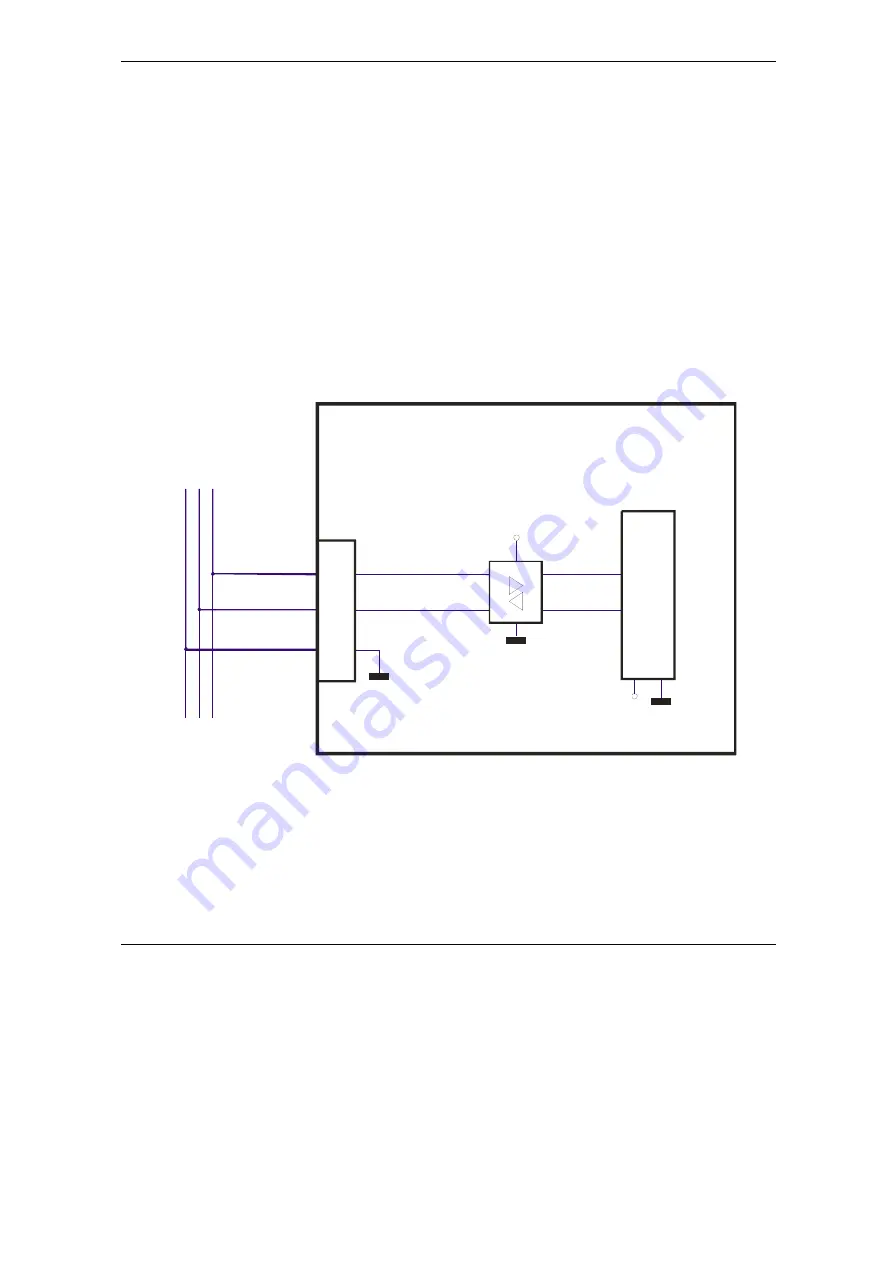
©
Technosoft 2007
37
PIM2401 Technical Reference
3.2.11.2 Recommendation for wiring
a) If you build the serial cable, you can use a 3-wire shield cable with shield connected to
BOTH ends. Do not use the shield as GND. The ground wire (pin 14 of J1) must be
included inside the shield, like the RxD and TxD signals
b) Do not rely on an earthed PC to provide the PIM2401 GND connection! The drive must
be earthed through a separate circuit. Most communication problems are caused by the
lack of such connection
c) Always power-off all the PIM2401 supplies before inserting/removing the RS-232 serial
connector.
3.2.12. CAN connection
3.2.12.1 CAN connection
12
J1
GND
+3.3V
13
IBL2401 v1.0
CAN_H
CAN_L
CAN connection
PIM2401 v1.0
CAN transceiver
+5V
To Previous Node
To Next Node
14
Mo
ti
o
n
C
h
ip
TM
Figure 3.21.
CAN connection
Remarks:
1. The CAN network requires a 120-Ohm terminator. This is not included on the board.
See Figure 4.14.
2. CAN signals are not insulated from other PIM2401 circuits.
Summary of Contents for PIM2401
Page 2: ......
Page 4: ......
Page 8: ... Technosoft 2007 VI PIM2401 Technical Reference ...
Page 90: ... Technosoft 2007 80 PIM2401 Technical Reference This page is empty ...
Page 91: ......
Page 92: ......