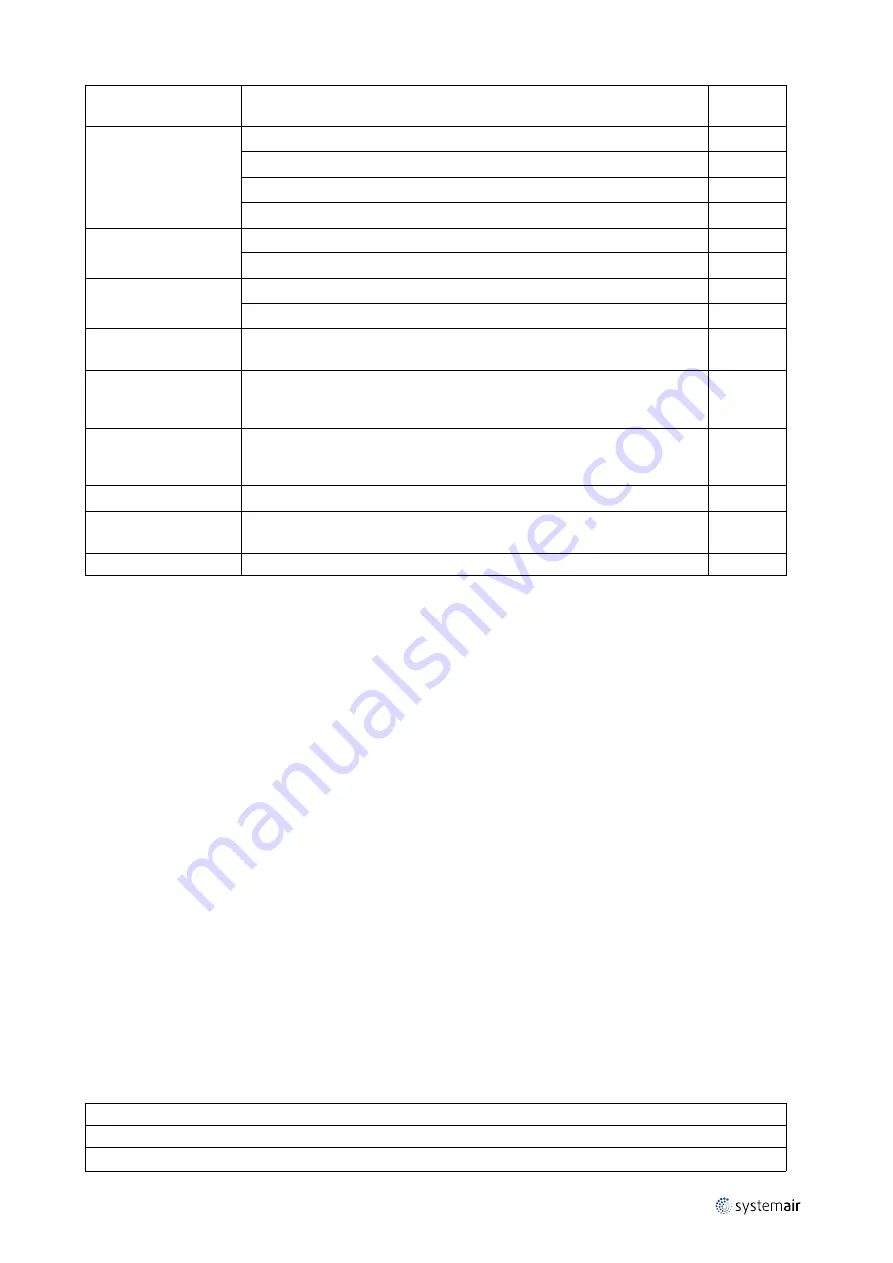
Adjustment and maintenance operations |
47
Function
Maintenance
Number
per year
Hot water coil
Check the dirt accumulation and clean, if needed.
1
Bleeding, if needed.
1
Test of frost protection sequence
1
Test of circulation pump
1
Electric heating coil
Check dirt accumulation and clean, if needed.
1
Test the function of the system with the fuses for the safety.
1
Cooling coil
Check dirt accumulation and clean, if needed.
1
Test the frost protection (glycol)
1
Heat pump unit
Mandatory annual control of the heat pump system. Must be done by
certified technician from a certified company.
1
Condensate drain
Cleaning of tray, water trap and outlet. Check the electrical heating between
insulation and pipes, if installed. Check and clean on demand and always
minimum twice a year.
2
Saving- and comfort
functions
Test of CO2 sensor, humidity sensor, motion sensor, pressure transmitters
for air capacity control, extended operation via button, cooling recovery, free
cooling
1
Fire alarm
Test of thermostats, smoke detectors and fire detection systems
1
Battery in controller
Change the battery on demand by alarm in the control panel and always
change the battery as a minimum every 5. Year.
1
Remote control
Test of Communications.
1
R.4
Filters – always replace filters with new filters with the same characteristics as
original filters to maintain SFP value
Filters in supply air and in extract air always have the same sizes of frames and the number of filters for supply air and
extract air are always the same. REMEMBER to order filters for supply air as well as for extract air.
To maintain the factory-calculated SFP values for the air-handling unit, it is very important that filters with the same
characteristics for start pressure as well as lifetime replace factory-mounted filters.
To achieve the most favourable SFP values, the factory-mounted filters represent the lowest achievable start pressure
as well as the longest achievable lifetime. If other filters with higher start pressure and shorter lifetime replace the fac-
tory-mounted filters, the user will experience smaller airflow and/or consumption of more electricity, and the SFPv val-
ue calculated by Systemair according to the Eurovent certification will not be achieved. Poor SFPv values will be
detected by tests according to commissioning standards, DGNB, LEED or BREEAM sustainability standards and locally
defined performance standards (the SFPv is with new clean filters).
Filter frame for bag filters must be of NON-PVC plastic to ensure safe disposal by incineration.
For each individual air handling unit you will find the data for the factory-mounted filters in Annex 2 that is always pro-
vided in a cover placed inside the air handling unit when the air handling unit is delivered to the final site. Annex 2 is al-
so always available from Systemair if you can inform us of the production number of the air handling unit. The
production number is always printed on the so-called machine card that is attached to the unit. You will find an example
of this machine card in section d.2.1 of this manual.
The factory-mounted filters comply with indoor air quality demands of customers and with the SFP values according to
local legislation.
The filters comply with the filter classes according to the new test standard EN ISO 16890:2016 valid from 1 January
2019.
Filter classes according to the old test standard EN 779:2012 and the new test standard EN ISO 16890:2016 are listed
below:
G4 — coarse 60%
M5 — ePM10 60%
M6 — ePM2,5 50%
output |