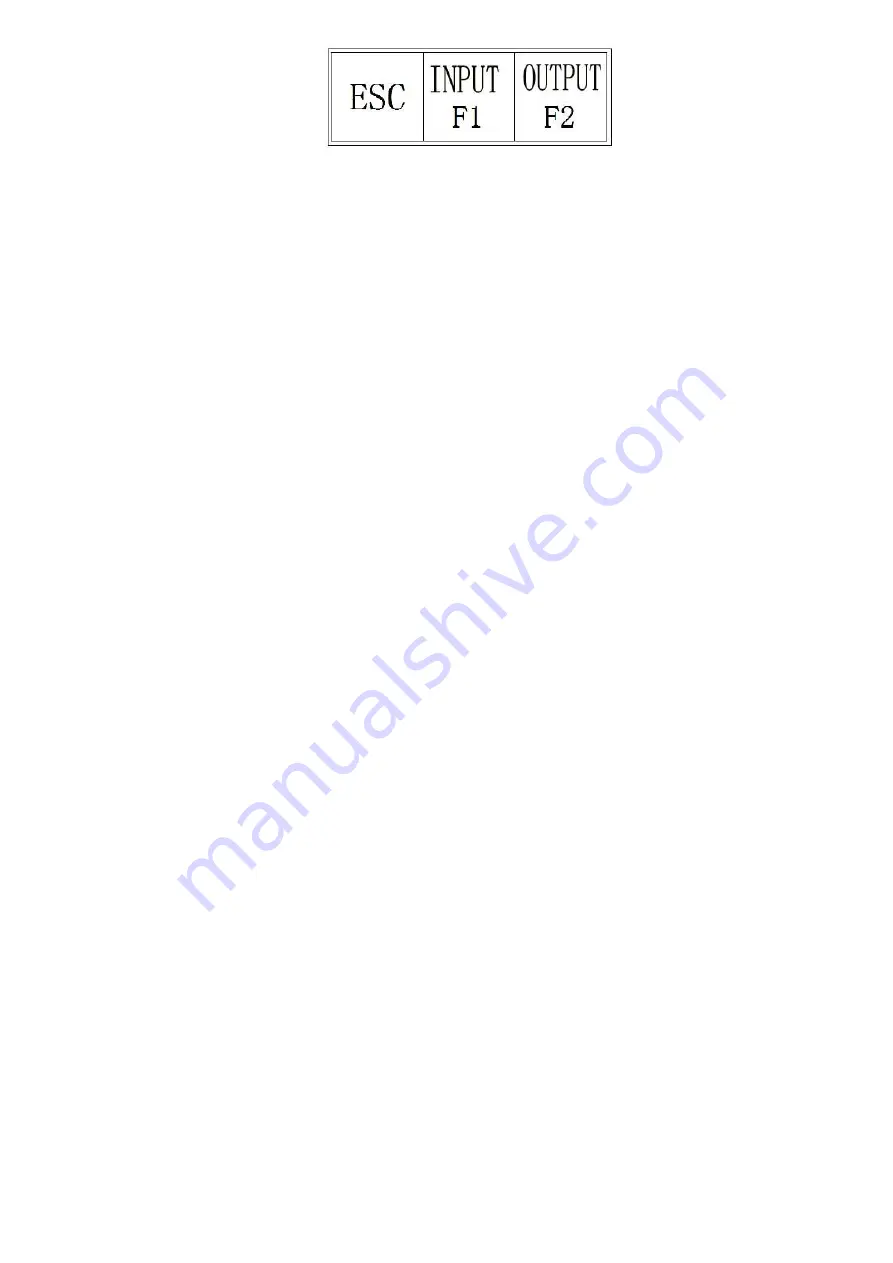
SF-2200H Flame / Plasma CNC Cutting System Operating Manual
14
【
F1
】
Load program file from removable disk to system
;
【
F2
】
Load program file from system to removable disk
4.1.7
、
【
F7
】
Find Parameters
This function is currently unavailable, saved for future upgrades.
图
4.2 Removable disk option menu