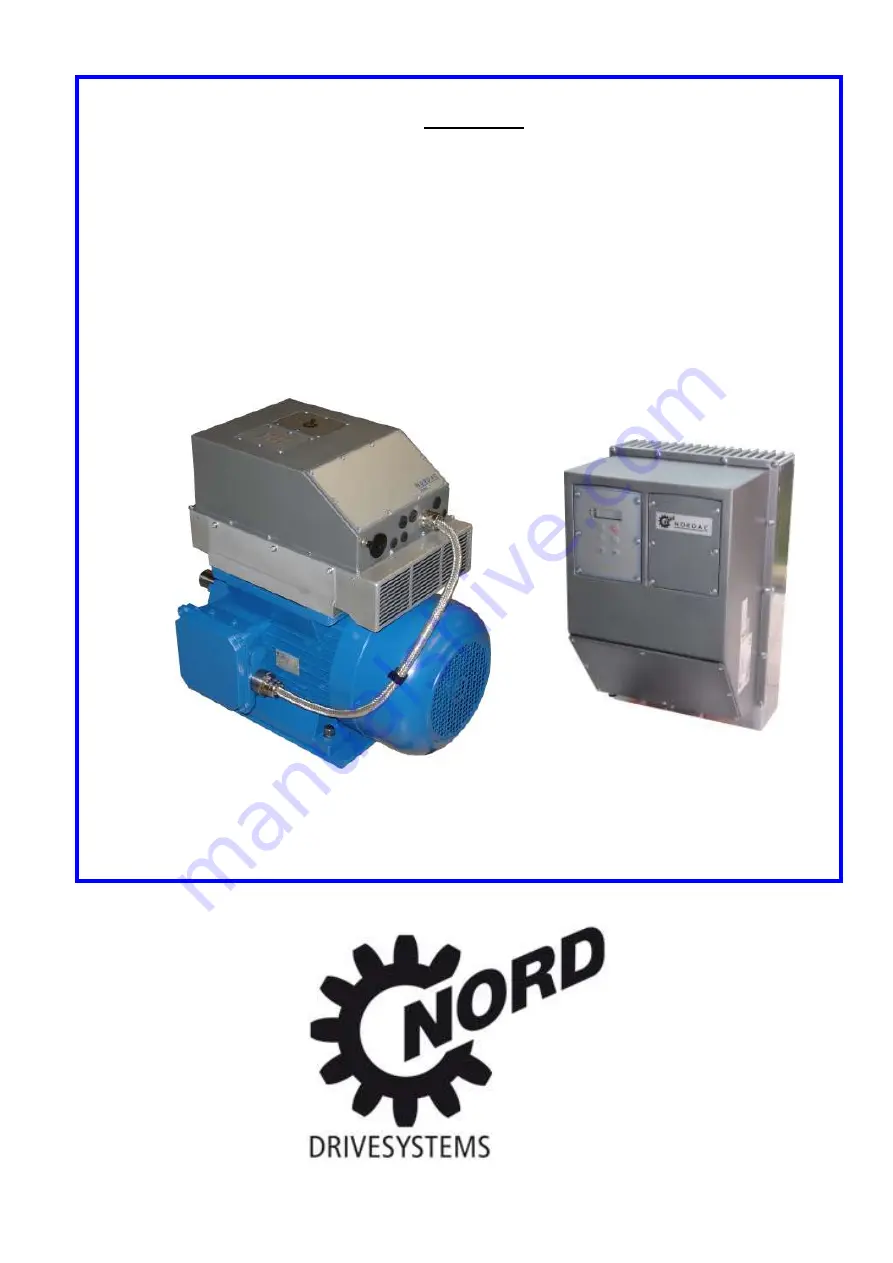
MANUAL
NORDAC SK 750E
Frequency Inverter
SK 750E-551-323-A (-W) ... SK 750E-112-323-A (-W)
(5.5kW … 11kW, 3~ 230V)
SK 750E-551-340-A (-W) ... SK 750E-222-340-A (-W)
(5.5kW … 22kW, 3~ 400V)
BU 0750 GB
Для
заказов
: +7(499)707-11-20 Email: [email protected]
8-800-511-65-88 (
Бесплатно
по
РФ
)