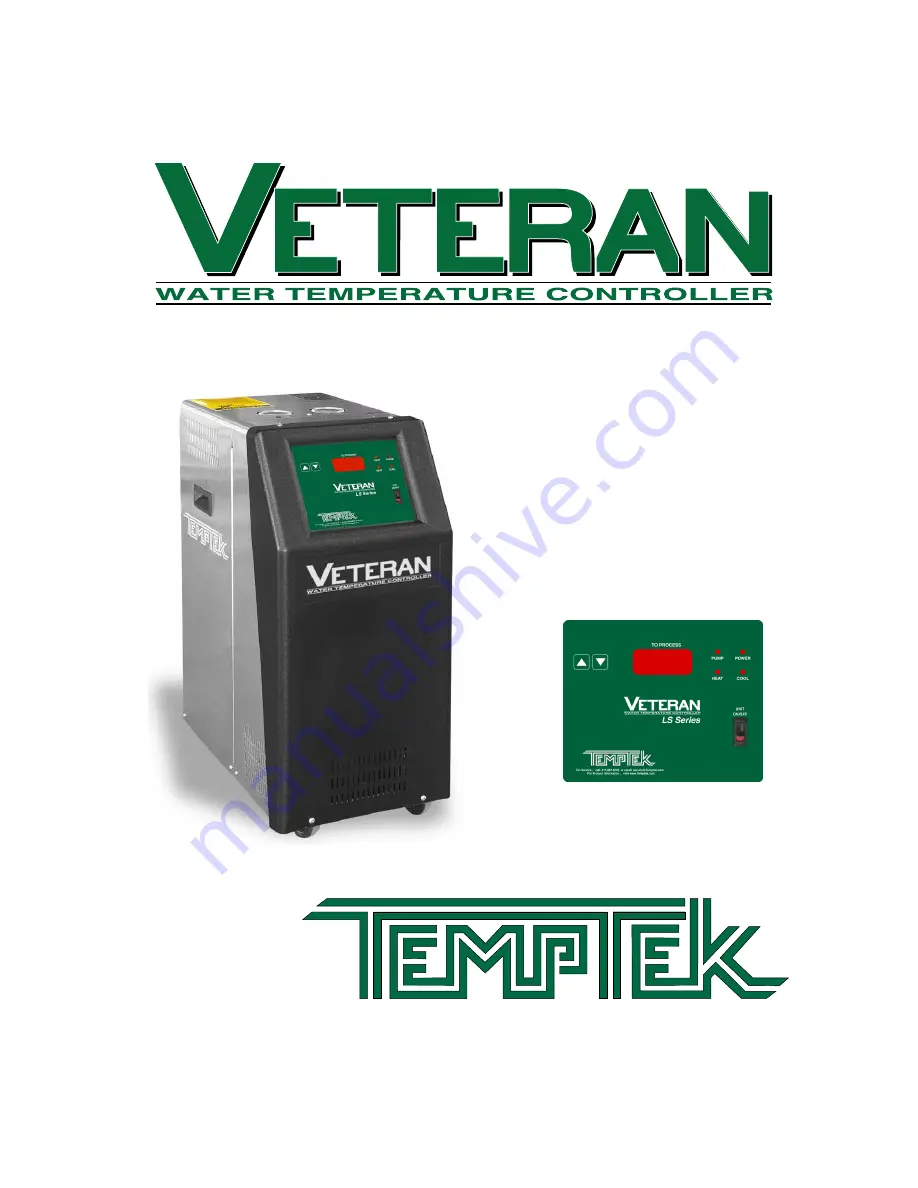
I.O.M. #092 12/06 updated 02/2013
INSTRUCTION MANUAL
• INSTALLATION • OPERATION • MAINTENANCE
TEMPTEK, INC.
525 East Stop 18 Road Greenwood, IN 46142
317-887-6352 fax: 317-881-1277
Service Department fax: 317-885-8683
www.TempTek.com
e-mail: [email protected]
Models with ‘LS’ Series Instrument.
Summary of Contents for VETERAN LS Series
Page 2: ......
Page 8: ...Page 8 THIS PAGE INTENTIONALLY BLANK ...
Page 60: ...Page 60 THIS PAGE INTENTIONALLY BLANK ...
Page 68: ...Page 68 THIS PAGE INTENTIONALLY BLANK ...
Page 78: ...Page 78 THIS PAGE INTENTIONALLY BLANK ...
Page 79: ...END 2013 Temptek INC RE 1 02 13 ...
Page 80: ......