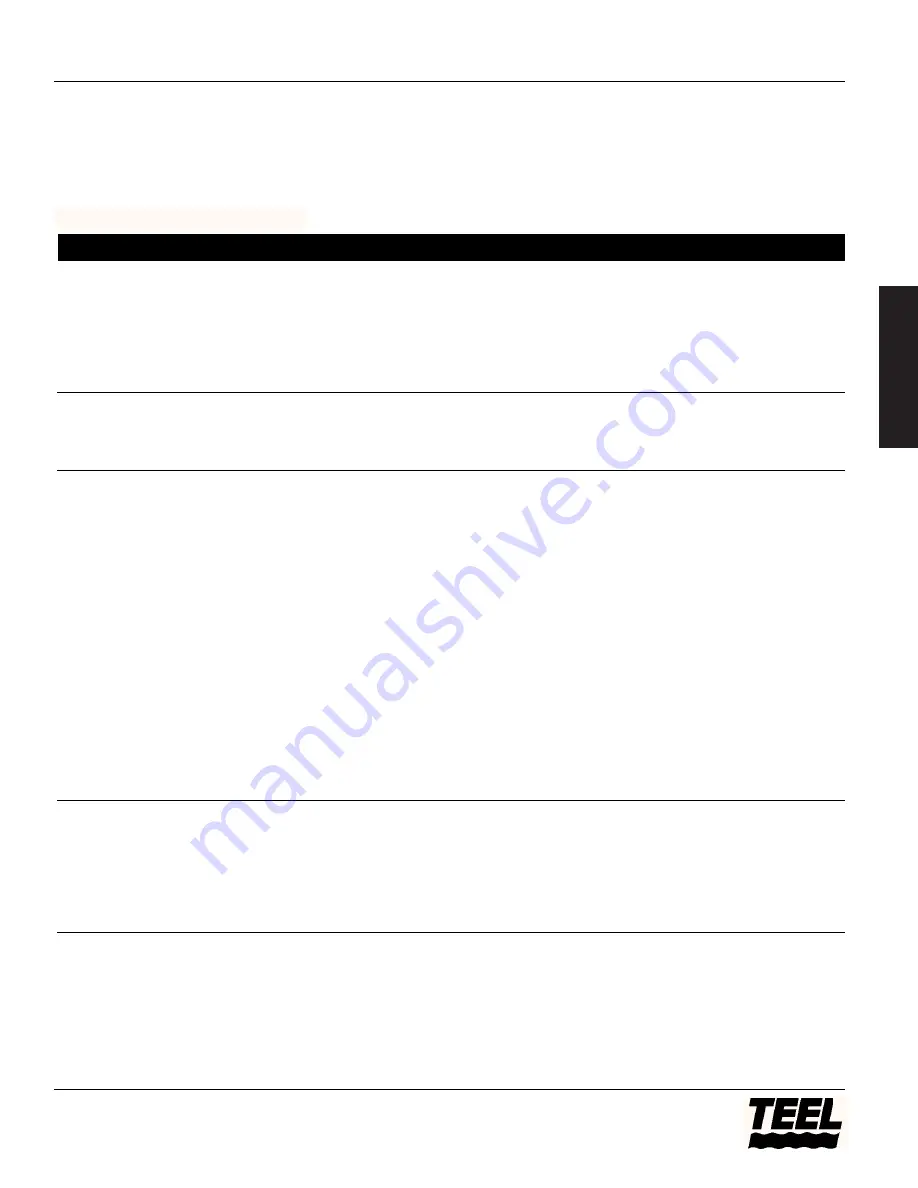
21
N
G
H
Motor will not run
1. Disconnect switch is off
1. Be sure switch is on
2. Fuse is blown
2. Replace fuse
3. Starting switch is defective
3. DISCONNECT POWER; replace starting switch
4. Wires at motor are loose, disconnected,
4. Refer to instructions on wiring. DISCONNECT
or wired incorrectly
POWER; check and tighten all wiring
5. Pressure switch contacts are dirty
5. DISCONNECT POWER; clean by sliding a piece of
plain paper between contacts
Motor runs hot and
1. Motor is wired incorrectly
1. Refer to instructions on wiring
overload kicks off
2. Voltage is too low
2. Check with power company. Install heavier wiring
if wire size is too small. See wiring instructions
3. Pump cycles too frequently
3. See section below on too frequent cycling
Motor runs but no
*1. Pump in a new installation did not
1. In new installation:
water is delivered
pick up prime through:
a. Improper priming
a. Re-prime according to instructions
b. Air leaks
b. Check all connections on suction line and ejector
c. Leaking foot valve
c. Replace foot valve
*2. Pump has lost its prime through:
2. In installation already in use:
a. Air leaks
a. Check all connections on suction line,
ejector and shaft seal
b. Water level below suction of pump
b. Lower suction line into water and re-prime. If
receding water level in a shallow well operation
exceeds 25’, a deep well pump is needed
3. Ejector or impeller is plugged
3. Clean ejector or impeller; see Maintenance
4. Check or foot valves stuck in closed
4. Replace check valve or foot valve
position
5. Frozen pipe
5. Thaw pipes. Bury pipes below frost line. Heat pit
or pump house
6. Foot valve and/or strainer are buried in
6. Raise foot valve and/or strainer above well bottom
sand or mud
Pump does not deliver 1. Water level in well is lower
1. A deep well jet may be needed
water to full capacity
than estimated
(over 25 ft. to water)
(also check point 3
2. Steel piping (if used) is corroded or
2. Replace with plastic pipe where possible,
immediately
limed, causing excess friction
otherwise with new steel pipe
above)
3. Offset piping is too small in size
3. Use larger offset piping
4. New Installation. Motor wired for
4. Check voltage of incoming power supply.
230V, working at 115V
Rewire as necessary
Pump pumps water
1. Pressure switch is out of adjustment or
1. DISCONNECT POWER; adjust or replace pressure
but does not shut off
contacts are welded together
switch
(also check point 4
2. Faucets have been left open
2. Close faucets
immediately above)
3. Ejector or impeller is clogged
3. Clean ejector or impeller
4. Water level in well is lower than estimated 4. Check possibility of using a deep well jet pump
Teel Operating Instructions and Parts Manual
4RJ47, 4RJ48, 4RJ49, 4RJ50, 4P035A and 4P036A
Teel Heavy Duty Cast Iron
Convertible Jet Pumps
®
®
Symptom
Possible Cause(s)
Corrective Action
Troubleshooting Chart
*(NOTE: Check
prime before
looking for other
causes. Unscrew
priming plug and
see there is
water in priming
hole)