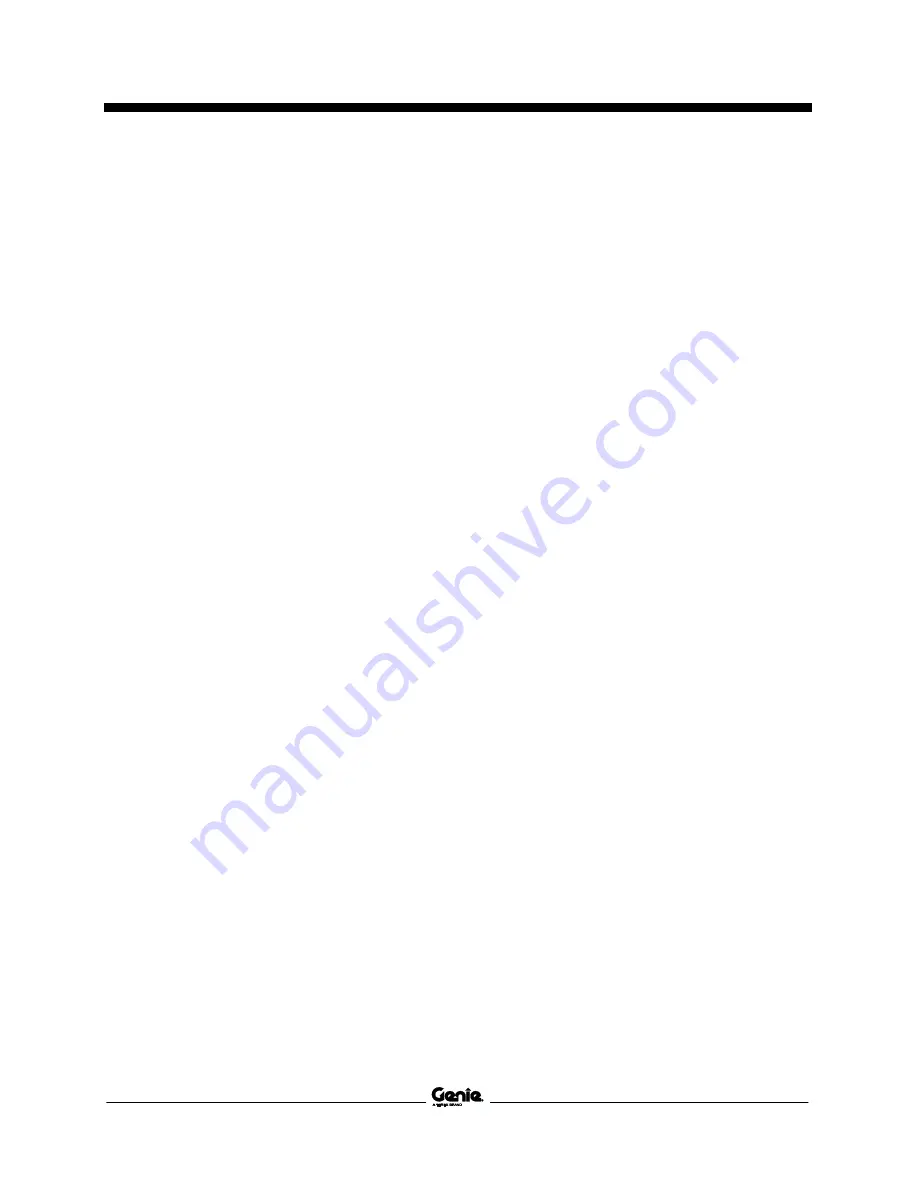
Third Edition • First Printing
Operator's Manual
Specifications
Part No. 1305656GT
GS
™
-
2669BE • GS
™
-
3369BE • GS
™
-4069BE
55
Contents of EC Declaration of Conformity
<Manufacturer’s name> hereby declares that the machinery described below complies with the provisions
of the following Directives:
1. EC Directive 2006/42/EC, Machinery Directive, under consideration of harmonized European standard
EN280 as described in EC type-examination certificate <variable field> issued by:
Kuiper Certificering B.V.
Van Slingelandtstraat 75, 7331NM
Apeldoorn
Netherlands
NB number 2842
2. EC Directive EMC: 2014/30/EU, under consideration of harmonized European standard EN
61000-6-2 and EN 61000-6-4
3. EC Directive 2000/14/EC, Noise Directive, under consideration of Annex V and harmonized standard EN
ISO 3744, internal combustion engine only.
Test Report:
This machine has been tested and passed the following categories per EN 280:2013+A1:2015 clause
6.3 prior to entering the market:
1. BRAKES: Brakes working properly in forward and reverse.
2. OVERLOAD: Overload tested at XXX% rated load.
3. FUNCTIONAL: Smooth operation at XXX% rated load.
4. FUNCTIONAL: All safety devices working correctly.
5. FUNCTIONAL: Speeds set within permitted specification.
Model / Type: <machine type>
Manufacture Date: <variable field>
Description: <machine classification>
Country of Manufacture: <variable field>
Model: <model name>
Net Installed Power: <only for IC machines>
Serial Number: <variable field>
Guaranteed Sound Power Level: <only for IC machines>
VIN: <where applicable>
Manufacturer: <Manufacturer’s name>
Authorized Representative:
Genie Industries B.V
Boekerman 5,
4751 XK Oud Gastel,
The Netherlands
Empowered signatory:
Place of Issue: <variable field>
Date of Issue: <variable field>
GS™-2669BE • GS™-3369BE • GS™-4069BE
Part No. 1305656GT
Operator's Manual
Third Edition • First Printing
Summary of Contents for Genie GS-3369BE
Page 58: ......