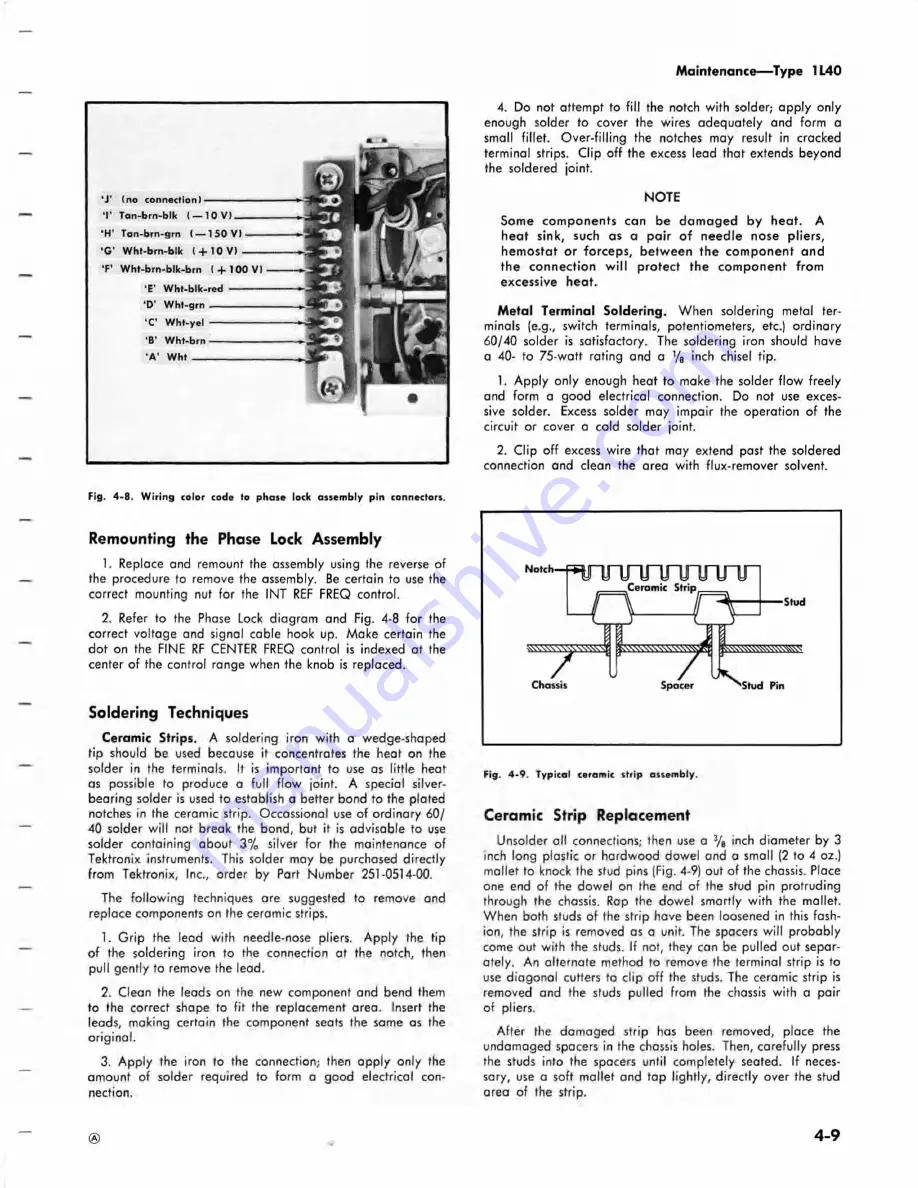
Maintenance— Type 1L40
'J' (no co n nection )---------
‘ I’
T a n -b r n - b f k ( —
10 V)
■H’ Tan-brn-grn ( — 1 50 V)
•G' W h t-b rn -b lk ( + 10 V) .
‘F’ W h t-b rn -b lk-b rn ( + 100 VI
•E’ W h t-b lk-re d -----------
*D' W h )- g rn -----------------
‘ C’ W ht-ye l -----------------
B' W h t-b rn -----------------
■A' W h t _____________
Fig. 4 -8 . W irin g color code to phase lock assembly pin connectors.
Remounting the Phase Lock Assembly
1. Replace and remount the assembly using the reverse of
the procedure to remove the assembly. Be certain to use the
correct mounting nut for the INT REF FREQ control.
2. Refer to the Phase Lock diagram and Fig. 4-8 for the
correct voltage and signal cable hook up. Make certain the
dot on the FINE RF CENTER FREQ control is indexed at the
center of the control range when the knob is replaced.
Soldering Techniques
Ceramic Strips.
A soldering iron with a wedge-shaped
tip should be used because it concentrates the heat on the
solder in the terminals. It is important to use as little heat
as possible to produce a full flow joint. A special silver
bearing solder is used to establish a better bond to the plated
notches in the ceramic strip. Occassional use of ordinary 60/
40 solder w ill not break the bond, but it is advisable to use
solder containing about 3% silver for the maintenance of
Tektronix instruments. This solder may be purchased directly
from Tektronix, Inc., order by Part Number 251-0514-00.
The following techniques are suggested to remove and
replace components on the ceramic strips.
1. G rip the lead with needle-nose pliers. A pply the tip
of the soldering iron to the connection at the notch, then
pull gently to remove the lead.
2. Clean the leads on the new component and bend them
to the correct shape to fit the replacement area. Insert the
leads, making certain the component seats the same as the
original.
3. A pply the iron to the connection; then apply only the
amount of solder required to form a good electrical con
nection.
4. Do not attempt to fill the notch with solder; apply only
enough solder to cover the wires adequately and form a
small fillet. Over-filling the notches may result in cracked
terminal strips. Clip off the excess lead that extends beyond
the soldered joint.
NOTE
Some com ponents can be d am aged by heat. A
heat sink, such as a p a ir o f needle nose pliers,
hem ostat or forceps, betw een the com ponent and
th e connection w ill protect the com ponent from
excessive heat.
M etal Terminal Soldering.
When soldering metal ter
minals (e.g., switch terminals, potentiometers, etc.) ordinary
60/40 solder is satisfactory. The soldering iron should have
a 40- to 75-watt rating and a Vs inch chisel tip.
1. Apply only enough heat to make the solder flow freely
and form a good electrical connection. Do not use exces
sive solder. Excess solder may impair the operation of the
circuit or cover a cold solder joint.
2. Clip off excess wire that may extend past the soldered
connection and clean the area with flux-remover solvent.
No,eh^n ru in n n n riJ in
______.Ceramic Strip.______
-Stud
Chassis
Spacer
K .
Stud Pin
Fig. 4 -9 . Typical ceramic strip assembly.
Ceramic Strip Replacement
Unsolder all connections; then use a 3/8 inch diameter by 3
inch long plastic or hardwood dowel and a small (2 to 4 oz.)
mallet to knock the stud pins (Fig. 4-9) out of the chassis. Place
one end of the dowel on the end of the stud pin protruding
through the chassis. Rap the dowel smartly with the mallet.
When both studs of the strip have been loosened in this fash
ion, the strip is removed as a unit. The spacers w ill probably
come out with the studs. If not, they can be pulled out separ
ately. An alternate method to remove the terminal strip is to
use diagonal cutters to clip o ff the studs. The ceramic strip is
removed and the studs pulled from the chassis with a pair
of pliers.
After the damaged strip has been removed, place the
undamaged spacers in the chassis holes. Then, carefully press
the studs into the spacers until completely seated. If neces
sary, use a soft mallet and tap lightly, directly over the stud
area of the strip.
®
4-9
Summary of Contents for 1L40
Page 30: ...Fig 3 1 Type 1L40 Block Diagram CO K ISO 2 5 0 MHz 75 MHz Circuit Description Type 1L40 ...
Page 40: ...NOTES ...
Page 54: ...NOTES ...
Page 85: ...NOTES ...
Page 103: ......
Page 117: ...I ...
Page 119: ...T Y P E I L 4 0 S F t C T R U M A N A U V t R A ...
Page 120: ...L R O G 8 R F P H A S E L O C K D I A G R A M A ...
Page 124: ... 75V T Y P L I L A Q S P f c C T R U M A N A L Y Z t R ...
Page 126: ... T y p t S P E C T R u M A N A U V 2 f e R A ...
Page 127: ...4 A P H A S t L O C K C I R C U I T ...
Page 128: ...iv r AMPUH19 1 rRon J9A 4 T Y P E L 4 0 S P E C T R U M A N A L Y Z C R A I ...
Page 130: ......
Page 134: ... IS MHZ IP lO M Hx OSCILLATOR r T Y P E IL 4 0 SPECTRUM ANALYZED ...
Page 135: ... lL I z 5 a or lJ ui Ul X i u tt O a i d id u it l h 5 12 2 a or PO S 3 J3 ...
Page 139: ...DETECTORS i 4 1066 OUTPUT AMPLIPIER ...
Page 140: ...FIG 1 FRONT REAR TYPE 1L40 SPECTRUM ANALYZER ...
Page 141: ...FIG 2 IF CHASSIS PHASE LOCK AS 6 1 ...
Page 142: ...F CHASSIS PHASE LOCK ASSEMBLIES TYPE 1L40 SPECTRUM ANALYZER ...
Page 145: ......