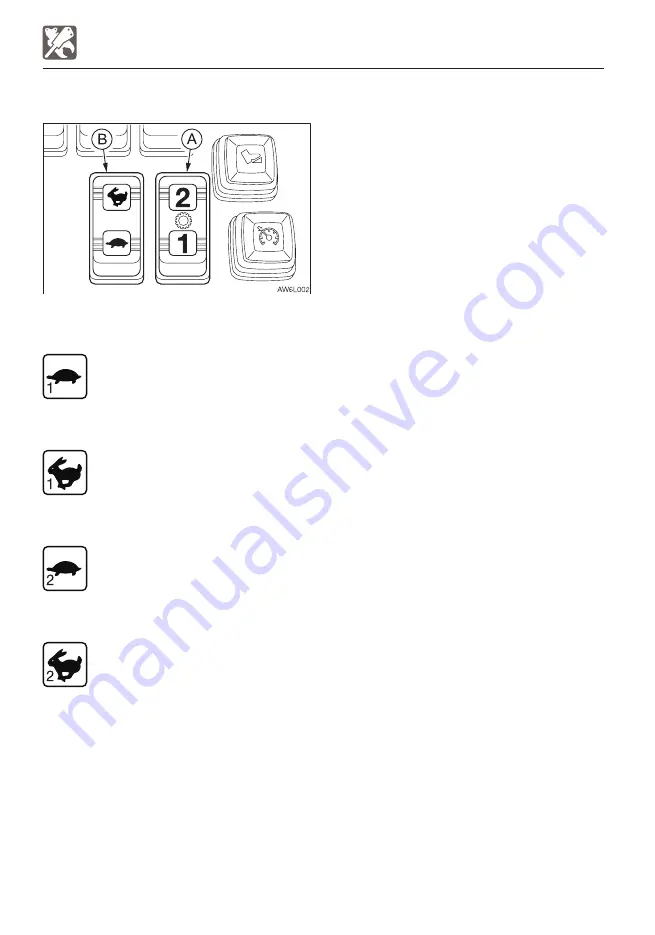
8-16
OPTIONS
4-SPEED TRAVEL SWITCH
4-SPEED TRAVEL SWITCH
Stop the machine and lock the brake pedal
before shifting gears between low and high.
Low-speed travel 1: 0 to 5.1 km/h
(3.17 mph)
Depress “1” on the switch (A) and
the “Turtle” symbol on the low/
high-speed travel switch (B).
High-speed travel 1: 0 to 15.2 km/h
(9.42 mph)
Depress “1” on the switch (A) and
the “Hare” symbol on the low/
high-speed travel switch (B).
Low speed travel 2: 0 to 9.8 km/h
(6.09 mph)
Depress “2” on the switch (A) and
the “Turtle” symbol on the low/
high-speed travel switch (B).
High-speed travel 2: 0 to 29.2 km/h
(18.14 mph)
Depress “2” on the switch (A) and
the “Hare” symbol on the low/
high-speed travel switch (B).
Summary of Contents for 190100003
Page 1: ......
Page 11: ...1 1 SAFETY...
Page 50: ...1 40 SAFETY SAFETY SIGNS DECALS...
Page 51: ...1 41 SAFETY SAFETY SIGNS DECALS...
Page 52: ...1 42 SAFETY SAFETY SIGNS DECALS...
Page 53: ...2 1 CONTROLS...
Page 77: ...2 25 MEMO...
Page 126: ...2 74...
Page 127: ...3 1 OPERATION...
Page 155: ...3 29 MEMO...
Page 158: ...3 32...
Page 159: ...4 1 TRANSPORT...
Page 163: ...4 5 TRANSPORT Hoisting posture HOISTING THE MACHINE...
Page 166: ...4 8...
Page 167: ...5 1 MAINTENANCE...
Page 217: ...5 51 MEMO...
Page 229: ...5 63 MEMO...
Page 235: ...5 69 MEMO...
Page 246: ...5 80...
Page 247: ...6 1 TROUBLESHOOTING...
Page 255: ...6 9 MEMO...
Page 271: ...7 1 SPECIFICATIONS...
Page 278: ...7 8 SPECIFICATIONS OPERATING RANGES OPERATING RANGES...
Page 280: ...7 10 MEMO...
Page 282: ...7 12 SPECIFICATIONS 2 Piece boom LIFTING CAPACITIES...
Page 283: ...7 13 SPECIFICATIONS 2 Piece boom LIFTING CAPACITIES...
Page 284: ...7 14 SPECIFICATIONS Mono boom LIFTING CAPACITIES...
Page 285: ...7 15 SPECIFICATIONS Mono boom LIFTING CAPACITIES...
Page 286: ...7 16...
Page 287: ...8 1 OPTIONS...
Page 303: ...8 17...