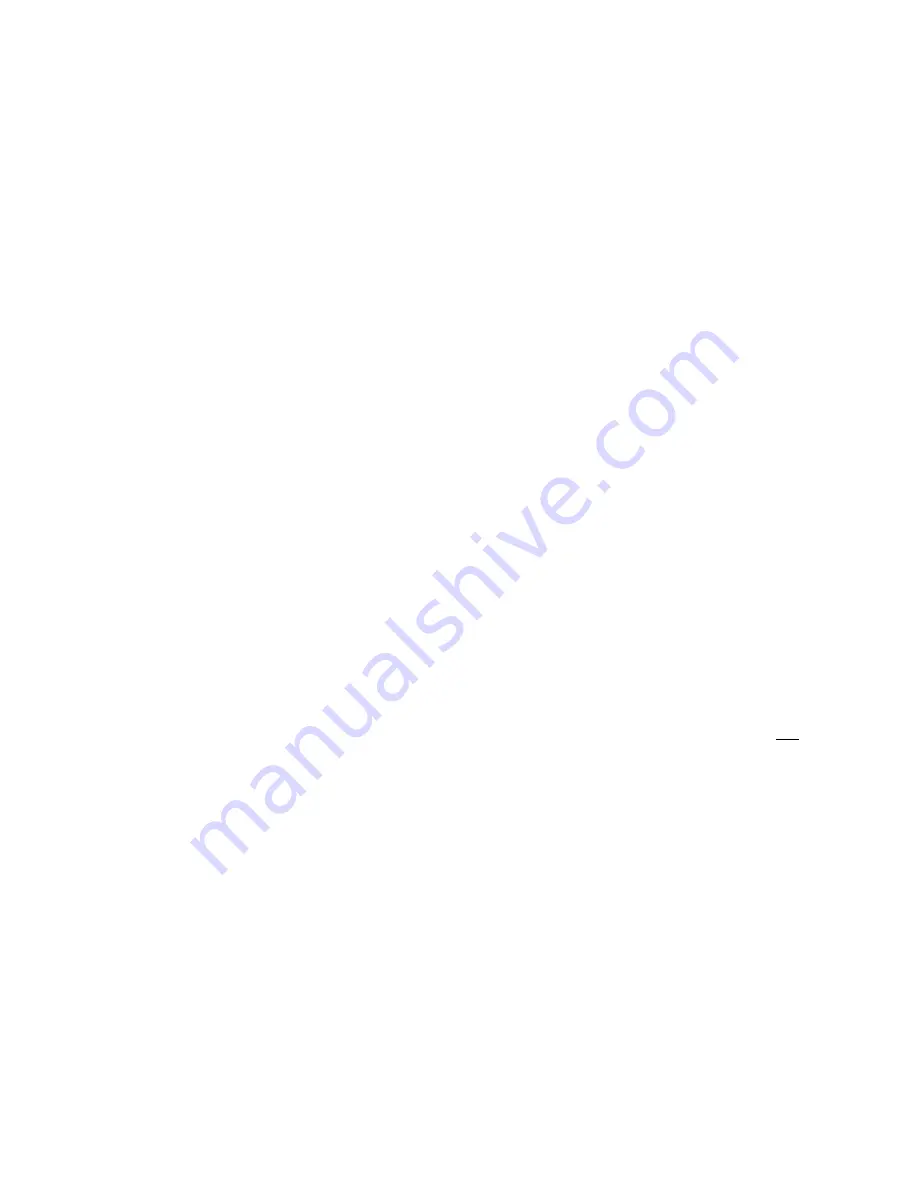
Principles
10
Principles
The CAN bus converter makes additional
interfaces
available for all CAN bus devices.
Furthermore, all the
function modules
in the X2 range are available. These allow bus input values to
be processed directly in the bus converter. The results of the functions can be transferred to other
devices as network outputs, visualised or logged.
It is programmed using TAPPS2 software. The CAN-BC2 can be operated via the UVR16x2 controller,
via CAN-MTx2 or via the C.M.I. interface.
Minimum system requirements
Programming
:
TAPPS2 version
1.10
Programming
Visualisation
:
TA-Designer version
1.17
Access
:
C.M.I. version
1.26.2
UVR16x2 version
V1.23
CAN-MTx2 version
V1.09
Datalogging
:
Winsol version
2.07
Interfaces
Potential-free CAN bus with increased interference resistance
The CAN-BC2 is used for
remote connection
within a controller network or by network groups. This
could be several groups of CAN bus connections and/or further remote CAN bus subscribers, for
example in a heating system.
This interface is electrically
isolated
from the primary CAN bus via an
optical
transmission path.
We recommend using a bus converter at both ends of a long cable, so that no critical electronic parts
are directly connected to the bus over the entire remote connection. The CAN-BC2 protects against
potential differences of
up to 1 kV
and can therefore
not
be considered to offer voltage surge
protection in the case of a lightning strike.
Note:
Every CAN bus subscriber is identified with its own
CAN node number
from a total of
62 possible node numbers. When designing the network, bear in mind that a bus converter does
not
disconnect the networks
from a data point of view
and therefore does not increase the number of
nodes available. As bus subscribers,
every single
converter is given its
own
node number. This
individual number is identical for both CAN sides (primary and potential-free).
M-Bus (measurement bus)
The M-Bus is a master/slave system for reading data from energy and volume meters (electricity,
heat, water, gas).
The CAN-BC2 is designed for up to 4 M-Bus "unit loads". Up to 4 M-Bus meters, each with 1 unit load,
can therefore be connected. The bus converter (master) cyclically reads the values from the individual
devices. The interval time is adjustable.
As a master, this bus converter is therefore suitable for the parallel connection of up to four
M-Bus meters (slaves).
In total
, a maximum of 32 M-Bus values can be read per bus converter. There must only be one
master in the M-bus system.