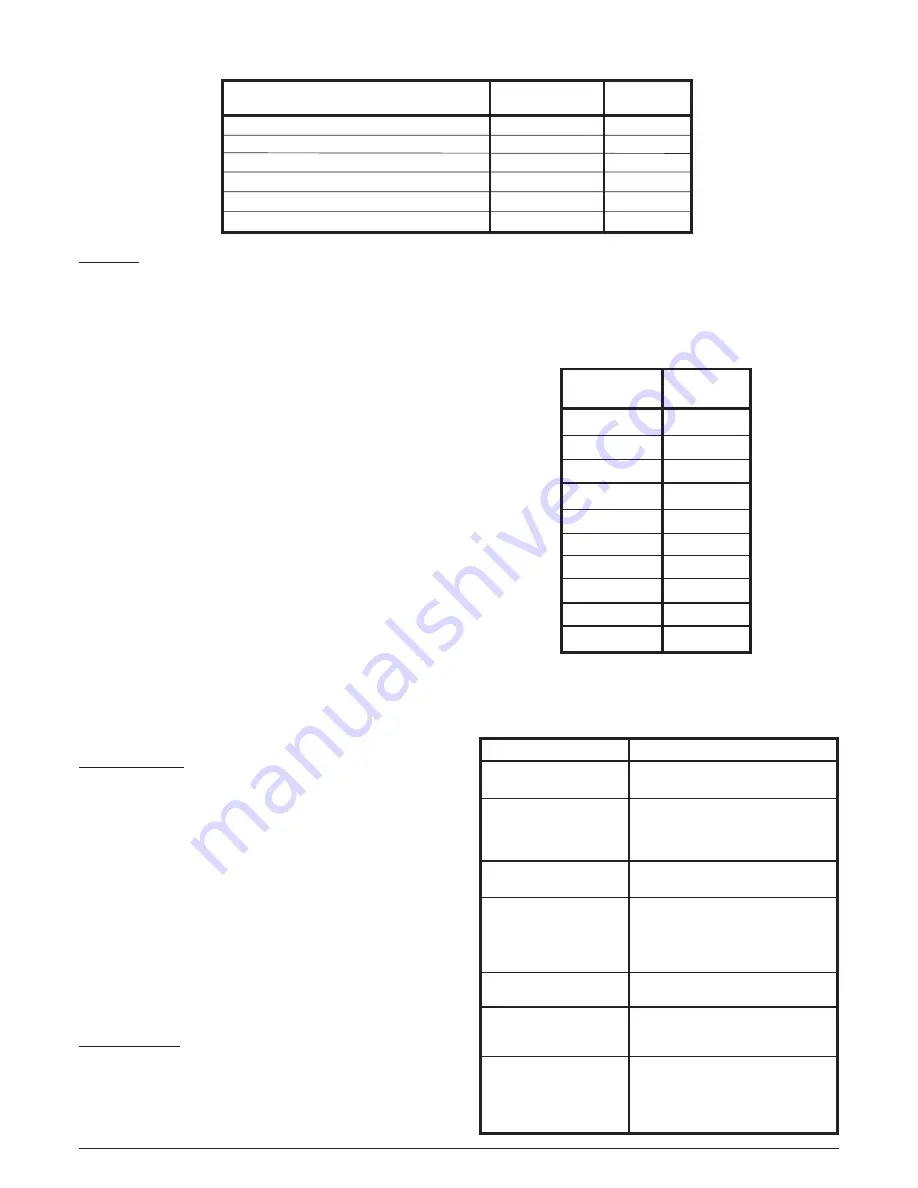
10
D200-41-00
Pittway Tecnologica S.r.l, Via Caboto 19/3, 34147 Trieste, Italy
TESTING
Testing should only be carried out by qualified
personnel. Before undertaking any testing ensure that
the proper authorities have been informed, and if
necessary, that the unit has been isolated from the fire
control panel to prevent unwanted alarms.
Sensor Testing
With the unit powered up and the top cover removed
the sensors can be tested for functionality using methods
described by the manufacturer (for example aerosol spray
or magnet test).
System Testing
Alarm: The installed system must be checked with the top
cover securely fitted. As a minimum, smoke should be
introduced to the furthest sampling point from the A300E
unit on each branch of the pipe. The choice of smoke
source is dependant on the installation but in all cases the
smoke must be present for the duration of the test –
aerosol sprays for point detectors DO NOT work on
aspirated systems.
If it is possible to get close to the sampling point then a
basic, functional check can be carried out with smoke
matches or lighted taper etc. But for measurable
performance tests then refer to Appendix A of the FIA Code
of Practice for Aspirating Systems to select the
appropriate test for the installation.
Fault: Simulate a fault on the A300E unit (for example,
remove the power) and check that a fault is signalled at the
fire panel.
MAINTAINANCE
With normal use, the filter elements will eventually become
contaminated with dust particles, impeding airflow. It is
recommended that it be changed every six months.
To change the filter:
1. Unscrew the top cover
2. Lift out the foam filter elements from its housing
3. Fit a new filter kit so that it lies flush with the top of its
housing
4. Replace the top cover
5. Test the unit as described above.
IMPORTANT
To ensure maximum efficiency and longevity of the filter,
when fitting the replacement filter element kit, the Coarse
filter needs to be fitted first into the pipe.
ACCESSORIES
The following accessories are available to order:
Model Number
Product
02-FL50
Replacement Filter Element Kit
20-LA0015
Replacement Key to Open Detector
Table 5: Problem Solving
Table 4: A300E Current Consumption
Fan Speed
Current mA
Bargraph Value
0
110
1
120
2
130
3
150
4
170
5
190
6
220
7
235
8
265
9
300
Table 3: Typical Flow Sensitivity Settings
PIPE SETUP
RECOMMENDED
FLOW
(all 50m lengths unless otherwise stated)
FAN SPEEDS
SENSITIVITY
13 x 3mm Sampling Holes, 1 x 6mm End Hole
9
9
8 x 3mm Sampling Holes, 1 x 6mm End Hole
6-9
9
4 x 3mm Sampling Holes, 1 x 6mm End Hole
6-9
7
1 x 5mm Sampling Hole, 1 x 5mm End Hole
6-9
5
1 x 8mm End Hole
5-9
2
1 x 8mm End Hole (10m Pipe)
3-9
1
Problem
Possible Solutions
Power light flashing.
Ensure supply to external power
connector within limits.
No lights on display.
Ensure supply leads correctly
Fan not running
orientated. Ensure that FUSE
correctly seated in socket and fuse
not blown.
No lights on display.
Ensure ribbon cable fully seated into
Fan running OK.
main & display boards.
Flow HI/LO light on
Ensure sampling pipes correctly
installed, lid fitted and box fully sealed.
Ensure filters not blocked.
Ensure flow calibration procedure has
been carried out
Flow reading on Bargraph Decrease Flow sensitivity setting
display moves erratically.
and re-calibrate air flows
Flow reading on
Increase Flow sensitivity setting
Bargraph unresponsive
and re-calibrate air flows
to broken/blocked pipes
Sensor(s) unresponsive
Ensure sampling pipe installed correctly
to smoke tests
and undamaged. Ensure that holes
and pipe length do not exceed limits
for detector. Ensure that
recommended test method is used.