down into the ash box. Then, the furnace is self cleaning and only the ash needs to be removed from the boiler
once a day or max. once in four days, depending on the size of the boiler and whether it is overloaded .
Properly set parameters guarantee reaching the required temperatures and total combustion so that the ash, falling
into the ash box accounts for about 5-7% of the burnt fuel. It is necessary to observe how in the given conditions the
boiler is operating and burning the fuel. If the fuel does not burn completely, but falls down into the ash box as partly
unburnt /pellets/, this means that the feeding time is to long and the scavenge time is too short (the fuel does not have
enough time to burn). The parameters need to be selected in such a way that the fuel burns on the ’dish’ of the retort in a
light cone.The burning must not take place in ‘subsidence’ of the retort. As this may cause the rise in the temperature of
the feeder’s pipe and the activation of the alarm on the controller. It is essential to remember that when the parameters
are accurately set and we want to increase the temperature, we should increase the feeding time and decrease the
standstill time. The setting of the controller for the system given depends on many factors, such as: the size of a heating
surface the amount of water in the system, fuel and the insulation of the building etc.
The suggested min. temperature for operating the boiler is 56°C.
Longer combustion at low temperatures results in condensation of the exhaust and corrosion of the central heating
boiler which diminishes its life. Low temperatures also cause intensive precipitation of tar substances from the fuel. This
causes a layer of tar in the chimney to develop and in the boiler water exchanger.
At the beginning of the combustion, over the period of a few days, there might be a water leakage from the boiler.
This is caused by the expansion of the inside sheet metal plates of the body of the central heating boiler. It is a natural
symptom in the first days of the central heating boiler operation .The temperature in the boiler should be increased until
the retting stops.
6.2.3.2. DURING OPERATION IT IS ESSENTIAL TO PAY ATTENTION TO THE FOLLOWING:
The amount of the air supplied by the blow-in fan should be adjusted to the intensity of the fuel burning in the retort. It
is necessary to control the condition of the fire in the furnace:
- A red smoky fire indicates that the inflow of the air is too small
- Bright white fire indicates that the inflow of the air is too big.
- A clear, intensively yellow flame means proper fire.
Summary of Contents for EKO-TECH Series
Page 1: ...1 PL GB D 3 21 38 EKO TECH EKO TECH ...
Page 2: ...2 ...
Page 56: ...56 ...
Page 58: ...58 ...