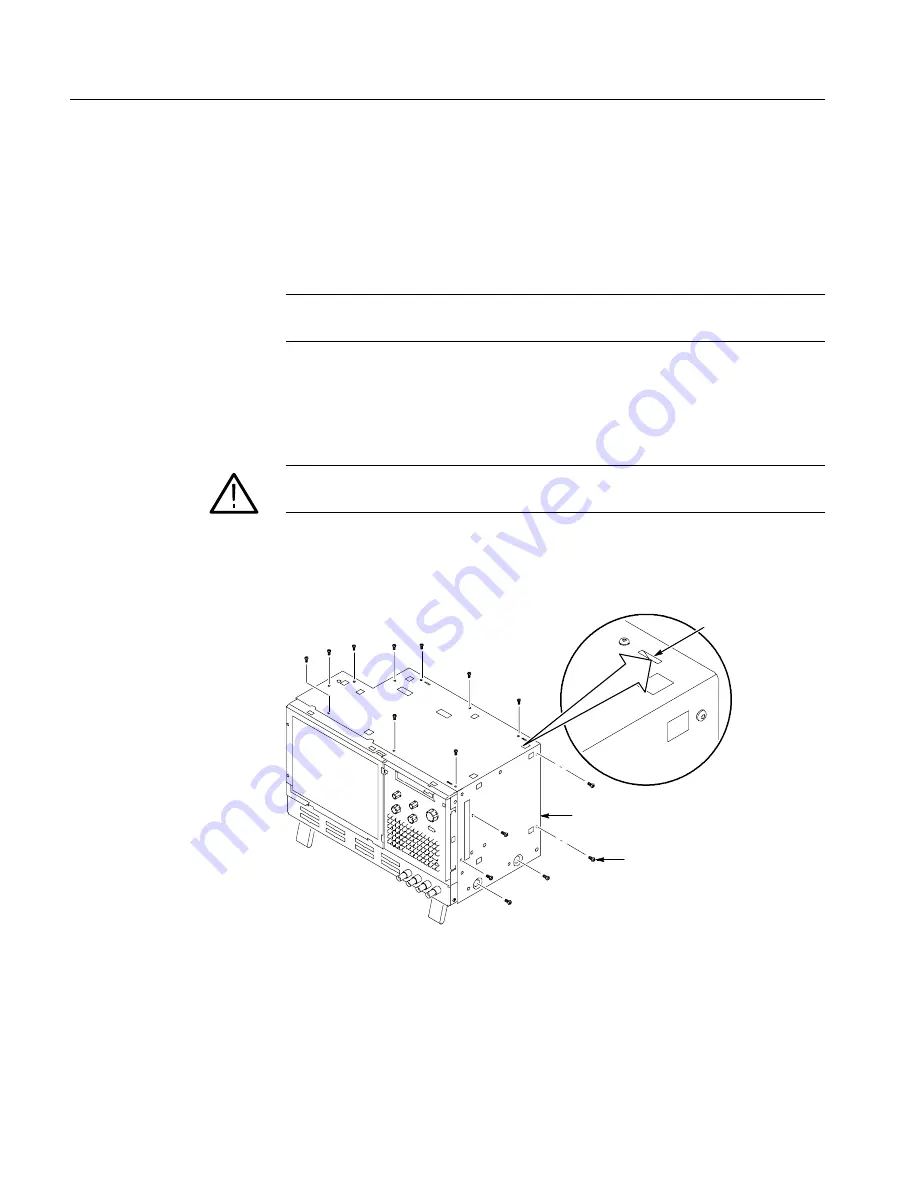
Removal and Installation Procedures
6- 10
TLA5000 Series Service Manual
Right-Side Cover
Remove the right-side cover to access most of the internal components of the
instrument. Refer to Figure 6--2 while removing the right-side cover.
1.
Remove the top and right trim to access the right-side cover.
NOTE
. All mounting screw holes are indicated by a star etched around the
mounting hole.
2.
Remove the 15 T-15 Torx-drive screws that secure the cover to the top and
right sides of the chassis.
3.
Remove the cover.
CAUTION.
Take care not to bind or snag the covers on the internal cabling as you
remove or install.
4.
To reinstall the right-side cover reverse steps 1 through 3. Tighten the T-15
Torx-drive screws to 8-in lbs.
T-15 Torx-drive
screws (14)
Right side cover
Tab
Figure 6- 2: Right-side cover removal
Summary of Contents for TLA5201
Page 5: ......
Page 13: ...Table of Contents viii TLA5000 Series Service Manual...
Page 17: ...Service Safety Summary xii TLA5000 Series Service Manual...
Page 21: ...Preface xvi TLA5000 Series Service Manual...
Page 27: ...Specifications 1 2 TLA5000 Series Service Manual...
Page 35: ...Operating Information 2 8 TLA5000 Series Service Manual...
Page 61: ...Performance Verification 4 22 TLA5000 Series Service Manual...
Page 73: ...Maintenance 6 4 TLA5000 Series Service Manual...
Page 105: ...Removal and Installation Procedures 6 36 TLA5000 Series Service Manual...
Page 119: ...Repackaging Instructions 6 50 TLA5000 Series Service Manual...
Page 121: ...Options 7 2 TLA5000 Series Service Manual...
Page 123: ...Electrical Parts List 8 2 TLA5000 Series Service Manual...
Page 125: ...Diagrams 9 2 TLA5000 Series Service Manual...
Page 132: ...Mechanical Parts List TLA5000 Series Service Manual 10 7 1 2 3 4 2 Figure 10 2 Inner panels...
Page 136: ...Mechanical Parts List TLA5000 Series Service Manual 10 11...