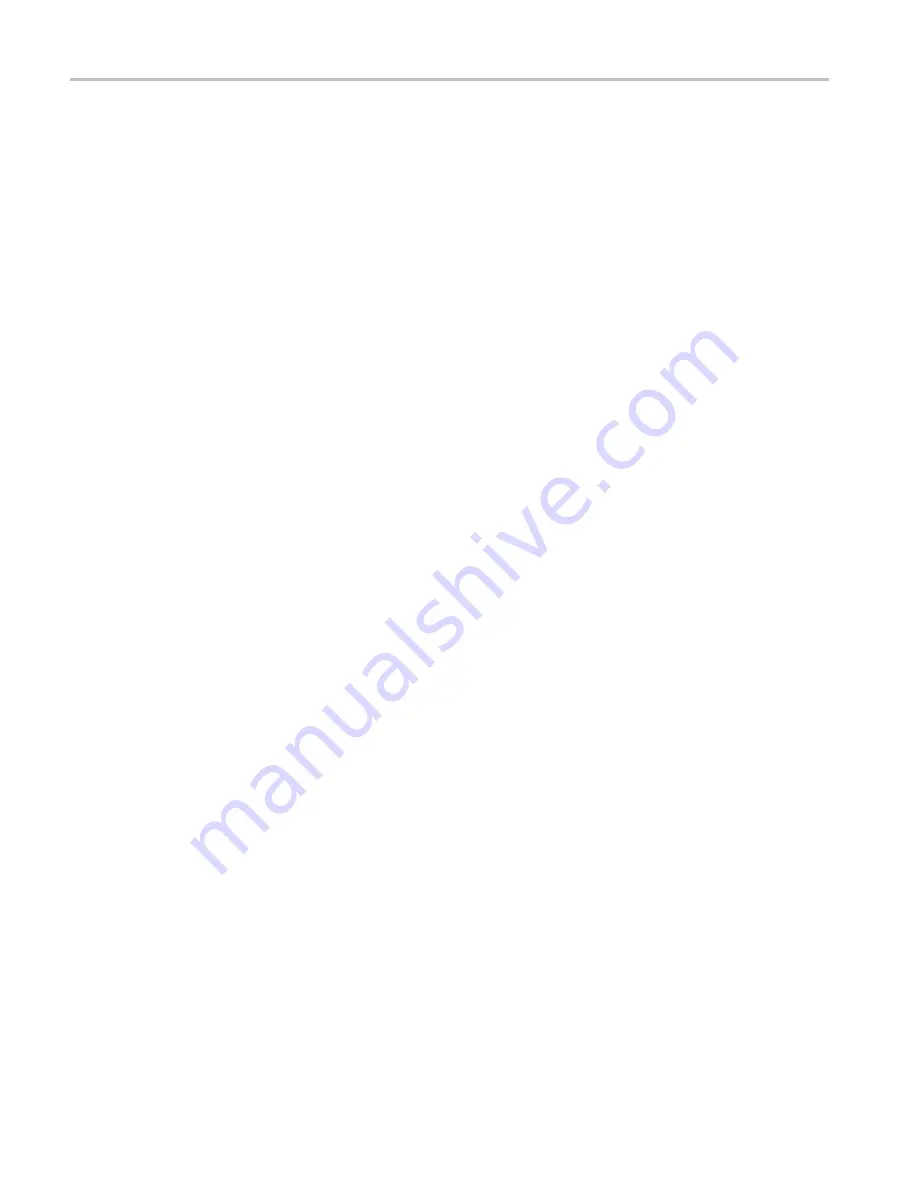
General Safety Summary
General Safety Summary
Review the following safety precautions to avoid injury and prevent damage to
this product or any products connected to it.
To avoid potential hazards, use this product only as speci
fi
ed.
Only quali
fi
ed personnel should perform service procedures.
While using this product, you may need to access other parts of a larger system.
Read the safety sections of the other component manuals for warnings and
cautions related to operating the system.
To Avoid Fire or Personal
Injury
Use proper power cord.
Use only the power cord speci
fi
ed for this product and
certi
fi
ed for the country of use.
Ground the product.
This product is grounded through the grounding conductor
of the power cord. To avoid electric shock, the grounding conductor must be
connected to earth ground. Before making connections to the input or output
terminals of the product, ensure that the product is properly grounded.
Observe all terminal ratings.
To avoid
fi
re or shock hazard, observe all ratings
and markings on the product. Consult the product manual for further ratings
information before making connections to the product.
Do not apply a potential to any terminal, including the common terminal, that
exceeds the maximum rating of that terminal.
Power disconnect.
The power cord disconnects the product from the power source.
Do not block the power cord; it must remain accessible to the user at all times.
Do not operate without covers.
Do not operate this product with covers or panels
removed.
Do not operate with suspected failures.
If you suspect that there is damage to this
product, have it inspected by quali
fi
ed service personnel.
Avoid exposed circuitry.
Do not touch exposed connections and components when
power is present.
Use proper AC adapter.
Use only the AC adapter speci
fi
ed for this product.
Do not operate in wet/damp conditions.
Do not operate in an explosive atmosphere.
Keep product surfaces clean and dry.
Provide proper ventilation.
Refer to the manual’s installation instructions for
details on installing the product so it has proper ventilation.
iv
WVR4000 and WVR5000 Service Manual
Summary of Contents for WVR4000
Page 1: ...xx WVR4000 and WVR5000 Waveform Rasterizers ZZZ Service Manual P077244901 077 2449 01...
Page 2: ......
Page 6: ......
Page 18: ...Theory of Operation Figure 1 Block diagram 4 WVR4000 and WVR5000 Service Manual...
Page 39: ...Removal and Replacement Procedures Figure 3 WVR overview WVR4000 and WVR5000 Service Manual 25...
Page 42: ...Removal and Replacement Procedures Figure 6 Main board 28 WVR4000 and WVR5000 Service Manual...