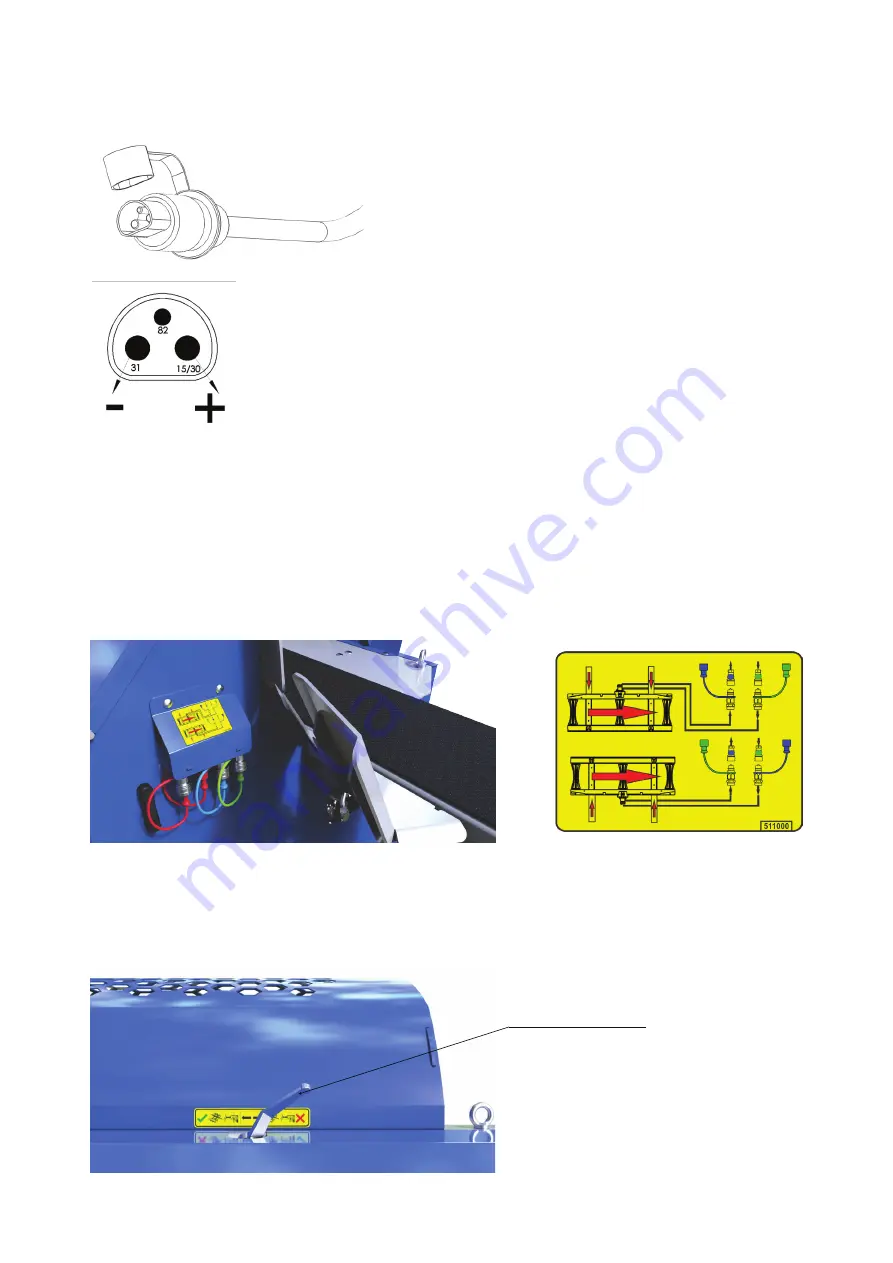
4.1. CONNECTING TO THE MAINS CIRCUIT
Plug the 3 pin plug into the tractor mains or EP unit
(optional).
Check that the power source provides a constant 12 V
voltage and 16 A current; otherwise, this may lead to faulty
operation of the electrical system. Minimum cross-section
of the cables from the power source should be 2,5 mm².
4.2. ADDITIONAL EQUIPMENT SETUP
14
4.2.1. ATTACHING THE LOADING DECK TO THE MACHINE’S HYDRAULIC
CONTROL SYSTEM
• Use the quick couplings to connect the loading deck’s hydraulic pipes and the machine couplings.
To ensure proper connection observe the label and the color covers of the couplings.
• If the hydraulic couplings are not installed or if the loading deck is not in operation, place the
selector valve in the appropriate position (X).
Selector valve
After operation always disconnect the supply cables; otherwise, the tractor battery may begin to
discharge.
Summary of Contents for RCA 480 JOY
Page 39: ...8 2 LOADING WITH THE HELP OF LIFTING STRAPS 39 TRANSVERSELY L 3 m ...
Page 43: ...43 ...
Page 44: ...44 ...