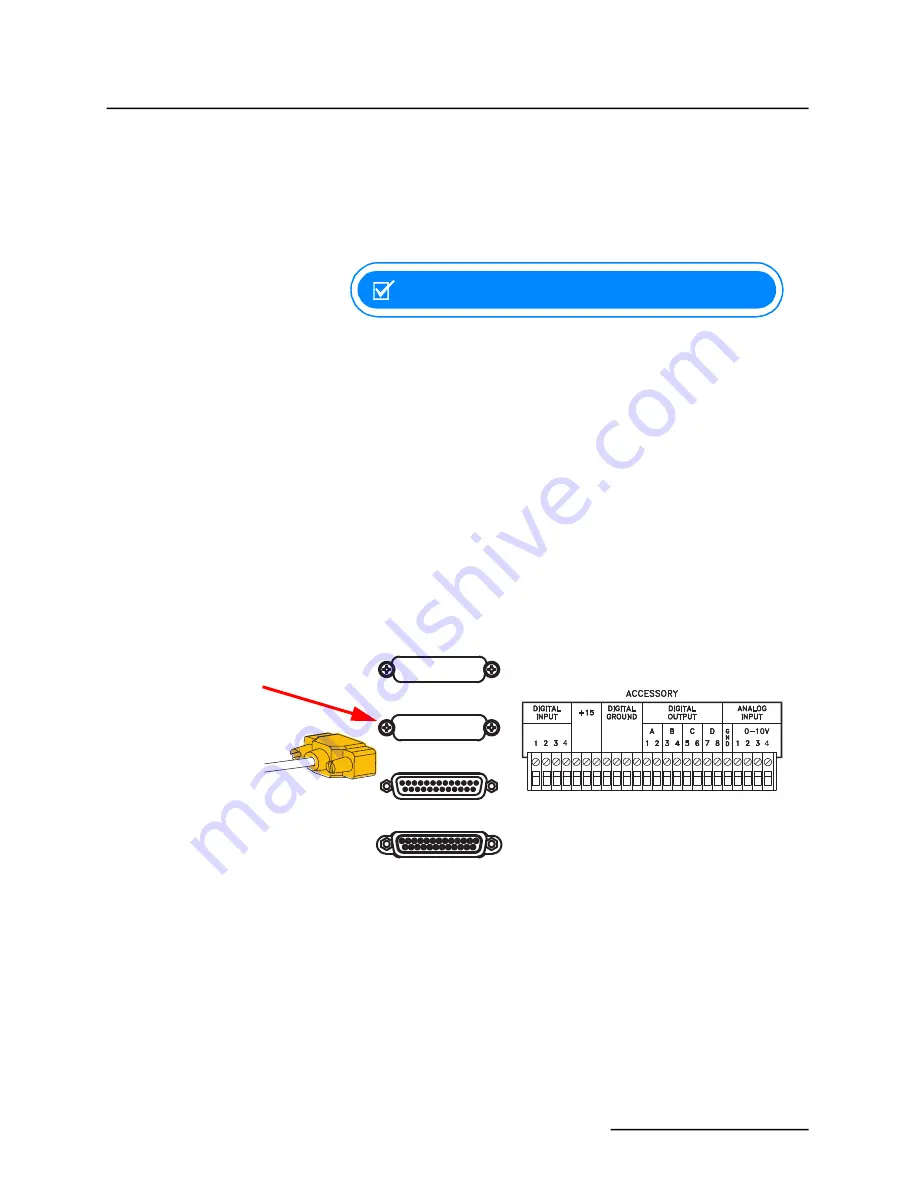
SyriXus Series Pumps Installation and Operation Guide
Section 3 Basic Programming and Operation
3-25
EAR99 Technology Subject to Restrictions Contained on the Cover Page
•
If two pumps are used with the controller, the second control
wire should be connected to terminal 2, under DIGITAL INPUT.
•
If three pumps are used with the controller, the third control
wire should be connected to terminal 3, under DIGITAL INPUT.
•
If four pumps are used with the controller, the fourth control
wire should be connected to terminal 4, under DIGITAL INPUT.
NOTE
For the 4-20ma option, the negative current wire is connected to
DIGITAL GROUND and the positive should be connected to DIGI-
TAL INPUT
3.14 Analog Flow Rate
and Volume
Output Options
The analog output option provides for analog monitoring of the
syringe pump flow rate. If two or less pump modules are connected to
the controller, pump volume delivered can also be monitored via
analog output. These outputs are often used with analog based plant
or process monitoring equipment.
3.14.1 Voltage Analog
Output
Output voltage for pressure is located on the back panel of the pump
module via standard banana jacks. Refer to Figure 1-6.
If the analog output board is installed at the factory, the output con-
nection is the female 25-pin Sub-D connector located on the rear panel
of the controller, under the 4-20mA Output label. Refer to Figure 1-5.
Figure 3-14 Analog voltage output connection, rear panel
Voltage analog outputs are pre-installed at the factory. This option has
a total of four outputs for monitoring flow rate with selectable ranges
from 0 to 5V, -5 to +5V, and 0 to 10V. The default range at installation
is 0 to 10V. Each output can be set to a different range.
The top of the selected range is the same maximum value entered for
MAX
FLOW
when setting
LIMITS
, as described in Section 3.8.7 "LIMITS"
of this manual. For example: if the output range is 5V and the pre-
ferred output scale is 1 volt per 10 mL/min,
MAX
FLOW
is set at
50 mL/min.
MAX
FLOW
cannot exceed the pump specification.
Controller rear panel
25-pin cable
DIGITAL I/O
4-20mA OUTPUT
USB / ETHERNET
RS-232 / RS-485
This Output can be one
of the Following:
4-20mA OUTPUT
ANALOG OUTPUT
ELECTRIC VALVES
12-CH OUTPUT