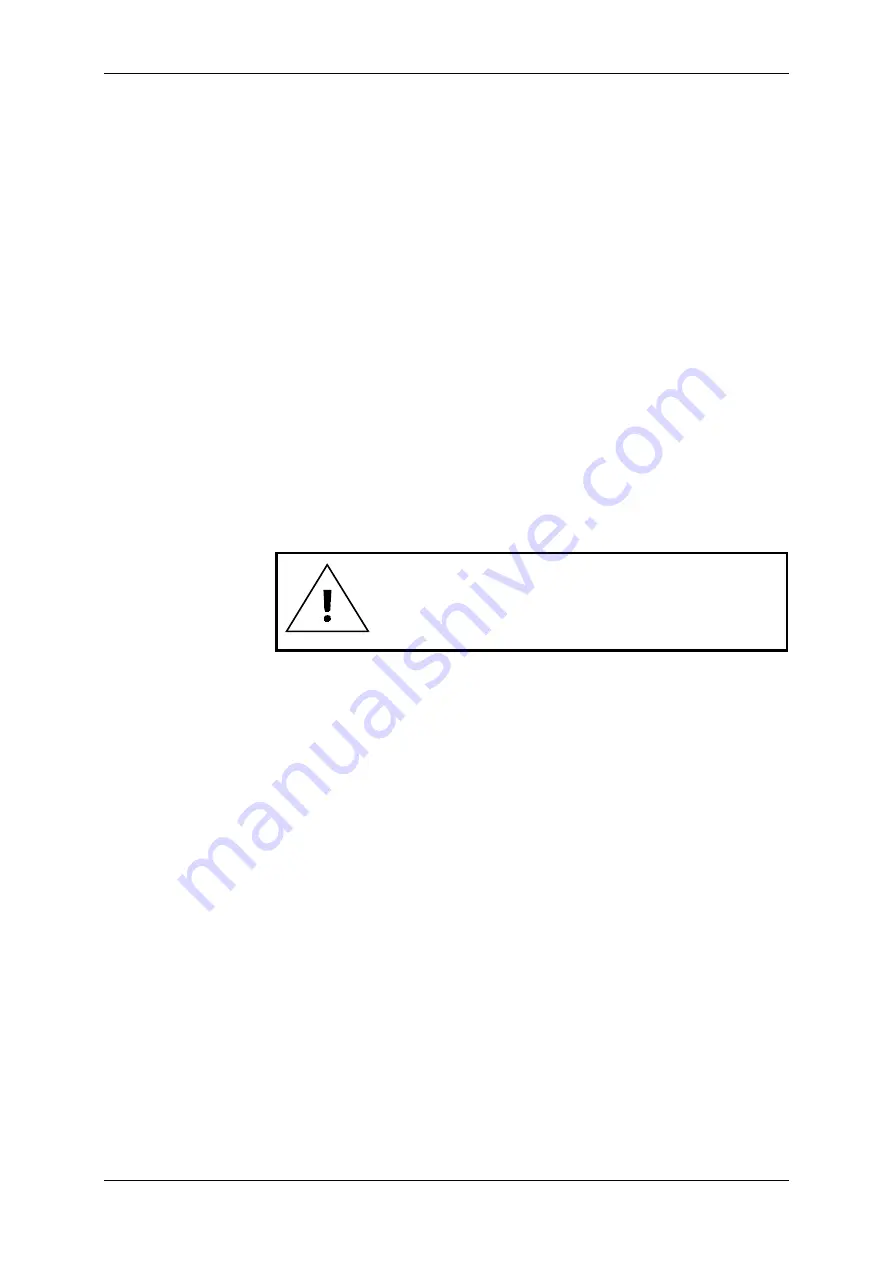
Tecomat TC600
TXV 138 08.02
96
Allowed voltage tolerance for closing of fast inputs (DI0 to DI3 of mod-
ules TC603 to TC607) is
17,5 V~
to 30 V~
or 18,5 V- to 30 V-. Allowed volt-
age tolerance for opening of the input is
0 V~
to 13,5 V~
or 0 V- to 14 V-.
13.5 Checking of Voltage of Binary Transistor Outputs
Voltage of binary transistor outputs is measured between connectors
UDO and GND of the relevant group of outputs. Allowed voltage range is
9.6 V- to 28.8 V-.
13.6 Battery Exchange
Exchanging of the battery (Panasonic CR2032 or a similar lithium battery
of 3 V, 210 mAh,
20 mm) can be performed without losing of the user pro-
gram and set parameters in the following way:
turn off the PLC and inputs and outputs power supply
remove the BM cover
disconnect jumper V1 (next to the battery)
take out the battery (on the upper edge of the CPU board)
insert a new battery
connect jumper V1
screw on the BM cover
When the battery is disconnected (jumper V1 is disconnected), memory
of the user program and the RTC circuit are supplied for the period of about
5 minutes from the backing condenser.
Metal instruments which could short-circuit the battery (for
example the tweezers, flat pincers etc.) must not be used
to insert the new battery. Pay attention to correct polarity.
The recommended interval of the battery exchange is 5 years. For the
way of indication of lower battery voltage see Article 4.2.
13.7 Fuse Exchange
The internal fuse of the voltage converter can be exchanged without
demounting of the BM cover through a cut-out on the bottom side of the
cover. Non-breaking of the fuse is signalled by the lighted green LED diode
placed behind the fuse when the regulator power supply is on. Type and
value of the fuse are given on the label close to the fuse. Exchange of the
fuse is done with the PLC power supply turned off.
13.8 Cleaning
To clean the PLC, no solvents, diluents, alcohols or similar substances
may be used. To clean the surface covered by labels, it is possible to use
fabric imbued with some diluted detergent cleaning means. Cleaning of
dusty units is performed by a stream of air.
14. The Guarantee
Guarantee and reclamation conditions follow the
Commercial Conditions
of Teco a.s..