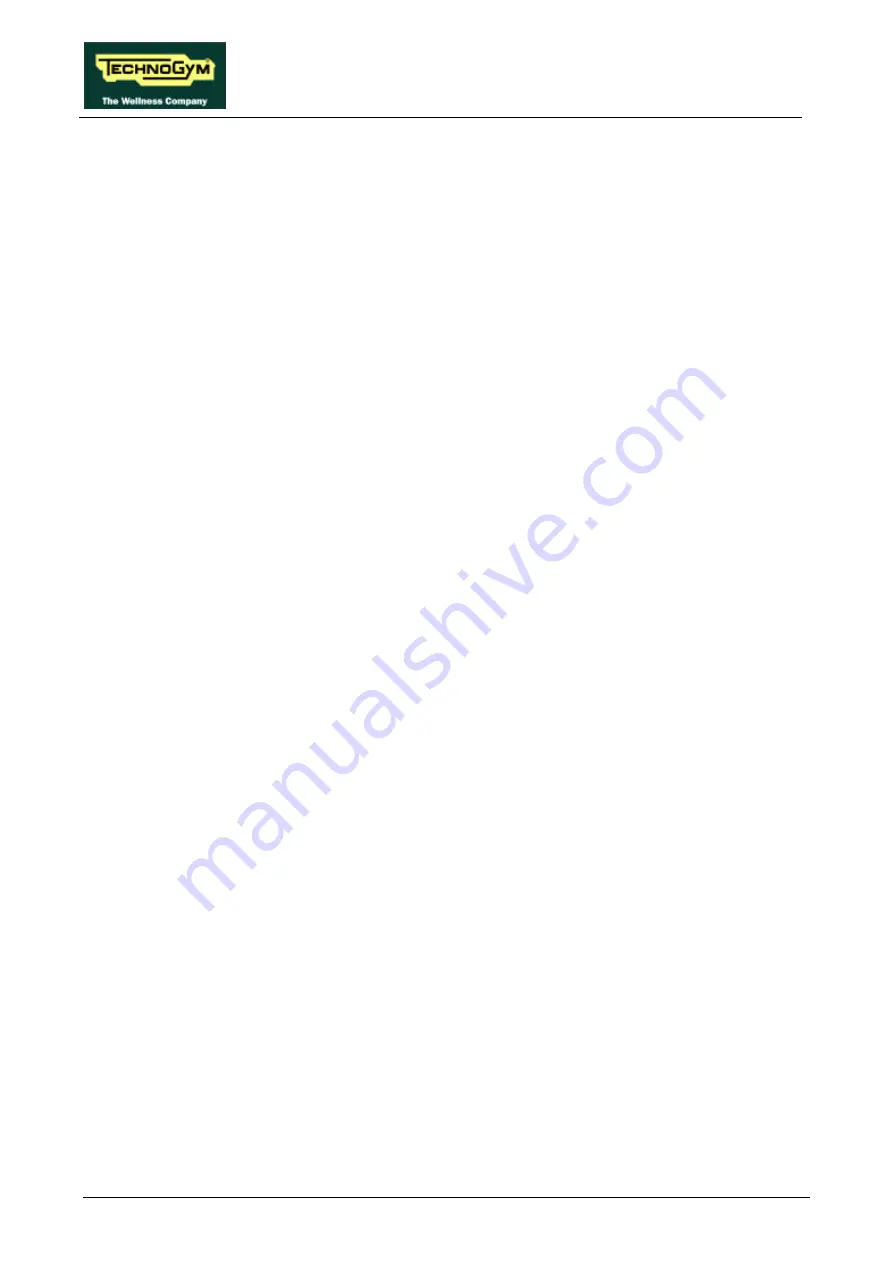
RUN XT: Service & Maintenance Manual - rev. 2.0
Page 5.2
5.3.
FIRST POWER-ON
After completing the installation procedure, the machine is ready to be powered up. To turn on the
machine, simply toggle the on/off switch from the 0 position to the 1 position.
When the machine is turned on it will perform a power-on test which:
•
sounds the buzzer;
•
lights all the LEDs.
•
resets the elevation
After completing this power-on test the machine enters standby mode, awaiting a keyboard
command.
To check the correct operation of the machine:
•
get on the machine;
•
press the "Start" key on the keyboard to begin exercising;
•
check that the belt motor starts;
•
press the “+” and “
−
” keys on the keyboard and check that the tread belt speed changes
accordingly;
•
press the “
↑
” and “
↓
“ keys on the keyboard and check that the machine elevation changes
accordingly;
•
put on the heart rate transmitter and check that the machine correctly measures the heart rate
value.
Summary of Contents for Run XT
Page 1: ...SERVICE MAINTENANCE MANUAL PRELIMINARY...
Page 2: ......
Page 4: ......
Page 8: ...RUN XT Service Maintenance Manual rev 2 0 Page iv Page intentionally left blank...
Page 26: ...RUN XT Service Maintenance Manual rev 2 0 Page 3 8 Page intentionally left blank...
Page 28: ...RUN XT Service Maintenance Manual rev 2 0 Page 4 2 Page intentionally left blank...
Page 68: ...RUN XT Service Maintenance Manual rev 2 0 Page 6 38 Page intentionally left blank...
Page 108: ...RUN XT Service Maintenance Manual rev 2 0 Page 8 10 Page intentionally left blank...
Page 116: ...RUN XT Service Maintenance Manual rev 2 0 Page 9 8 Page intentionally left blank...
Page 120: ...RUN XT Service Maintenance Manual rev 2 0 Page 10 4 Page intentionally left blank...
Page 130: ...RUN XT Service Maintenance Manual rev 2 0 Page 11 10 Page intentionally left blank...
Page 131: ......