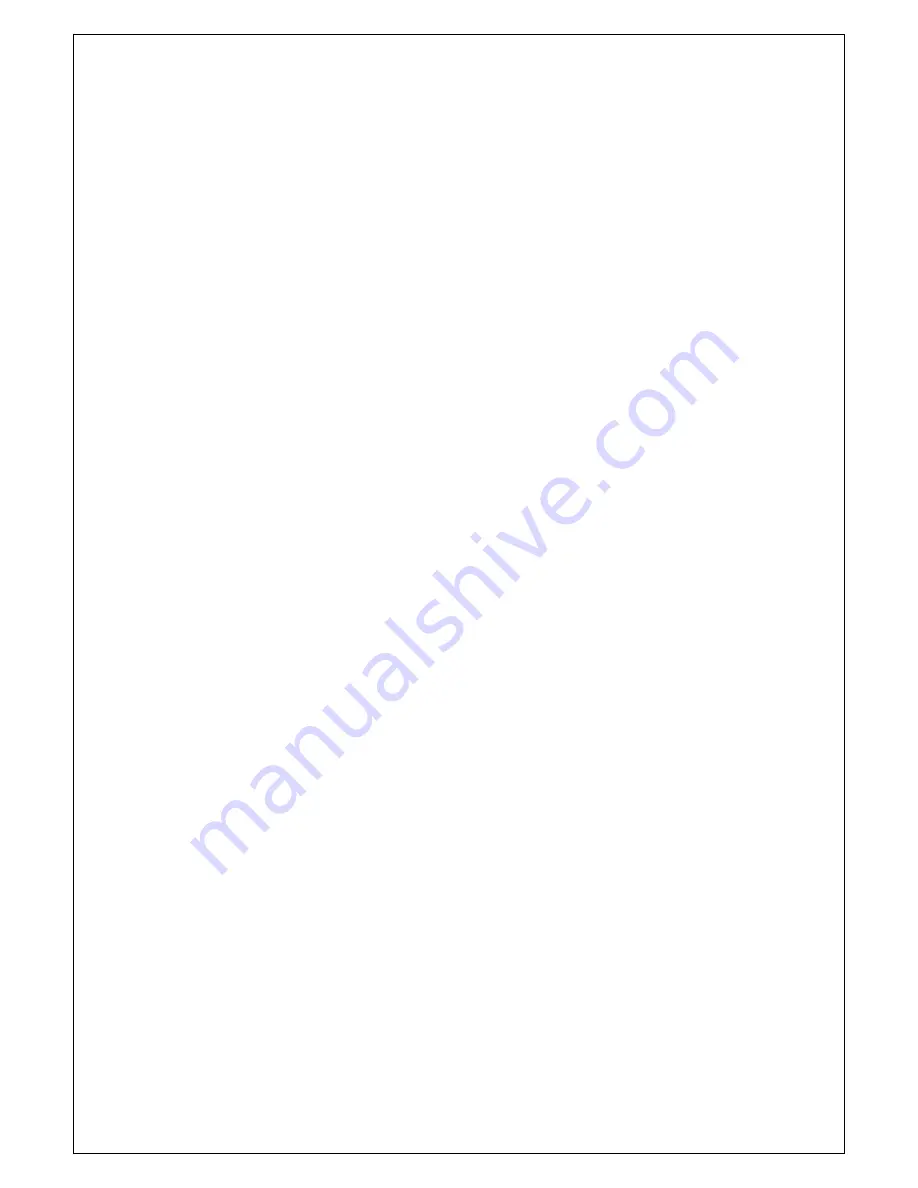
Page 6 of 6
TVP Manual (full) March 2007 CE rev 03.doc
(10) If the lines have visible frosting or water is seen to leak from them during defrost or
standby, all of the line insulation must be replaced.
(11) The most common cause of system malfunction are refrigeration leaks. Careful
attention to the integrity of the system will ensure optimal performance.
(12) Do NOT repeatedly bend the refrigerant line; this will cause leakage and or breakdown
of the insulating materials.
(13) Always attach the refrigerant line to the feed-through coupling.
(14) Leak checking should always be carried out with a helium mass spectrometer leak
detector. Any other method may lead to contamination of the system, leaks and ultimately
system failure.
(15) Detecting leaks without a helium mass spectrometer is difficult and time consuming for
all but the grossest of leaks. The leak rate should be less than 5 x 10
-8
mbar/L/S this is outside
of the detection range of hand held halogen sniffer.
(16) Most leaks are found at the connections of refrigerant lines, pay particular attention to
these areas. It is important that these joints are checked regularly throughout the life of the
installation.
(17) Failure to identify and repair leaks before operation will lead to poor performance
system contamination and in extreme cases total system failure. In such cases the Warranty
will be invalidated.
(18) Ensure the Cryocoil is located in a vacuum chamber and that the chamber is evacuated
to at least 0.01 Torr or 1 x 10
-2
mbar to prevent overheating of the coil from latent heat.
(19) Before any leaks are repaired the refrigerant mixture must be drawn back into the TVP
unit. Using an oil free refrigerant reclaim unit. This requires an experienced technician.
Details of how this maybe achieved are outside the scope of this manual.
(20) Do not operate the unit if a refrigerant leak is suspected. Be very careful not to pull a
vacuum within the refrigeration lines as this will lead to contamination of the system by water.
(21) Failure to adequately insulate and protect refrigerant feed lines and couplings will result
in reduced cryotrap performance, including possible failure of the entire system.
(22) The system uses highly stable PT100 sensors, the temperature measurement system is
designed for long-term reliability and stability of temperature measurement. Inferring vacuum
performance from the CI/CO values is an unreliable method of process determination. Direct
measurement and observation of the vacuum through either an RGA or Penning type gauge
are the only reliable methods of evaluating the actual process conditions present.
(23) For process safety reasons the interface has the following command hierarchy:
COOL - Overrides all other actions.
DEFROST - Will revert to STANDBY when complete.
STANDBY - Default state.
(24) To prevent system damage check controlling systems status and the interface is
correctly wired before attempting to connect to the TVP.