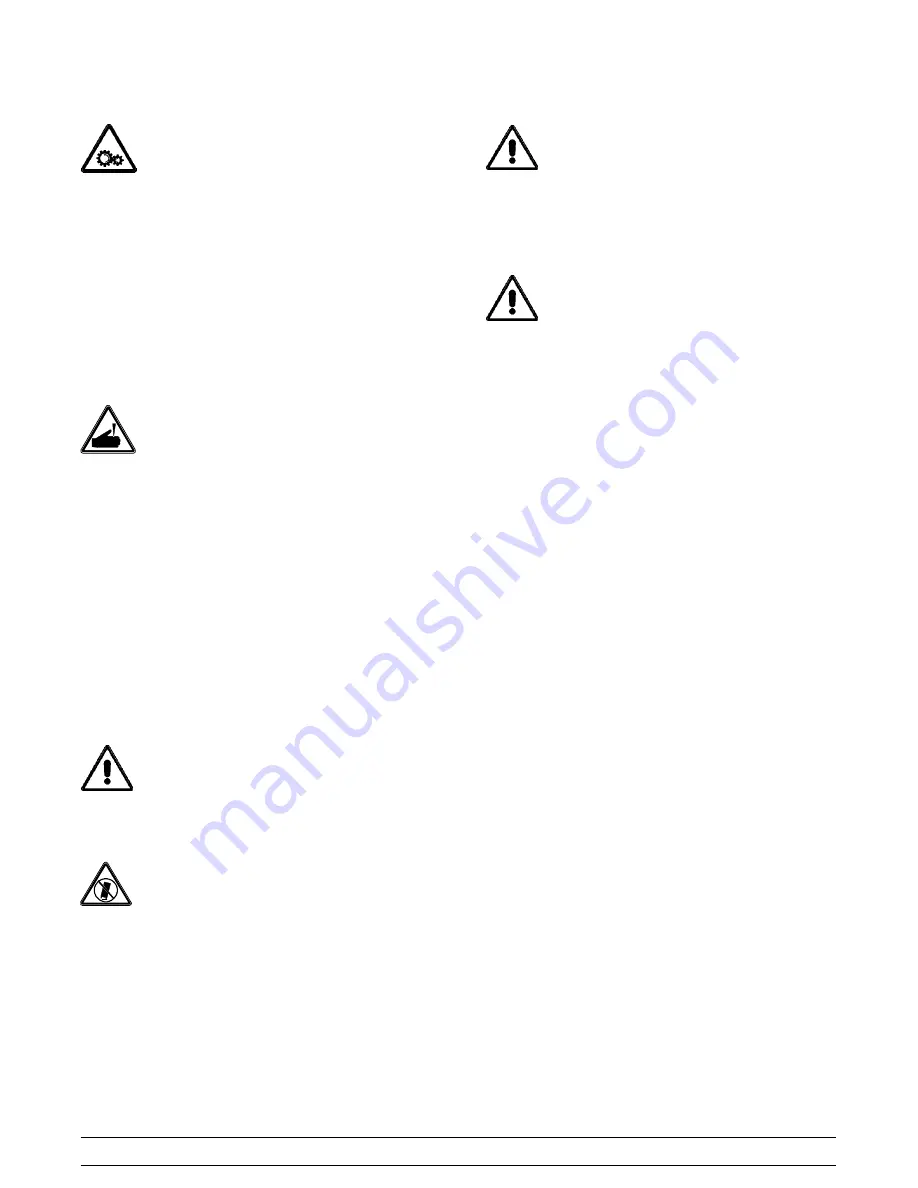
6
Models C708 & C716
Safety
130304
S
DO NOT
allow untrained personnel to
operate this machine.
S
DO NOT
operate the freezer unless all
service panels and access doors are
restrained with screws.
S
DO NOT
remove any internal operating
parts (example: freezer door, beater,
scraper blades, etc.) unless all control
switches are in the OFF position.
Failure to follow these instructions may result in
severe personal injury from hazardous moving parts.
This unit has many sharp edges that can
cause severe injuries.
S
DO NOT
put objects or fingers in the door
spout. This may contaminate the product
and cause severe personal injury from blade
contact.
S
USE EXTREME CAUTION
when removing
the beater asssembly. The scraper blades
are very sharp.
S
CAUTION-SHARP EDGES:
Two people are
required to handle the cup/cone dispenser.
Protective gloves must be worn and the
mounting holes must NOT be used to lift or
hold the dispenser. Failure to follow this
instruction can result in personal injury to
fingers or equipment damage.
Access to the service area of the unit is
restricted to persons having knowledge and practical
experience with the appliance, in particular as far as
safety and hygiene are concerned.
This freezer must be placed on a level
surface. Failure to comply may result in personal
injury or equipment damage.
Cleaning and sanitizing schedules are
governed by your state or local regulatory agencies
and must be followed accordingly. Please refer to
the cleaning section of this manual for the proper
procedure to clean this unit.
This machine is designed to maintain
product temperature under 41°F (5°C). Any product
being added to this machine must be below 41°F
(5°C). Failure to follow this instruction may result in
health hazards and poor freezer performance.
DO NOT
obstruct air intake and discharge openings:
C708:
A minimum of 6” (152 mm) air space is
required on both sides and 0” on the rear.
C716:
A minimum of 3” (76 mm) air space is
required on all sides. Install the deflector provided to
prevent recirculation of warm air.
Failure to follow these instructions may cause poor
freezer performance and damage to the machines.
For Indoor Use Only:
This unit is designed to
operate indoors, under normal ambient
temperatures of 70
_
-75
_
F (21
_
-24
_
C). The freezer
has successfully performed in high ambient
temperatures of 104
_
(40
_
C) at reduced capacities.
DO NOT
run the machine without product. Failure to
follow this instruction can result in damage to the
machine.
NOISE LEVEL:
Airborne noise emission does not
exceed 78 dB(A) when measured at a distance of
1.0 meter from the surface of the machine and at a
height of 1.6 meters from the floor.