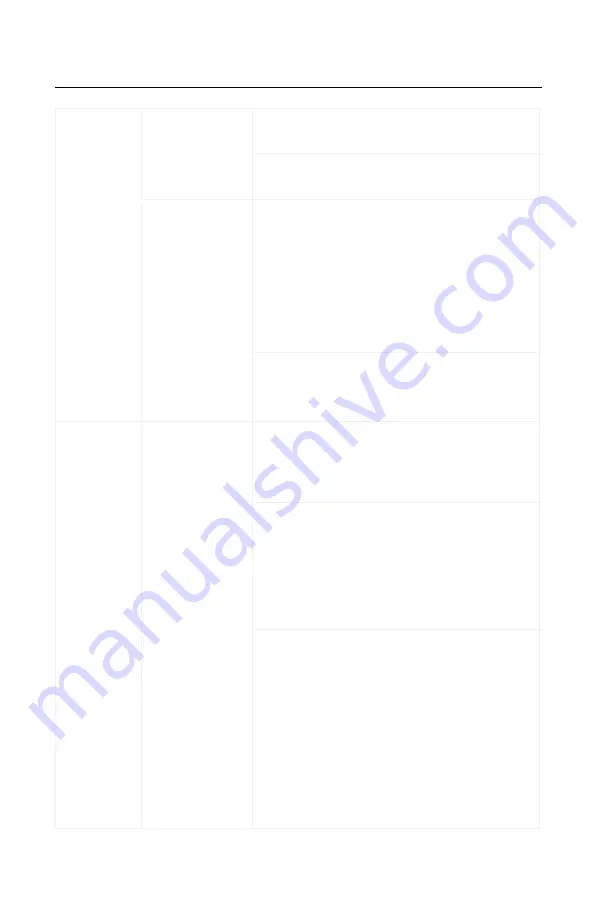
64
Section VII
– Maintenance
All Types
(Cont.)
Plug stopped
working
correctly.
Contaminated plug: install a new filter
pack version.
Wax build up in plug: consult with factory
on other plug option.
Trigger is
damaged.
Verify proper THREAD-O-RING was
used for corresponding wall thickness of
pipe. Measure the height of the THREAD-
O-RING as it is mounted to the pipe and
then add that measurement to the wall
thickness of the pipe. This measurement
should not exceed 4.50 inches but needs
to be greater than 4.25 inches.
Plug may have wax or other buildup
preventing the trigger from moving,
resulting in damage.
Electrical
or Combo
Electrical
switch is not
sending
electrical
signal.
Proper switch adjustment: refer to
electrical switch instruction in the manual
and ensure the switch is adjusted
properly.
Ensure that the double torsion spring is
still installed correctly.
Verify indicator is properly installed:
check indicator installation by removing a
set screw and looking for the groove on
the plug.
Verify that the plug is fully installed:
measure the distance the plug extends
above the THREAD-O-RING Nipple; the
distance should be 1-3/8 inches.
In the event of freezing weather: the seal
on the indicator may have been
compromised allowing water to enter the
upper position of the plug. This water can
freeze and not allow the magnet to move.
Remove indicator to check for moisture.
Summary of Contents for PIG-SIG V
Page 5: ...2018 All rights reserved T D Williamson Inc ii This page intentionally left blank...
Page 7: ...2 Section I Safety This page intentionally left blank...
Page 25: ...20 Section III Pipeline Not Under Pressure This page intentionally left blank...
Page 71: ...66 Section VII Maintenance This page intentionally left blank...