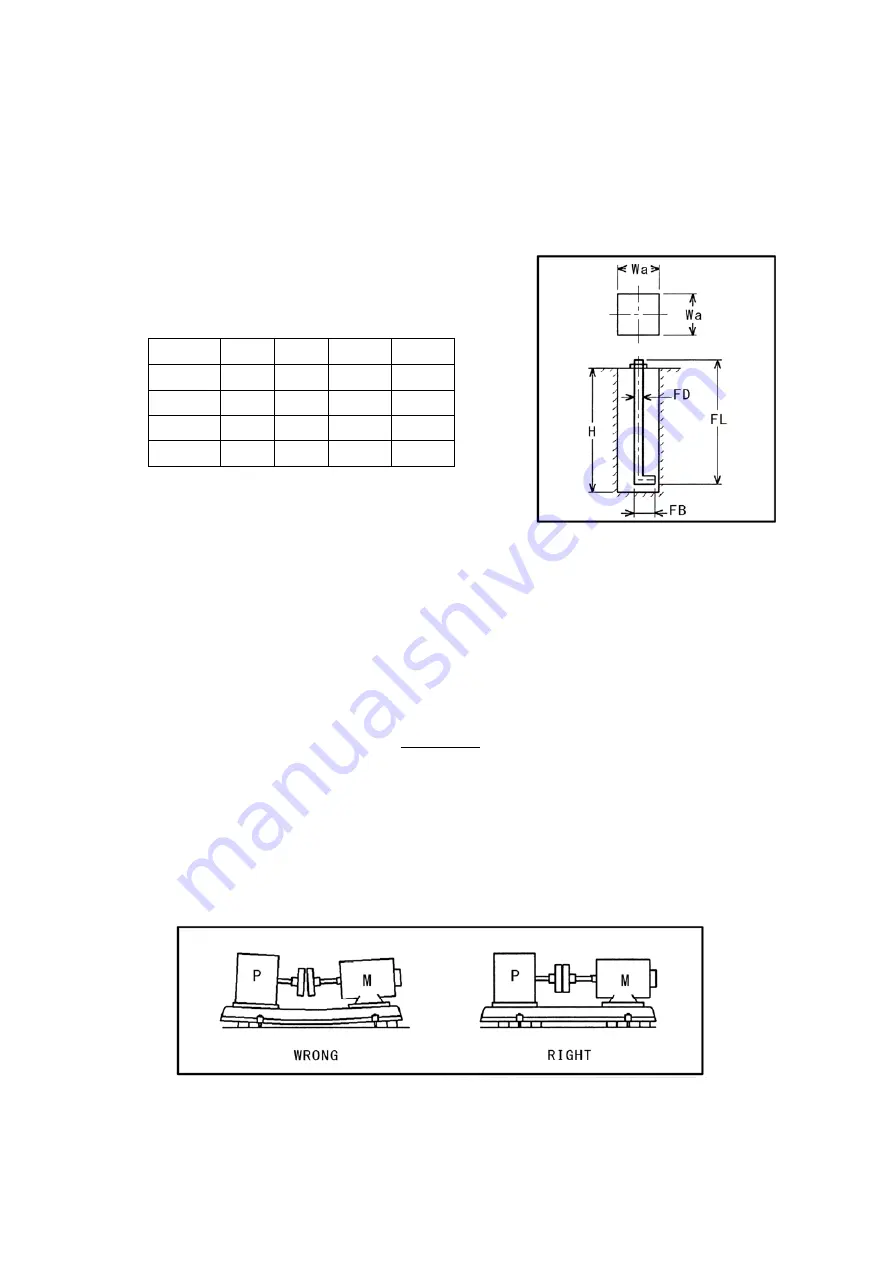
3-5
3.3 Installation procedure
(1)Provide a foundation of ample area and depth to bear the weight of the pump and its
operating load.
(2)Provide holes in the foundation in accordance with the drawings,or else using the
pump itself to determine the hole positions prior the pump is installed.
Anchor bolt and anchor bolt hole dimensions
FD
FL
FB
Wa
H
M10
200
45
100
250
M12
250
55
120
300
M16
315
70
150
370
M20
400
90
190
450
(3)Make sure that the surface of the concrete foundation is level,and protect it
thoroughly until the pump is installed.
(4)Mount the pump on the foundation.When mounting,insert square steel plates or
metal wedges between the common base and the concrete foundation,to make a gap
through which the mortar can be poured in.
(The gap should be 10-30 mm wide.)
As well as being used for adjusting the levelness of the pump,the metal wedges will
receive the pump's weight and operating load.
Use only a few wedges,that are as thick as possible.
Insert the wedges close to the anchor bolts,and locate them so that they provide
even weight.
(5)Fix the anchor bolts to the common base using the nuts,and hang them in center of
bolt holes.
N O T E
3 - 2
Summary of Contents for SJ4S
Page 23: ......