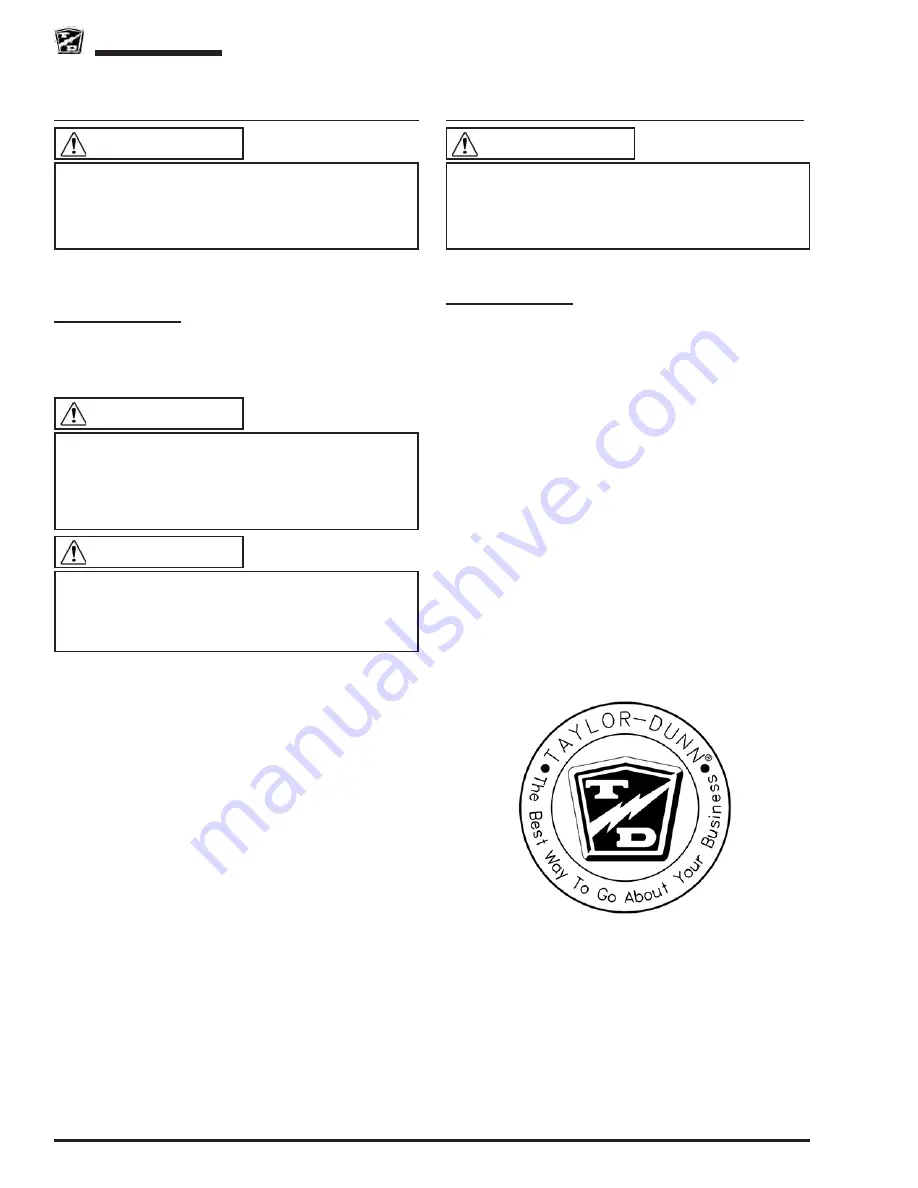
Suspension
Page 86
SS and MX Models, DC System
MS-534-13
This section is one section of a complete service
manual. Before starting any procedure, read all
warnings and instructions that are located in the
Service Guidelines chapter.
WARNING
REAR COIL SPRING AND SHOCK,
SS-534
There is a single coil spring on top of the drive axle and
a shock mounted to the rear.
Remove/Install
1: Raise the rear deck.
2: Remove the charger.
3: Remove the two shock bolts and remove the
shock.
4: Wrap a large heavy rag around the spring.
5: Raise the rear of the vehicle just high enough to
remove the spring. Refer to Raising the Rear of
the Vehicle in this chapter.
6: Install the spring onto the lower spring pad.
7: Carefully bend the spring over to mate with the
upper pad and SLOWLY lower the frame onto the
spring making sure it is indexed properly.
8: Install the shock.
REAR COIL SPRINGS, SS-536,
SS-546
There are two coil springs on the transaxle swing arm.
Remove/Install
1: Remove the rear deck cover.
2: Remove the upper and lower spring mounting
bolts.
3: Raise the rear of the vehicle just high enough to
remove the springs. Refer to Raising the Rear of
the Vehicle in this chapter.
4: Tap the two spring clips out of each spring.
5: Install the spring clips into the replacement
springs.
6: Place the springs onto the swing arm and
loosely thread the mounting bolts into each clip.
7: Lower the frame down onto the springs and
tighten the spring hardware.
The coil spring is bent into a small arc when in the
vehicle and may jump out of position when the frame
is lifted off of the spring.
Keep clear of the spring when lifting frame or it may
result in severe personal injury.
WARNING
DO NOT place hands or fingers between the spring
and frame.
This is a pinch point and may result in severe personal
injury.
WARNING
This section is one section of a complete service
manual. Before starting any procedure, read all
warnings and instructions that are located in the
Service Guidelines chapter.
WARNING
Summary of Contents for SS-025-34
Page 6: ......
Page 12: ...Page 12 MS 534 13 Introduction SS and MX Models DC System Notes...
Page 26: ...Lubrication Page 26 SS and MX Models DC System MS 534 13 Notes...
Page 30: ...PM Schedule Page 30 SS and MX Models DC System MS 534 13 Notes...
Page 66: ...Drive Motor Page 66 SS and MX Models DC System MS 534 13 Notes...
Page 78: ...Tires Wheels Page 78 SS and MX Models DC System MS 534 13 Notes...
Page 88: ...Suspension Page 88 SS and MX Models DC System MS 534 13 Notes...
Page 132: ...Replacement Parts Page 132 MS 534 13 SS and MX Models DC System Notes...
Page 133: ......