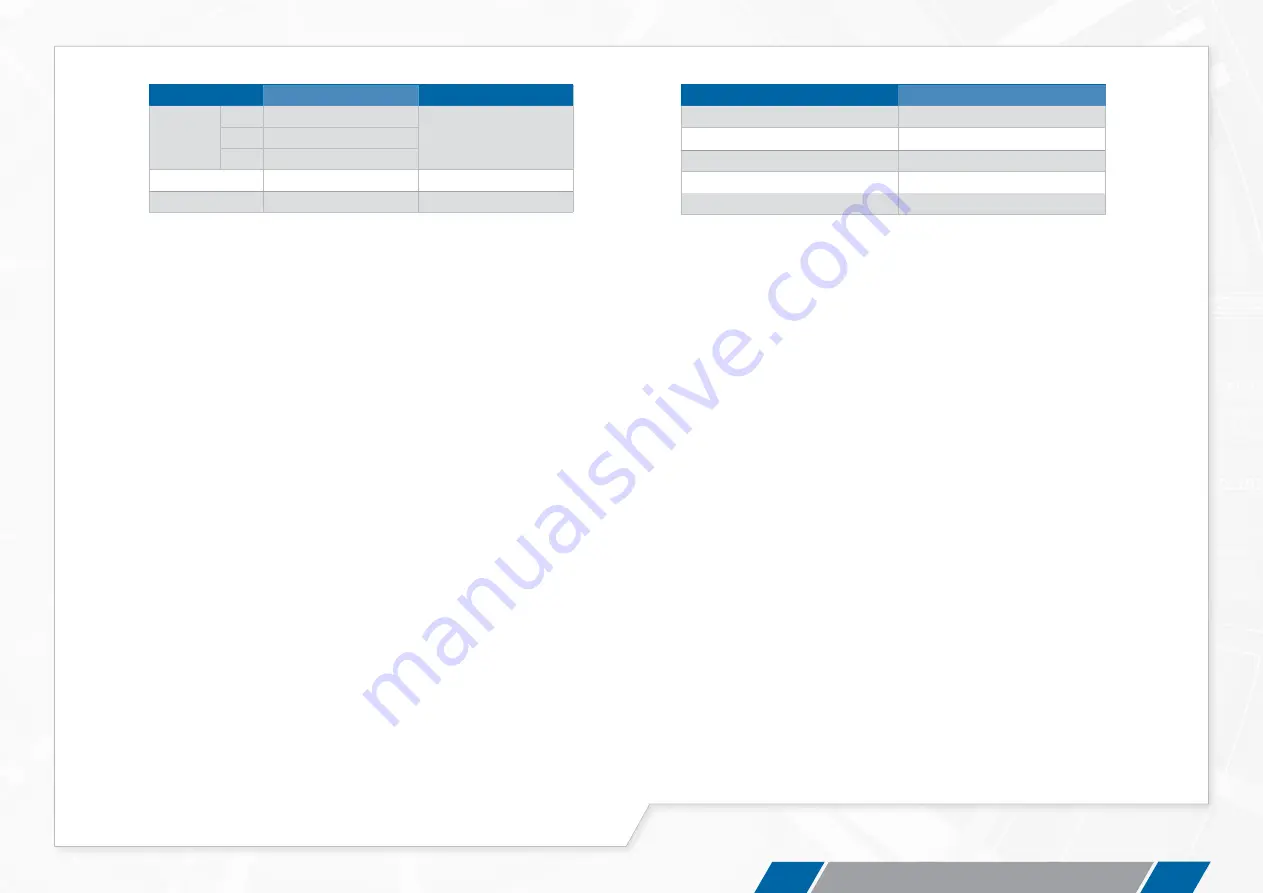
©2016 Tecnotion BV - All rights reserved - The contents of this document are subject to change without prior notice.
16
Tecnotion
| www.tecnotion.com | [email protected]
Ironless linear mot
or manual - v
er
. 1.03
INSTALLATION
CH 3
Powercable
Color code
Connection to servo controller
3-phases
L1
black
3-phases
L2
red
L3
white
Protective Earth
green/yellow
Protective Earth
Shield
(Protective) Earth
Table 3.11: Powercables wire identification
3.7.3 Protective earth
Be sure that the earth shield of the cable is well connected – also through
the connecting devices – to the PE connector or the housing of the ampli-
fier. Most linear motors are driven on the principle of pulse width modula-
tion. This involves large electrical impulses and causes a significant risk of
electromagnetical interference.
Internally the motor’s PE wire (green/yellow) is galvanic connected to the
motor housing. This wire must be connected to the PE connector of the
servo amplifier. Provide the motor system with PE lines to the amplifier that
are as short as possible.
3.7.4 Temperature Sensor
The coil unit of the UM,UL,UXA and UXX Linear Motors come equipped
with two temperature sensors, one PTC-1k-type and one NTC-sensor. The
UF series has only a NTC-sensor. The UC series has no temperature sensors.
For more details about both sensor see the next three paragraphs.
The temperature cable consists of four wires. For wire color and function,
see table 3.12.
Sensor cable (color)
Connection to servo controller
PTC (white)
PTC
PTC (brown)
PTC
NTC (green )
NTC
NTC (yellow)
NTC
Shield
Protective Earth
Table 3.12: Sensor cable wire identification
3.7.5 Temperature protection
The temperature sensors are normally used for overheating protection of
the coil unit. The NTC-sensor can be used for monitoring temperature, the
PTC can be used as cut off sensor when the maximal temperature is ex-
ceeded. For specifications and characteristics see the next two paragraphs.
In cases where long peak currents are demanded, the thermal response
time of the coil unit is too long to ensure a proper overheating protection
by the sensors. The temperature sensors can ensure a proper protection up
to an Irms of 25% of the peak current of the motor. This corresponds to a
temperature increase of 4,5°C/s.
These long peak current conditions can occur for example during an acci-
dental run or by taking a new axis in control.
In this case I²t protection is essential to prevent the coil unit from overhe-
ating. In almost all controllers an I²t-protention can be set in the software.
For more information contact Tecnotion’s Application support team.