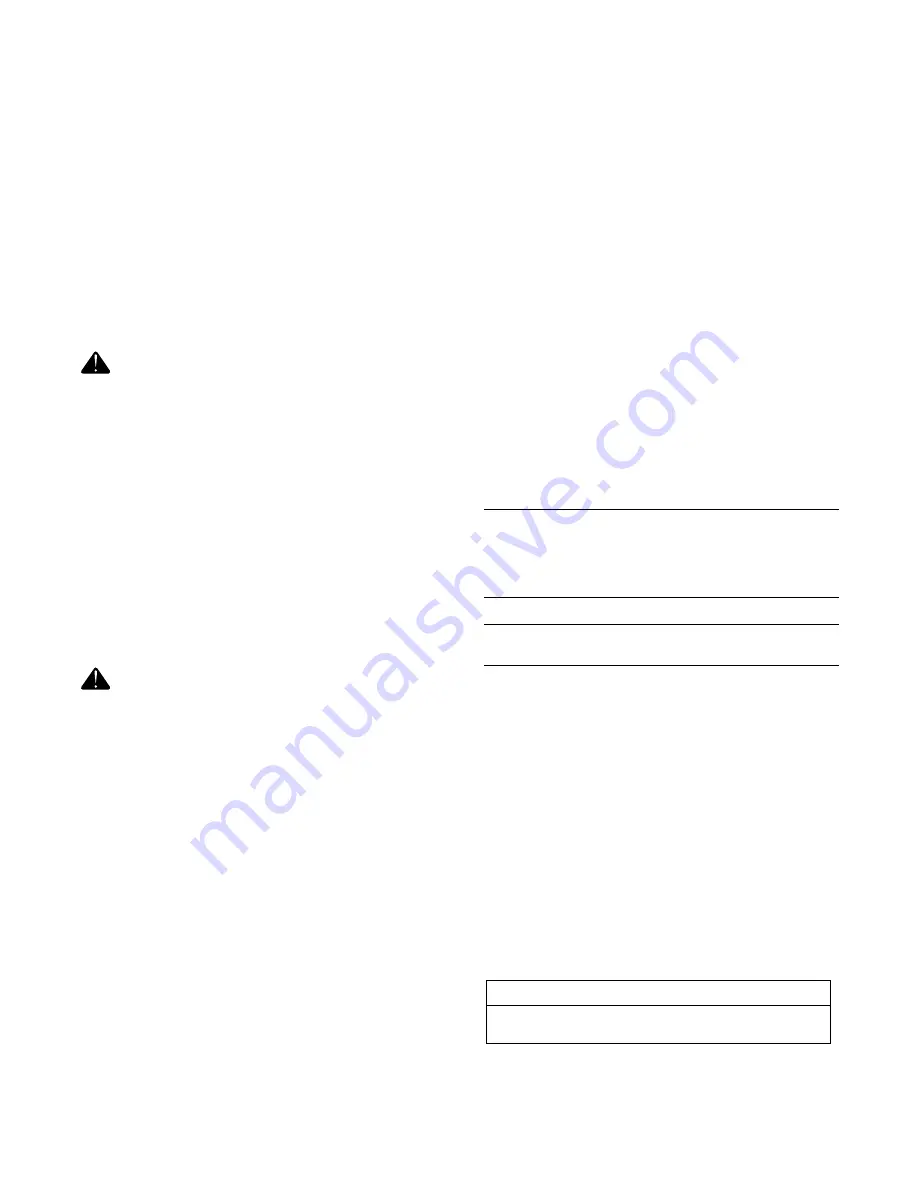
8-1
8. Hydraulic Reservoir
Disassembly and Assembly
Chapter Overview
This chapter provides disassembly and assembly
procedures for the hydraulic reservoir assembly.
Cleaning procedures are also included for the hy-
draulic reservoir.
Personal Safety
Improper or incomplete maintenance/repair of a Compact
Track Loader can be dangerous and may result in ma-
chine damage, injury or death.
Do not attempt to perform any type of repair or mainten-
ance on a Compact Track Loader until you have read and
fully understood the information in this manual.
Refer to the Operation and Maintenance manual for in-
structions regarding proper machine operation techniques
before operating any Compact Track Loader.
Prior to performing any type of service work on a
Compact Track Loader, read and understand Chap-
ter 1 (Product Safety) for personal safety informa-
tion.
Machine Preparation
Accidental machine starting can cause injury or
death to personnel working on a Compact Track
Loader.
As a precaution, disconnect the battery cables from
the battery terminals, tape the battery clamps and
remove the key from the ignition switch prior to per-
forming any service work on a Compact Track Load-
er.
Place a “Do Not Operate” tag prominently on the
machine to inform personnel that the machine is be-
ing worked on.
Hydraulic Reservoir
Disassembly and Assembly
Procedures
Disassembly and assembly procedures are provided
for the following hydraulic reservoir components.
•
Filter Element
•
Filter
Assembly
•
Filler Cap Assembly
•
Access Cover Assembly
•
Reservoir
Gauge
•
Suction Screen
Note:
Procedures are provided for only those hydraulic
reservoir components listed above. However, information
for removal and installation of other hydraulic reservoir
components can be obtained from the Compact Track
Loader Parts List manual.
Note:
Refer to Figure 3-1 for an overview of the filtering
and cooling system.
Filter Element Removal and
Installation
Refer to
Chapter 16. Maintenance – Hydraulic Fluid
and Filter
for removal and installation of the filter.
Filter Assembly Removal and
Installation
The tools required for filter assembly removal and
installation are listed in Table 8-1. Use manufactur-
er-recommended tools whenever possible.
Table 8-1
Required Tools
Combination/Socket Wrenches
Needle Nose Pliers
Summary of Contents for PT-30
Page 1: ...PT 30 Part Number 2010 513 Printed 1 11 Service Manual Compact Track Loader ...
Page 2: ......
Page 3: ......
Page 7: ......
Page 13: ...1 6 ...
Page 15: ......
Page 19: ......
Page 35: ......
Page 51: ......
Page 65: ......
Page 73: ......
Page 85: ......
Page 99: ......
Page 103: ......
Page 115: ......