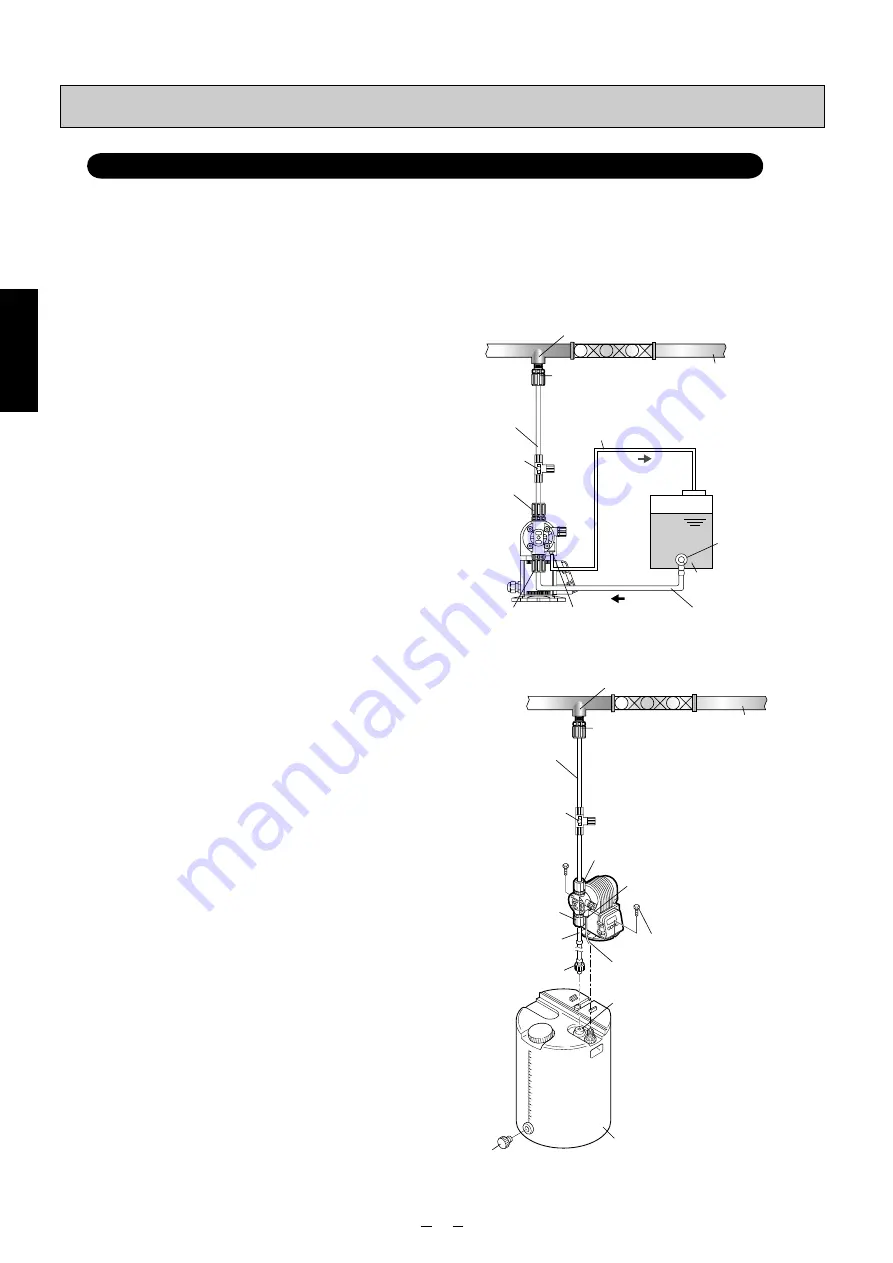
13
Installation
Pump-mounting bolts (2 sets)
Foot valve
Drain cock
Suction-pipe cover
Tank
Relief/air-release hose
Main pipe
Anti-siphon check valve
Injection point
Discharge-
side pipe
Discharge-side joint
Suction-side joint
Suction-side pipe
Relief/air-release port
3-way valve
Main pipe
Anti-siphon check valve
Relief/air-release hose
Tank
Suction-side pipe
Suction valve
Injection point
3-way valve
Discharge-
side pipe
Discharge-
side joint
Relief/air-release port
Suction-side joint
Installation is described with an example using a TACMINA tank.
• If the valve has not been opened or clogging by foreign matter has occurred inside the pipe at the discharge side of
the pump, the chemical will gush out from the relief/air-release port. Therefore, always have a relief/air-release hose
installed, and lead its end back into the tank or other container.
• Install a valve for releasing abnormal pressure that has built up inside the discharge-side pipe. The 3-way valve on the
washing water line may be used instead.
Piping
■
When installing the pump
below the tank
(1) Connect the suction valve of the tank and the suction-
side joint of the pump using the hose/tube.
(2) Connect the discharge-side joint of the pump and
main pipe (injection point) using the hose/tube.
When doing this, attach the anti-siphon check valve
at the injection-point side end of the hose/tube.
(3) Return the end of the relief/air-release hose which
has already been attached to the relief/air-release
port to the tank or other container.
✽
It is also recommended that a valve, meter, etc. be
installed to make it easy to carry out maintenance
and other such jobs.
■
When installing the pump
above the tank
(1) Using the pump-mounting bolts provided, secure the
pump to the prescribed position on top of the tank.
(2) Pass the suction-side hose/tube with foot valve
attached through the hole in the suction-pipe cover
on top of the tank, and connect it to the suction-side
joint of the pump. At this time, adjust the length of
the hose/tube and cut it so that the foot valve is 30
mm higher than the bottom of the tank.
(3) Connect the discharge-side joint of the pump and
main pipe (injection point) using the hose/tube.
When doing this, attach the anti-siphon check valve
at the injection-point side end of the hose/tube.
(4) Return the end of the relief/air-release hose which
has already been attached to the relief/air-release
port to the tank or other container.
✽
Installing the pump above the tank is not recommend-
ed for chemicals in which air bubbles tend to form.
✽
This pump’s static suction head is −1.5 m for water.
Its suction capability may decrease when the valve
seats inside the pump head are dry.
✽
Be absolutely sure to connect the foot valve provided
to the end of the suction-side hose/tube to prevent
dirt or foreign matter from entering the pump head
and valve seat area.
✽
It is also recommended that a valve, meter, etc. be
installed to make it easy to carry out maintenance
and other such jobs.
Model w/ relief-valve function for injection of general chemicals: PZD-30R/60R/100R
09-32̲PZD総合取説̲E.indd 13
09-32̲PZD総合取説̲E.indd 13
2010/07/22 8:42:27
2010/07/22 8:42:27