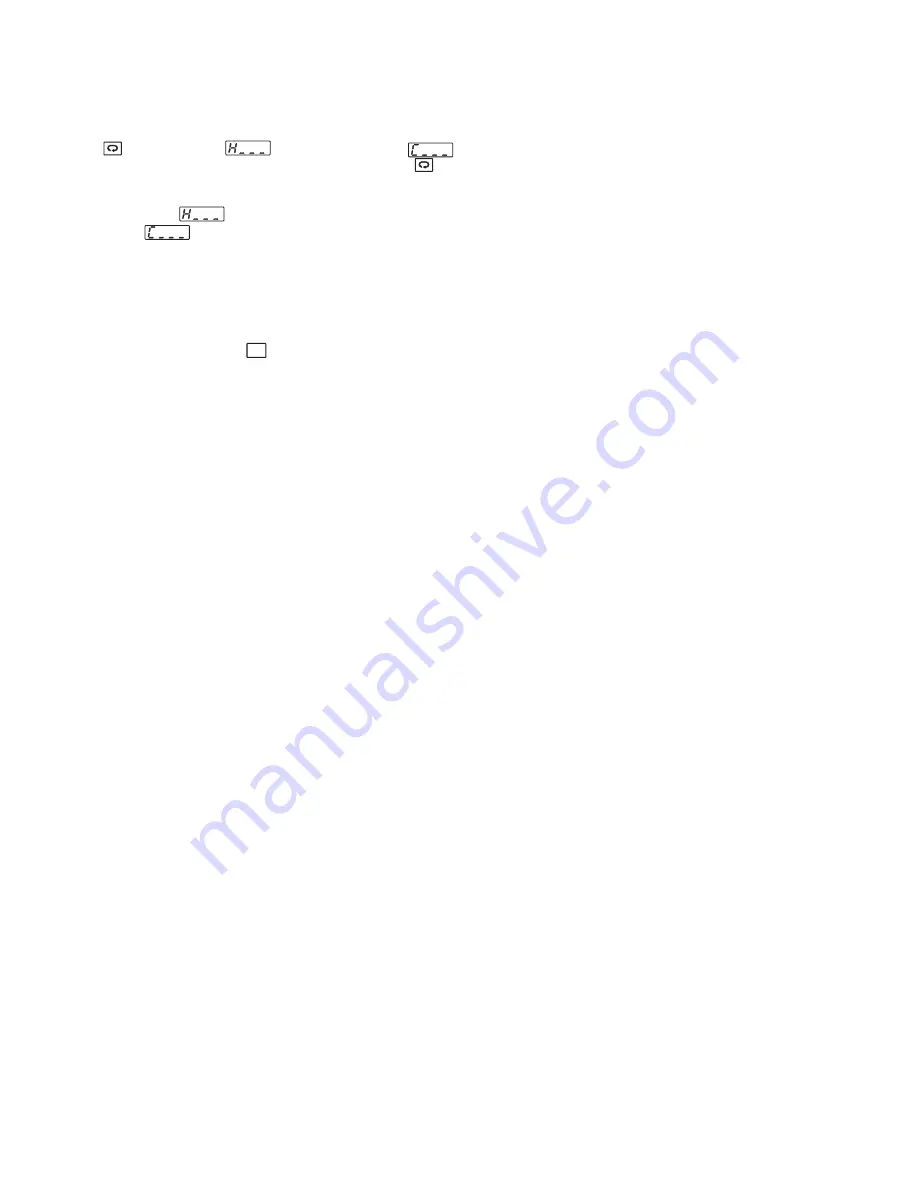
17
3–13 Manual Control
Operation:
To enable manual control, the LOCK parameter should be set to
NONE.
Press
several times;
(heating output) or
(cooling output) will appear on the display. Press and hold
for
5 seconds or until the MAN indicator (for TEC-920) or the dis-
play (for TEC-220) begins to flash. The controller is now in man-
ual control mode.
indicates output control variable for
output 1, and
indicates control variable for output 2. Now
you can use the up and down keys to adjust the percentage values
for the heating or cooling output.
The controller performs open loop control as long as it stays in
manual control mode.
Exit Manual Control
Model TEC-920: Pressing the
key will cause the controller to
revert to its normal display mode.
Model TEC-220: Press and release the up and down buttons.
R
3–14 Data Communication
The controllers support RTU mode of Modbus protocol for data
communication. Other protocols are not available for this series.
Two types of interface are available for data communication.
These are RS-485 and RS-232. Since RS-485 uses a differential
architecture to drive and sense signal instead of a single-ended
architecture like the one used for RS-232, RS-485 is less sensi-
tive to noise and more suitable for communication over a longer
distance. RS-485 can communicate without error over a 1km dis-
tance while RS-232 is not recommended for a distance of over 60
feet (20 meters).
Using a PC for data communication is the most economical
method. The signal is transmitted and received through the PC
communication port (generally RS-232). Since a standard PC
can't support an RS-485 port, a network adapter (such as
TEC99001) has to be used to convert RS-485 to RS-232 for a PC
if RS-485 is required for data communication. Up to 247 RS-485
units can be connected to one RS-232 port; therefore a PC with
four comm ports can communicate with 988 units.
Setup
Enter the setup menu. Select RTU for COMM. Set individual
addresses for any units that are connected to the same port. Set
the baud rate (BAUD), data bit (DATA), parity bit (PARI) and
stop bit (STOP) so that these values are accordant with PC setup
conditions.
If you use a conventional 9-pin RS-232 cable instead of
TEC99014, the cable should be modified for proper operation of
RS-232 communication according to section 2-9 on page 10.
Refer to Chapter 7 for a complete technical description of the
Modbus Communications Protocol.
3–15 Process Variable (PV)
Retransmission
The TEC-220 controller can output (retransmit) a process value
via its retransmission terminals RE+ and RE- provided that the
retransmission option is ordered. The correct signal type should
be selected for COMM parameter to meet the retransmission
option installed. RELO and REHI are set to specify the low
scale and high scale values of retransmission.
The TEC-920 does not have this feature.
Summary of Contents for tec-220
Page 2: ...NOTES...
Page 4: ...NOTES...
Page 8: ...4 1 5 Menu Overview...
Page 9: ...5 1 6 Parameter Descriptions...
Page 10: ...6 1 6 Parameter Descriptions continued...
Page 22: ...18 NOTES...
Page 34: ...30 Table A 1 Error Codes and Corrective Actions A 1 Error Codes...