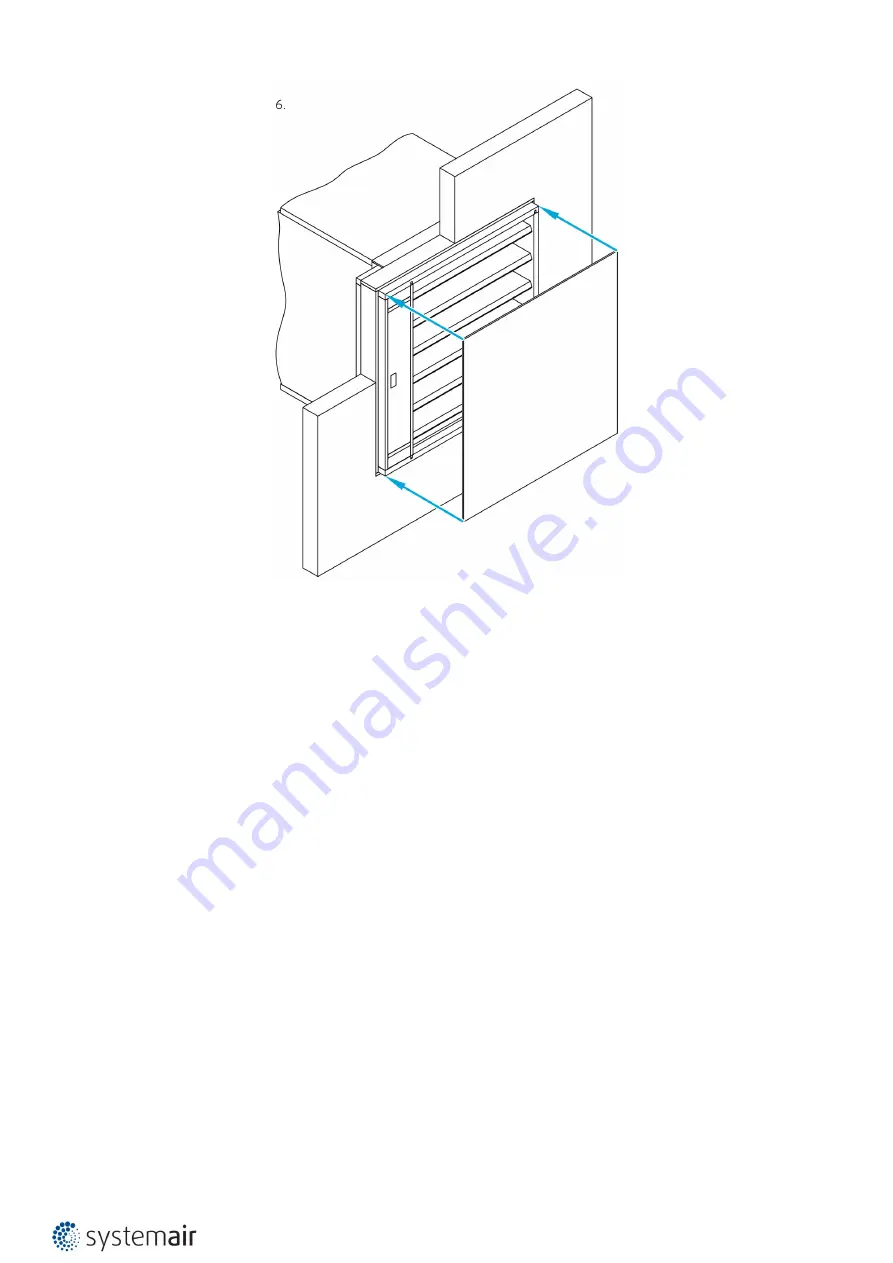
102/105 |
S-BM2
Legend
Y1, Y2, Y3, Y4
- Cutting plane
a)
- For wall installation - insert the filling as per desired installation.
b)
- For duct installation – fix the hangers so that the weight of the damper is supported.
Operation Manual
After installation, it is necessary to adjust the damper into its operating position “closed”. In case, that the damper is
used for extraction of pollutants, adjust the damper into its operating position “open”.
Connect the actuator to the relevant electric power supply as per Electrical connections section. The actuator is
activated and adjusts the damper into its operating position.
Warning
Some damper parts may have sharp edges; therefore, to protect yourself, please use gloves during damper installation
and manipulation. In order to prevent electric shock, fire or any other damage which could result from incorrect
damper usage and operation, it is important to:
1.Ensure that installation is performed by a trained person.
2.Follow the written and depicted instructions provided within this User Manual closely.
3.Perform damper inspection in accordance with this User Manual.
4.Check the damper’s functionality as per the “Smoke Damper Functionality Check” chapter before you install the
smoke damper. This procedure prevents the installation of a damper that has been damaged during transportation or
handling.
Summary of Contents for A-S-BM2
Page 1: ...S BM2 Smoke Control Damper MA multi ...
Page 16: ...16 105 S BM2 Dimensions of grille type M0 M1 in battery type assembly ...
Page 26: ...26 105 S BM2 ...
Page 27: ...27 105 S BM2 ...
Page 28: ...28 105 S BM2 ...
Page 29: ...29 105 S BM2 Opening and wall ceiling preparations ...
Page 30: ...30 105 S BM2 Damper minimum distances ...
Page 32: ...32 105 S BM2 Battery Installation Grille type M0 M1 ...
Page 33: ...33 105 S BM2 ...
Page 34: ...34 105 S BM2 Fixing layout for battery installations ...
Page 35: ...35 105 S BM2 Opening and wall ceiling preparations Damper minimum distances ...
Page 38: ...38 105 S BM2 ...
Page 39: ...39 105 S BM2 ...
Page 40: ...40 105 S BM2 ...
Page 41: ...41 105 S BM2 Opening and wall ceiling preparations Damper minimum distances ...
Page 44: ...44 105 S BM2 ...
Page 45: ...45 105 S BM2 ...
Page 46: ...46 105 S BM2 ...
Page 47: ...47 105 S BM2 Opening and wall ceiling preparations ...
Page 48: ...48 105 S BM2 Damper minimum distances ...
Page 51: ...51 105 S BM2 ...
Page 52: ...52 105 S BM2 ...
Page 53: ...53 105 S BM2 Opening and wall ceiling preparations Damper minimum distances ...
Page 55: ...55 105 S BM2 Battery Installation Grille type M0 M1 ...
Page 56: ...56 105 S BM2 ...
Page 57: ...57 105 S BM2 Fixing layout for battery installations ...
Page 58: ...58 105 S BM2 Opening and wall ceiling preparations Damper minimum distances ...
Page 61: ...61 105 S BM2 ...
Page 62: ...62 105 S BM2 ...
Page 63: ...63 105 S BM2 ...
Page 64: ...64 105 S BM2 Opening and wall ceiling preparations Damper minimum distances ...
Page 67: ...67 105 S BM2 ...
Page 68: ...68 105 S BM2 ...
Page 69: ...69 105 S BM2 Opening and wall ceiling preparations ...
Page 72: ...72 105 S BM2 ...
Page 75: ...75 105 S BM2 ...
Page 78: ...78 105 S BM2 ...
Page 79: ...79 105 S BM2 ...
Page 82: ...82 105 S BM2 ...
Page 83: ...83 105 S BM2 ...
Page 84: ...84 105 S BM2 ...
Page 87: ...87 105 S BM2 ...
Page 88: ...88 105 S BM2 ...
Page 89: ...89 105 S BM2 ...
Page 90: ...90 105 S BM2 ...
Page 100: ...100 105 S BM2 ...
Page 101: ...101 105 S BM2 ...
Page 105: ...Systemair DESIGN 2021 06 29 Handbook_S_BM2_en GB ...