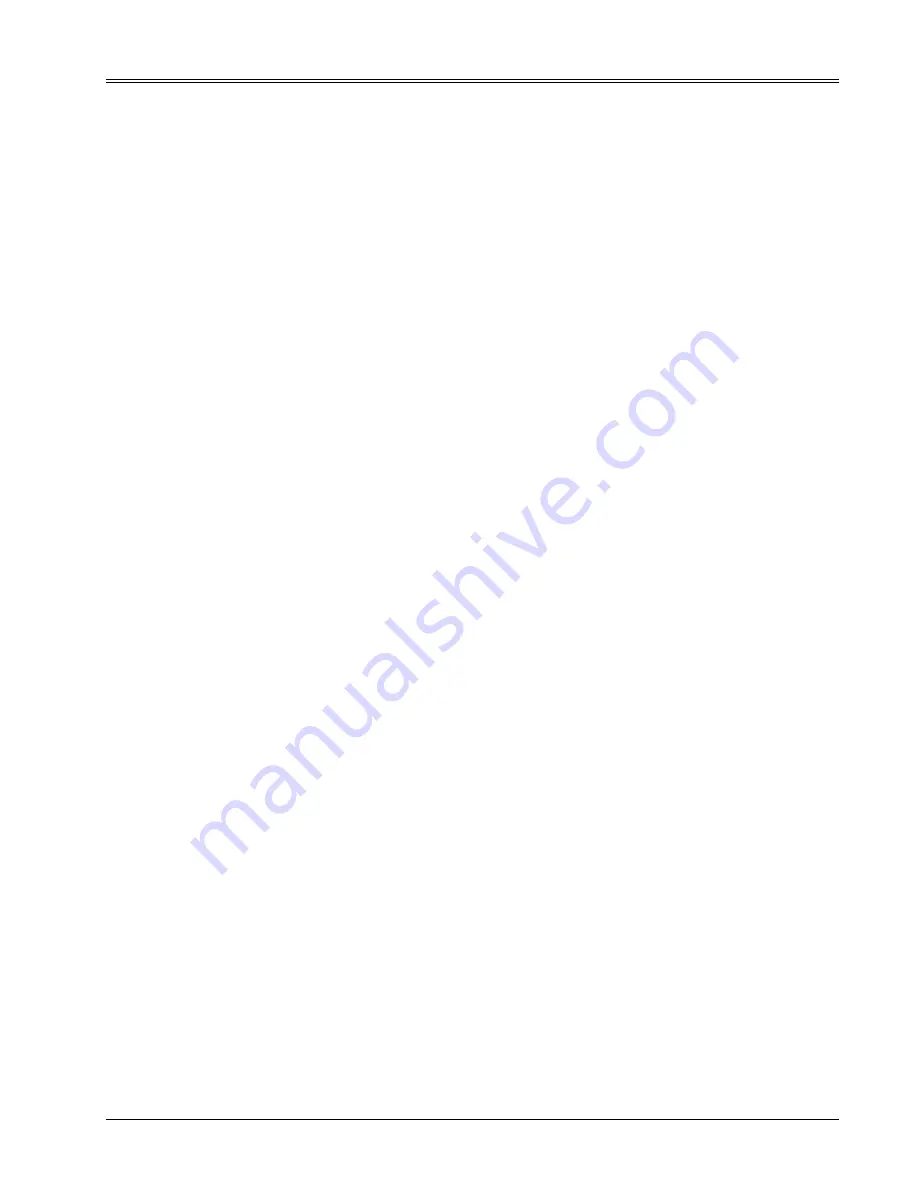
TMP4100-Series Installation/Maintenance
33480D01.DOC
A-1
Appendix A
Material Safety Data Sheets
This Appendix contains Material Safety Data Sheets (MSDS) for carbide and steel impact
pins. The impact pins are used by the TMP4100-Series marking heads for imprinting
messages into various materials.
Read the MSDS sheets prior to reconditioning pins to become familiar with potential
reconditioning hazards. Always wear a respirator, safety glasses, and gloves when grinding
metal. Use the appropriate precautions, coolant, abrasive, and grinding techniques for the pin
material as described in the Material Safety Data Sheets.
Summary of Contents for PINSTAMP TMP4100 Series
Page 2: ......
Page 10: ...TMP4100 Series Installation Maintenance viii 33480D01 DOC This page intentionally left blank...
Page 23: ...TMP4100 Series Installation Maintenance 33480D01 DOC 1 13...
Page 24: ...TMP4100 Series Installation Maintenance 1 14 33480D01 DOC This page intentionally left blank...
Page 25: ...TMP4100 Series Installation Maintenance 33480D01 DOC 1 15...
Page 28: ...TMP4100 Series Installation Maintenance 1 18 33480D01 DOC This page intentionally left blank...
Page 52: ...TMP4100 Series Installation Maintenance 2 24 33480D01 DOC This page intentionally left blank...
Page 54: ...Appendix A A 2 33480D01 DOC This page intentionally left blank...