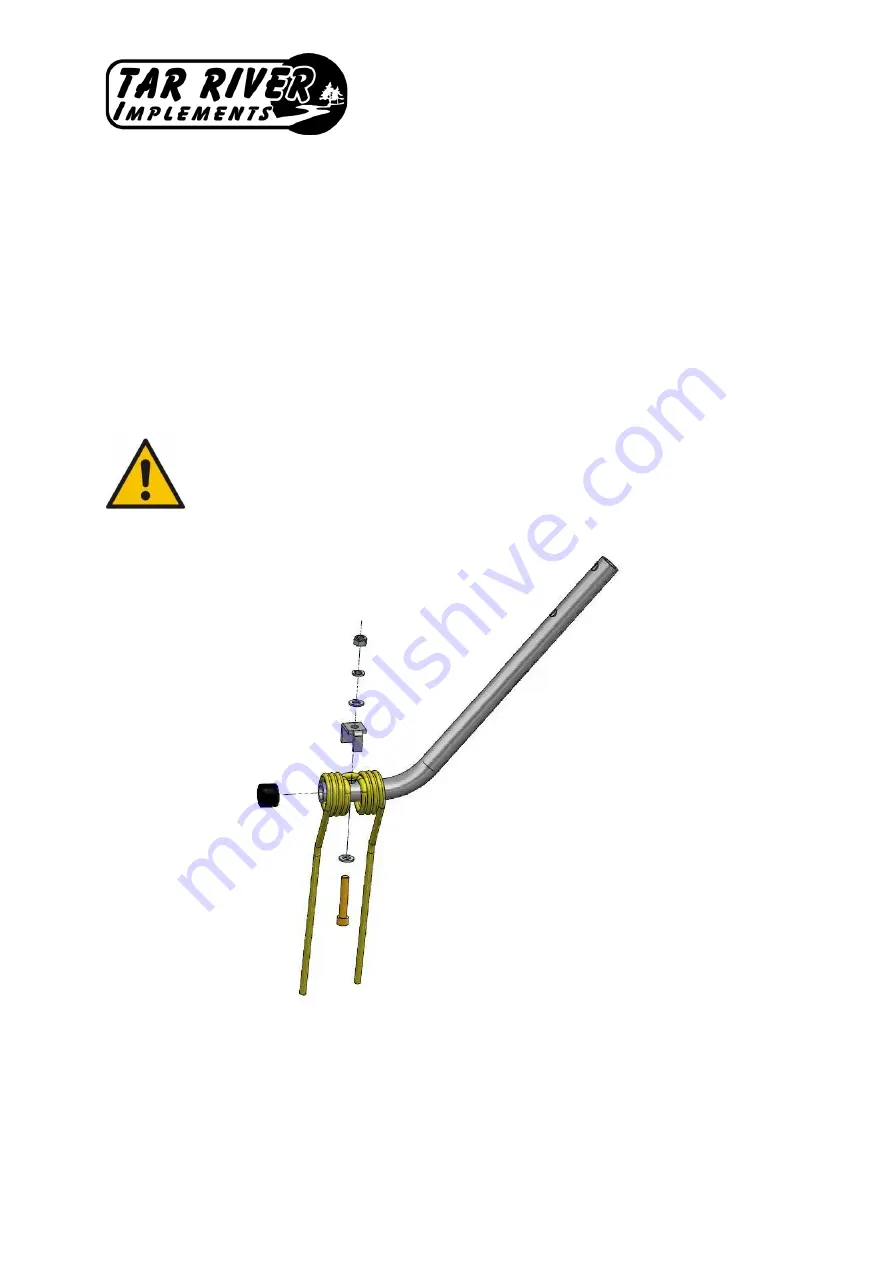
401 Jeffreys Road
Rocky Mount, NC 27804
Tel: 252-442-0700
6.6.5.
Tedder tines operation
The spring tines of the tedder are made of spring steel, thanks to which, they are highly
resistant to dynamic loads. Despite considerable durability, due to constant contact with
ground, the tines are subject to regular wear and tear. Additionally, due to vibrations, the
screw connections fastening tines to the arms may loosen. Therefore, check the technical
condition of each tine and the tension of each fastening screw before starting work. Replace
the tine if it is found to be damaged. The repair of a damaged tine is forbidden.
Caution!!!
The adjustments should be always performed by the vehicle and drive switched
off and on even ground. Immobilize the vehicle and the machine.
Fig. 16
Tedder tines operation