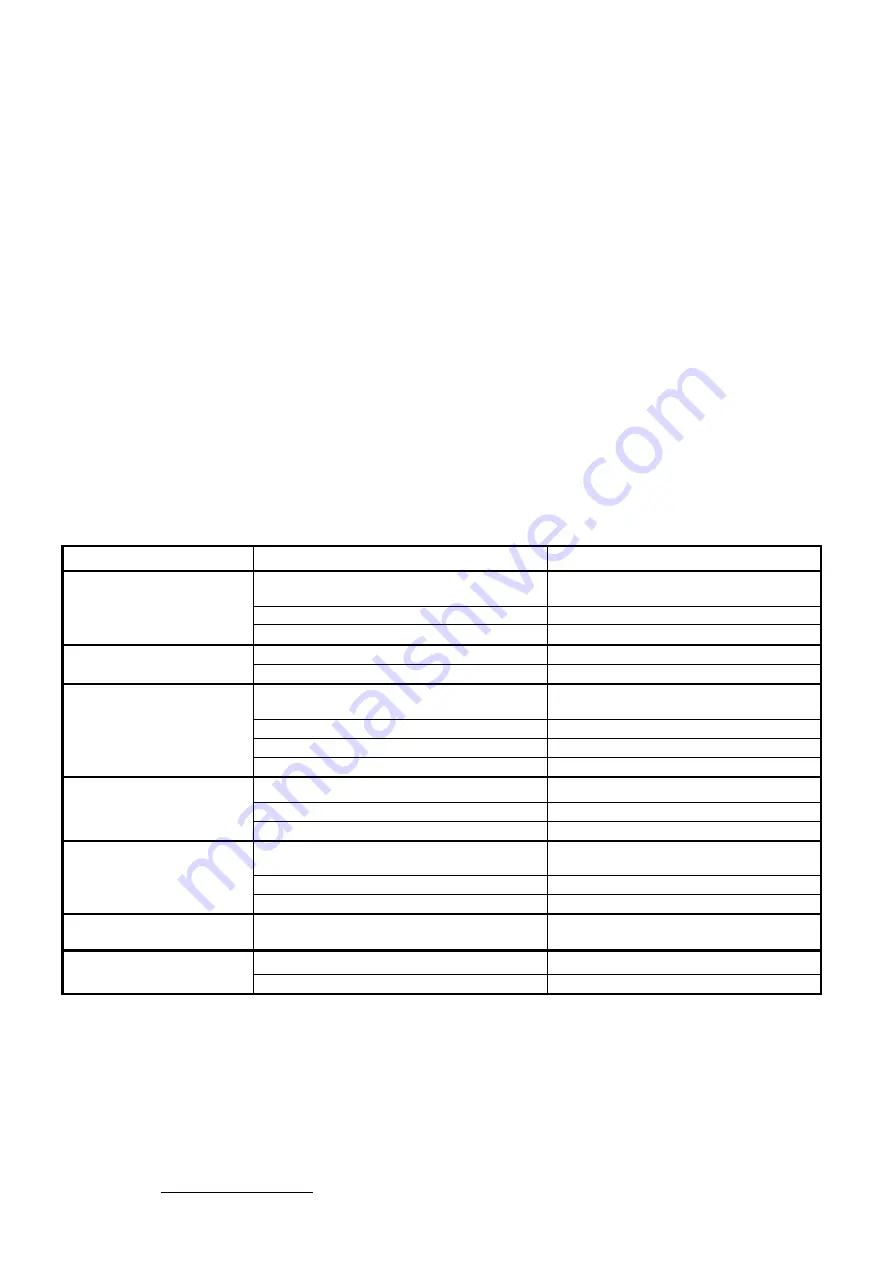
11
used. A common glass detergent may be used also to clean the external door glass. In any case one may
simply use warm soapy water. After rinsing dry the glass surface well with a soft cloth.
Should opaque spots form between the two glass panes, these may be removed as they are inspectable.
3.6 Cleaning the external casing
The outer steel surfaces must be cleaned with a cloth soaked in warm soapy water or mixed with a little
vinegar, they must be rinsed well and dried with a soft cloth.
Should you wish to use specific products on the market, these must comply with the cleaning requirements
set out in the “Information for the user” paragraph.
It is worth remembering that the counter supporting the appliance, or the floor surrounding the appliance
area, should also be cleaned without using acid corrosive substances (e.g. muriatic acid) since the vapours
released by them might corrode and deteriorate the outer steel shell and cause irreparable damage to the
electrical components inside the appliance.
3.7 Inactivity period
Should the appliance not be used for a long extent of time, it is good practice to disconnect it from the
power supply (act on the safety magnetic circuit breaker located upstream of the appliance) and water
supply. It is recommended to clean it with care internally (cooking chamber) and externally, paying special
attention to removing any salt residues which might lead to corrosion on the steel surfaces.
It is also recommended to protect the appliance with oil-based spray products (e.g. Vaseline oil) which form
an effective protective film when sprayed on the surfaces.
Leave the door of the cooking chamber ajar.
Adequately covering the appliance, finally, allows it to be protected from dust.
4. TROUBLESHOOTING
5. TECHNICAL SUPPORT
Before leaving the factory this appliance has been calibrated and tested by experienced and skilled
personnel in order to obtain the best operating results. Any repair or calibration must be carried
out with the utmost care and attention, using only original parts.
That is why it is required to always contact the Dealer who has sold the appliance or our nearest
Technical Support Centre, specifying the kind of failure and the model of the appliance you have.
The parts required for adaptation to different types of gas are provided with the appliance hence
supplied upon sale or delivery.
For servicing needs the user may contact Tecnoeka on the numbers shown on the cover, or refer to
the website www.tecnoeka.com.
Type of fault
Cause of the fault
Corrective action
Control panel warning
lights totally off
(The oven does not work)
-
Non-compliant connection to the power
mains
-
Check the connection to the mains
-
No mains voltage
-
Restore the power supply voltage
-
Safety thermal device triggered
-
Restore the safety thermal device
Cooking cycle set: the oven
does not work
-
Door open or ajar
-
Close the door properly
-
Door sensor damaged
-
Contact a skilled technician
Automatic humidifier
active: no humidity/steam
production in the cooking
chamber
-
Non-compliant water mains connection
-
Check the connection to the water
mains
-
Closed stopcock
-
Check the cock
-
Obstructed water inlet filter
-
Clean the filter
-
Damaged water inlet solenoid valve
-
Contact a skilled technician
Closed door: steam escapes
through the gasket
-
Non-compliant gasket assembly
-
Check gasket assembly
-
Damaged gasket
-
Contact a skilled technician
-
Handle “nose” adjusted incorrectly
-
Contact a skilled technician
The oven does not cook
evenly
-
One of the motors is down or operates at
low speed
-
Contact a skilled technician
-
The motors do not reverse direction
-
Contact a skilled technician
-
Resistor not powered or damaged
-
Contact a skilled technician
Lamp (LED) in the cooking
chamber does not work
-
Lamp (LED) damaged
-
Replace the lamp (LED)
The thermal safety device is
activated continuously
-
Damaged device
-
Contact a skilled technician
-
Control thermostat damaged
-
Contact a skilled technician